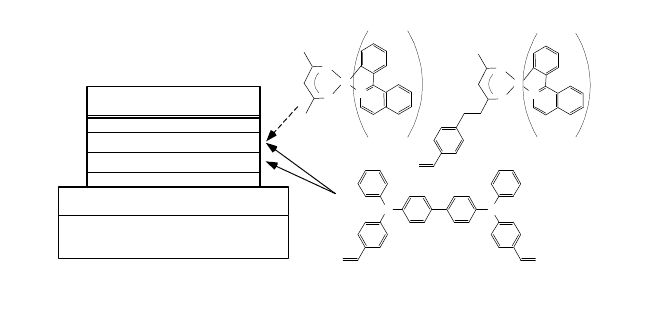
Physical Vapor Deposition of Polymer Thin Films and Its Application 335
Figure 11 shows the luminescence characteristics of the devices whose
HTL were deposition-polymerized at different substrate temperatures.
With increasing substrate temperature from 30 to 50°C, the TPD-Ac film
increased its molecular weight from 4.4 × 10
3
to 1.6 × 10
4
, and polymer
yield from 27 to 71%. Correspondingly, the luminance of the device also
increased with increasing substrate temperature. This result indicates that
the deposition-polymerization is an effective method for constructing
organic devices. Polymerization reaction can be further enhanced by
increasing the substrate temperature, but excessive increase of substrate
temperature resulted in rough film surface.
The vapor deposition-polymerization can make the advantage of its
solventless feature in constructing multilayered structures of polymer
thin films, which is effective in developing OLED due to the possibility
of optimizing carrier balance and recombination at the heterojunctions.
Figure 12 shows an example of OLED structure prepared by deposition
polymerization of HTL and EML susscessively.
22
A divinyl derivative
of tetraphenyldiaminobiphenyl DvTPD was deposited to form a HTL on
an ITO substrate coated with poly(3,4-ethylene dioxythiophene)-poly
(styrene sulfonate) (PEDOT:PSS), on which an EML was deposited by
coevaporation of DvTPD and a vinyl derivative of phosphorescent
dopant Ir(piq)
2
acac-vb. After depositing the HTL and the EML, the
substrate was annealed in the vacuum chamber at 100°C for 1 h to
thermally polymerize these layers. The device was finished by depositing
an electron transport layer (ETL) of bathocuproin (BCP), an electron
injection layer of lithium fluoride, and then an aluminum cathode. The
LiF (0.5 nm)/Al (100 nm)
BCP (45 nm)
DvTPD:dopant (40 nm)
DvTPD (30 nm)
PEDOT/PSS (40 nm)
ITO
glass substrate
N N
N
Ir
2
O
O
Ir(piq)
2
acac-vb
N
Ir
2
O
O
Ir(piq)
2
acac
Fig. 12. OLED structure and monomer materials for vapor deposition polymerization.