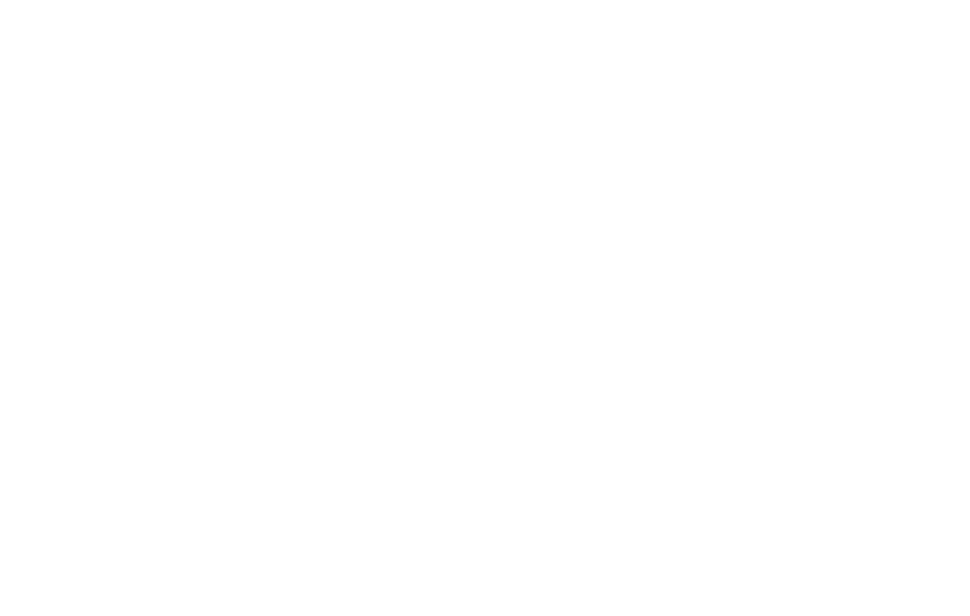
Ранее серьезные проблемы возникали в связи с накоплением минераль-
ных и других примесей, остающихся в составе ПУМ в виде золы. Да и механи-
ческая прочность получаемого материала была недостаточно высока. Техноло-
гия сибунитов решает все эти задачи. Поэтому она запатентована в США и дру-
гих странах. Полупромышленное производство сибунитов организовано в Кон-
структорско-технологическом институте технического углерода СО РАН, пер-
вые опытные партии его закуплены рядом отечественных предприятий и зару-
бежных фирм.
История другого − термокаталитического метода выработки углеродных
композитов началась в конце XIX века, когда американцы Хьюгес и Чемберс
обнаружили и в 1889 году запатентовали способ получения углеродных воло-
кон при пиролизе смеси метана и водорода в железном тигле, а на рубеже
1920-1930-х годов Фишер и Гофман (Германия) впервые описали образование
тех же волокон при разложении окиси углерода на железе. Оказалось, причина
их появления − так называемая каталитическая коррозия. От нее разрушаются
металлические дымоходы, химические реакторы, трубопроводы: при обработке
органических соединений образовываются побочные продукты в виде катали-
тического волокнистого углерода (KBУ); он-то и действует столь негативно.
Много лет усилия специалистов были направлены на борьбу с этим явлением.
В Институте катализа им. Г.К. Борескова СО РАН занялись не только
борьбой с ним, но и поиском условий и катализаторов, позволяющих получать
максимальное количество углерода на единицу массы последних до момента их
полной дезактивации, используя наиболее дешевые углеродсодержащие газы
(например, метан). И работа увенчалась успехом.
Дезактивация – потеря способности катализатора разлагать углеродсо-
держащие газы на углерод и водород.
На сегодня к лучшим можно отнести никелевые и никелево-медные ка-
тализаторы, содержащие 75 - 90 % металла и позволяющие получать из метана
при температуре примерно 500
0
С до 300 г КВУ на 1 г исходного катализатора,
в соответствии с рисунком 10. В результате газ трансформируется в ПУМ, со-
держащий всего до 0,3 % минеральных примесей (меньше, чем в природном
графите), его состав определяется катализатором.
На сегодня к лучшим можно отнести никелевые и никелево-медные ка-
тализаторы, содержащие 75 – 90 % металла и позволяющие получать из метана
при температуре примерно 500
0
С до 300 г КВУ на 1 г исходного катализатора.
В результате газ трансформируется в ПУМ, содержащий всего до 0,3 % мине-
ральных примесей (меньше, чем в природном графите), его состав определяется
катализатором. Получают КВУ следующим образом. Метан разлагается на по-
верхности катализатора (никеля) на водород и углерод; последний растворяется
в металлических частицах до образования неустойчивого при таких температу-
рах карбида. Этот процесс сопровождается реконструкцией и частичным спе-
канием частиц металла. В результате на их поверхности формируются несколь-
ко кристаллических граней. Одни из них наиболее активны в каталитическом
разложении углерода, а у других структура комплементарна (геометрически
подобна) структуре основной плоскости графита.
84