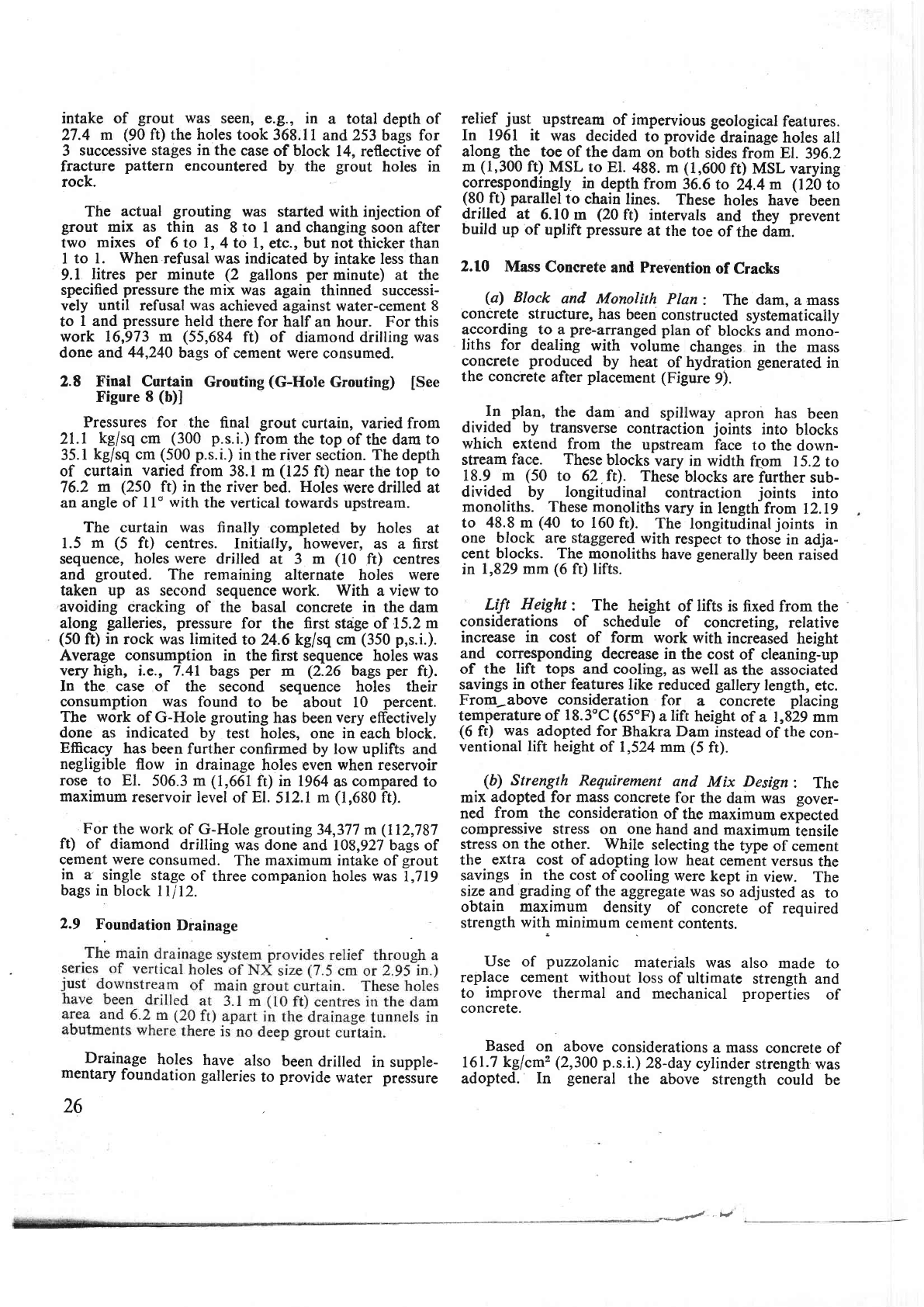
intake of
grout
was
seen, €.9., in
a total
depth
of
27.4
m
(90
ft) the
holes
took 368.11
and
253 bags for
3
successive stages
in the
case
of
block
14, reflective of
fracture
pattern
encountered
by
the
grout
holes
in
rock.
The
actual
grouting
was
started
with injection of
grout
mix as thin as
8
to
I
and changing soon
after
two
mixes
of
6 to l,
4 to l,
etc.,
but not
thicker
than
I
to l.
When
refusal was
indicated
by intake less than
9.1
litres
per
minute
(2
gallons per
minute)
at
the
specified
pressure
the
mix was
again
thinned successi-
vely until refusal
was
achieved
against water-cement 8
to
I
and
pressure
held
there
for
half
an hour.
For this
work
16,973 m
(55,684
f0 of diamond drilling was
done
and
44,240
bags
of cement
were
consumed.
2.8 Final Curtain
Grouting
(G-HoIe
Grouting)
[See
Figure
I
(b)l
Pressures
for
the
final
grout
curtain, varied
from
2l.l
kg/sq
cm
(300
p.s.i.)
from the top
of the dam
to
35.1
kg/sq
cm
(500
p.s.i.)
in
the
river
section. The depth
of curtain
varied
from
38.1
m
(125
f0
near
the
top
to
76.2
m
(250
ft)
in
the river
bed.
