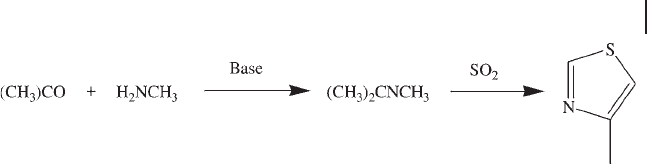
researched by industry, as witnessed by reports in the patent literature. The syn-
thesis of aziridine from N - methylethanolamine is reported in BASF [28] and
Nippon Shokubai patents [29] using cesium and potassium oxides in conjunction
with phosphoric acid supported on silica or glass fabric. Merck have patented a
zeolite - supported cesium catalyst [30] for the production of 4 - methylthiazole
(Scheme 21.1 ).
4 - Methylthiazole is a fungicide and a pharmaceutical intermediate. The catalyst
gives a selectivity of > 60% at a conversion of > 85% but deactivates with time on
stream such that half the activity is lost within two weeks.
The Lucite ALPHA process [31] for the production of methyl methacrylate via
an aldol reaction between methyl propionate and formaldehyde, also uses a sup-
ported cesium oxide catalyst, which requires various additives to minimize catalyst
deactivation. An issue that is rarely discussed in the academic literature, possibly
because of the nature of catalyst testing in academia, is that of deactivation due to
volatilization. Alkali metal oxides may exhibit appreciable volatility under reaction
temperatures > 400 ° C and so there can be a loss of activity over time through
volatilization. To overcome this deactivation mechanism, an AMOCO patent [32]
describes adding an alkali metal compound into the process gas stream so that
the alkali metal compound is deposited on the catalyst during operation to com-
pensate for any loss. It was also noted in the Lucite patent [31] that alkali metal
oxides under some reaction conditions (those where water is in the feedstream)
might enhance the loss in surface area of the silica support. To counteract such
effects the incorporation of modifi ers, such as boron, aluminum, magnesium,
zirconium or hafnium may be added to the catalysts to retard the rate of surface
area decrease. In other studies [33] , cesium oxide was thought to sinter under a
water - containing feed but could re - distribute when the water was removed.
The use of alkali metal oxide catalysts for aldol condensation reactions has been
examined for the production of 2 - ethylhexenal from butanal [34] . When coupled
to a hydrogenation catalyst the system can produce the plasticizer alcohol 2 - ethyl-
hexanol directly. When isobutyraldehyde was used as the feed to a silica - supported
sodium oxide catalyst, no products were formed but a signifi cant amount of carbon
was deposited on the catalyst and in the reactor (Scheme 21.2 ).
These results indicated that an aldehyde with a methyl branch α - to the carbonyl
group passed over a Na
2
O/SiO
2
catalyst was unable to undergo an aldol reaction
but did lay down carbon. This has implications for a combined Pd/Na
2
O/SiO
2
system, as the 2 - ethylhexanal that is formed as an intermediate has an ethyl branch
α - to the carbonyl group and may lead to product poisoning of the base sites of
the catalyst, in a manner similar to that found with isobutyraldehyde over a Na
2
O/
SiO
2
catalyst.
Scheme 21.1
21.2 Catalysts and Catalytic Processes 827