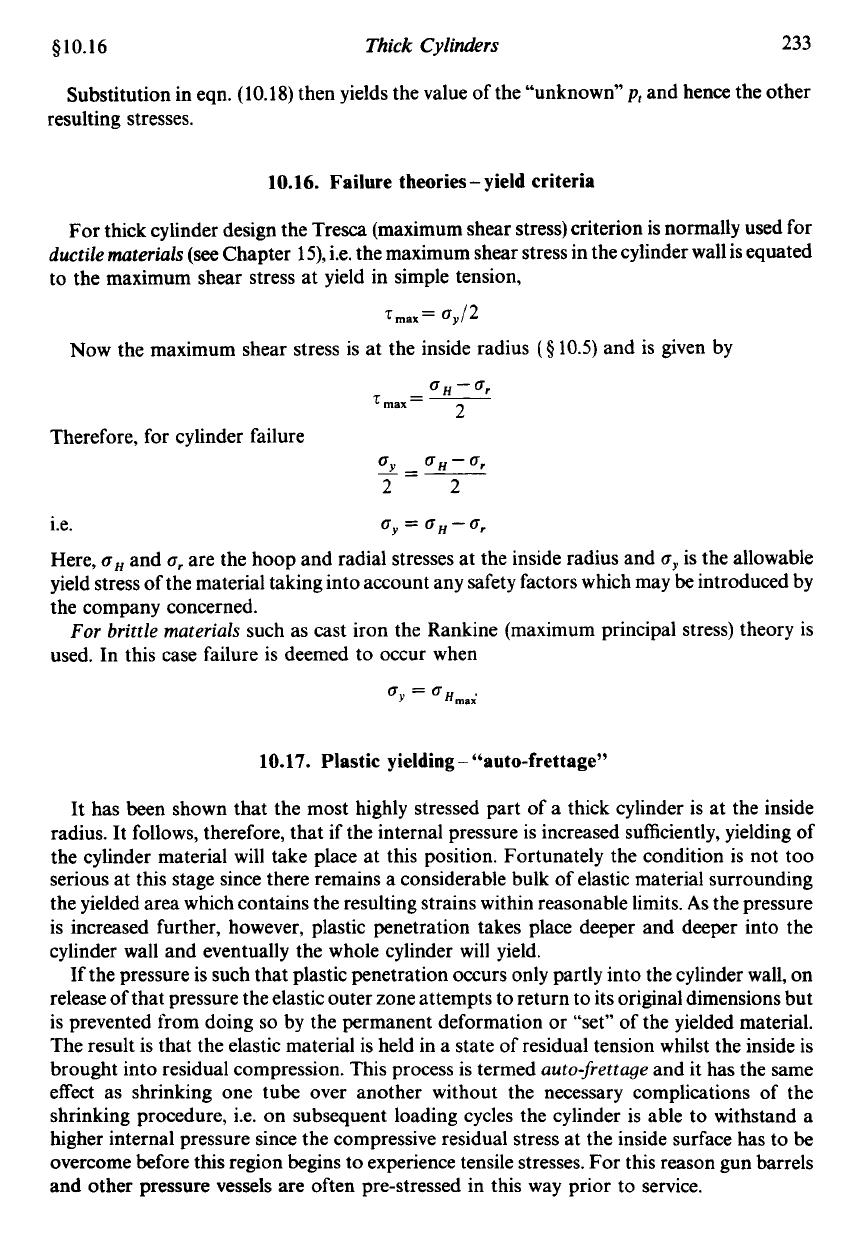
$10.16 Thick
Cylinders
233
Substitution in eqn.
(10.18)
then yields the value of the “unknown”
pt
and hence the other
resulting stresses.
10.16.
Failure theories- yield criteria
For thick cylinder design the Tresca (maximum shear stress) criterion is normally used for
ductile materials
(see
Chapter
15),
i.e. the maximum shear stress in the cylinder wall is equated
to the maximum shear stress at yield in simple tension,
Zma)r=
ay/2
Now the maximum shear stress is at the inside radius
(9
10.5)
and is given by
dH-ar
Tmax=
~
2
Therefore, for cylinder failure
i.e.
by
=
dH
-or
Here,
a”
and
or
are the hoop and radial stresses at the inside radius and
cy
is the allowable
yield stress of the material taking into account any safety factors which may
be
introduced by
the company concerned.
For brittle materials
such as cast iron the Rankine (maximum principal stress) theory is
used. In this case failure is deemed to occur when
10.17.
Plastic yielding- “auto-frettage”
It has been shown that the most highly stressed part of a thick cylinder is at the inside
radius. It follows, therefore, that if the internal pressure is increased sufficiently, yielding of
the cylinder material will take place at this position. Fortunately the condition is not too
serious at this stage since there remains a considerable bulk of elastic material surrounding
the yielded area which contains the resulting strains within reasonable limits.
As
the pressure
is increased further, however, plastic penetration takes place deeper and deeper into the
cylinder wall and eventually the whole cylinder will yield.
If the pressure is such that plastic penetration occurs only partly into the cylinder wall, on
release of that pressure the elastic outer zone attempts to return to its original dimensions but
is prevented from doing
so
by the permanent deformation or “set” of the yielded material.
The result is that the elastic material is held in a state of residual tension whilst the inside is
brought into residual compression. This process is termed
auto-frettage
and it has the same
effect as shrinking one tube over another without the necessary complications of the
shrinking procedure, i.e. on subsequent loading cycles the cylinder is able to withstand a
higher internal pressure since the compressive residual stress at the inside surface has to
be
overcome before this region begins to experience tensile stresses.
For
this reason gun barrels
and other pressure vessels are often pre-stressed in this way prior to service.