Holes
were drilled at
an
angle
of l1o
with
the vertical towards upstream.
The
curtain
was
finally
completed
by holes at
1.5
m
(5
ft) centres.
Initially, however,
as a first
sequence,
holes
were
drilled at
3
m
(10
ft)
centres
and
grouted.
The remaining
alternate holes
were
taken up as
second sequence
work.
With
a
view
to
avoiding
cracking of the
basal
concrete in
the dam
along
galleries,
pressure
for
the
first stage of 15.2
m
(50
f0
in
rock
was
limited
to 24.6 kelsq
cm
(350
p,s.i.).
Average
consumption
in
the
first
sequence holes
was
very
high, i.e., 7.41
bags
per
m
(2.26
bags
per
ft).
In
the
case of
the second
sequence
holes their
consumption was
found
to
be about 10
percent.
The work
of
G-Hole
grouting
has beenvery
effectively
done
as
indicated
by
test holes, one in
each
block.
Efficacy
has
been
further confirmed by low uplifts
and
negligible
flow
in
drainage
holes even
when reservoir
rose
to El.
506.3
m (1,661
ft) in
1964
as
compared
to
maximum
reservoir
level
of EI.
512.1
m
(1,680
ft).
For
the
work
of
G-Hole
grouting
34,377
m
(112,787
f0 of
diamond
drilling
was done
and
108,927
bags
of
cement were
consumed.
The
maximum
intake
of
grout
in
a
single stage
of
three companion holes was
1,719
bags in
block
ll
l12.
2.9
Foundation
Drainage
Drainage
holes
have
also
been
drilled
in
supple-
mentary
foundation
galleries
to
provide
water
pressure
26
relief
just
upstream
of
impervious
geological
features.
In
196I it
was
decided
to
provide
drainage holes all
along
the
toe
of
the dam
on
both
sides
from El.
396.2
m
(1,300
ft)
MSL
to
El.
488. m
(1,600
ft)
MSL varying
ggJrglpondingly in
depth
from
36.6
to
24.4
m
(120
ro
(80
ft)
parallel
to
chain
lines.
These
holes
have
been
drilled at
6.10
m
(20
ft) intervals
and
they
prevent
build up
of uplift
pressure
at
the
toe
of
the
dim.
z.LA
Mass
Concrete
and
Prevention
of Cracks
(a)
Block
and
Monolith
Plan:
The
dam,
a
mass
concrete structure,
has
been
constructed
systematicaily
according to a
pre-arranged
plan
of
blocks and mono-
Iiths
for
dealing
with
volume
changes
in
the
mass
concrete
produced
by
heat
of
hydration
generated
in
the concrete
afrer
placement
(Figure
9).
In
plan,
the
dam
and
spillway
apron
has
been
divided by transverse
contraction
joints
into
blocks
which
extend from
the
upstream
face
to the
down-
stream
face. These
blocks
vary
in
width
flom 15.2
to
18.9
m
(50
to
62.ft).
These
blocks
are
further
sub-
divided by longitudinal
contraction
joints
into
monoliths. These monoliths
vary
in
lengttr_from
lZ.l9
to
48.8 m
(40
to 160
ft).
The
longitudinal
joints
in
one
block
are
staggered
with
respecr
to those in adja-
cent
blocks. The
monoliths
have
generally
been
raised
in
1,829 mm
(6
ft) lifts.
Lift
Height:
The
height
of
lifts
is fixed
from
rhe
considerations of schedule
of
concreting,
relative
increase
in
cost of form
work
with
increaied
height
and coresponding decrease
in
the cost
of cleaning-up
of the
lift tops
and
cooling,
as
well
as
the
associated
savings
in other features
like
reduced
gallery
length,
etc.
From,
above consideration
for
a concrete
placing
temperature
of
18.3'C
(65"f'1a
lifr
height
of a 1,829
mm
(6
ft)
was
adopted for
Bhakra
Dam
instead
of
the
con-
ventional
lift
height
of 1,524
mm
(5
ft).
(b)
Strength
Requirement
and
Mix
Design:
The
mix
a4opted
for
mass
concrete
for
the
dam was
gover-
ned
from the consideration
of
the maximum
expected
compressive stress on
one
hand
and maximum
tensile
stress
on
the other.
While
selecting
the
type
of cement
the
extra cost
of
adopting low
heat
cement
versus
the
savings
in
the cost of
cooling were
kept
in
view.
The
size
and
grading
of
the
aggregate was
so
adjusted
as to
obtain
maximum
density
of
concrete
of
required
strength
with minimum
cenrent
contents.
Use
of
puzzolanic
materials
was
also
made
to
replace cement without
loss
of
ultimate
strength and
to
improve
thermal and
mechanical
properties
of
concrete.
Based
on
above
considerations
a mass
concrete
of
161.7
kg/cms
(2,300
p.s.i.)
28-day
cylinder
strength'was
adopted.'
In
general
the above
strength
could be
-*4'/
'*