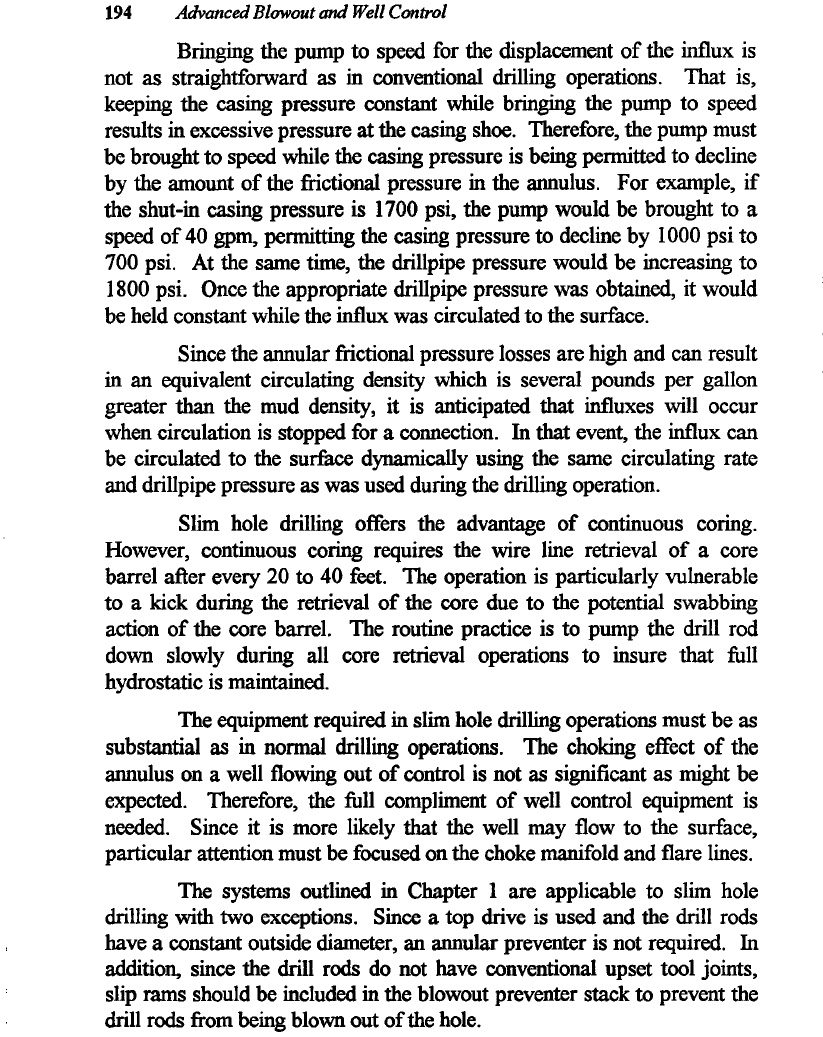
194
Advanced
Blowout
and
Well
Control
Bringing the pump
to
speed for the displacement of the influx is
not
as
straightforward
as
in conventional drilling operations.
That
is,
keeping the casing pressure constant while bringing the pump to speed
results in excessive pressure
at
the casing shoe. Therefore, the pump must
be brought to speed while the casing pressure is being
permitted
to decline
by the amount
of
the frictional pressure in the annulus. For example, if
the shut-in casing pressure is
1700
psi, the pump would be brought to a
speed
of
40
gpm, permitting the casing pressure
to
decline by
1000
psi to
700
psi. At the same time, the drillpipe pressure would be increasing to
1800 psi. Once the appropriate drillpipe pressure
was
obtained, it would
be held constant while the
influx
was circulated to the surf-ace.
Since the annular frictional pressure losses are high and can result
in
an equivalent circulating density which is several pounds per gallon
greater
than
the mud density, it is anticipated
that
influxes will occur
when circulation is stopped for
a
connection.
In
that
event, the influx can
be circulated to the surface dynamically using the same circulating rate
and drillpipe pressure
as
was used during the drilling operation.
Slim hole drilling offers the advantage of continuous coring.
However, continuous
coring
requires the wire line retrieval of a core
barrel after every
20
to
40
feet. The operation is particularly vulnerable
to a
kick
during
the retrieval
of
the core due to the potential swabbing
action
of
the core barrel. The routine practice is to pump the drill rod
down slowly during all core retrieval operations
to
insure
that
fill
hydrostatic
is
maintained.
The equipment required in slim hole drilling operations must be
as
substantial
as
in
normal
drilling
operations. The choking effect
of
the
annulus
on
a well flowing out of control
is
not
as
significant as might be
expected. Therefore, the full compliment of well control equipment is
needed. Since it is more likely
that
the
well may flow to the surface,
particular attention must be focused on the choke manifold and flare lines.
The systems outlined in Chapter
1
are applicable to slim hole
drilling with
two
exceptions. Since
a
top drive is used and the drill rods
have
a
constant outside diameter, an annular preventer is not required.
In
addition, since the drill
rods
do not have conventional upset tool joints,
slip
rams
should be included
in
the blowout preventer
stack
to
prevent the
drill rods
from
being blown out of the hole.