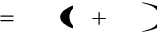
особенностью является способность наращивать значительные объемы
металлов на базовую деталь или на ее основу и по диапазону этих объемов
и скорости наращивания они примыкают и к технологиям макроуровня, и к
технологиям микроуровня. При всей условности деления технологий на
макро-, микро- и наноуровни, методы наплавки можно отнести к
переходным уровням.
Доля основного металла в наплавленном слое g
0
, обычно
выражаемая в процентах, колеблется в широких пределах и зависит от
способа и режима наплавки:
,
где F
о
– площадь сечения слоя расплавленного основного металла,
F
н
– площадь сечения наплавленного металла.
Как правило, при наплавке долю основного металла в
наплавленном слое стремятся свести к минимуму. Ее можно
регулировать, изменяя соотношение скоростей плавления электродного и
основного металлов. Величина g
0
уменьшается при увеличении скорости
наплавки, при применении для наплавки электродных лент или при
колебательных движениях электрода.
Важной характеристикой процесса является производительность
наплавки П
н
, которую измеряют массой металла или площадью
поверхности, наплавляемых в единицу времени (кг/ч, м
2
/ч). Кроме
производительности, способы наплавки может характеризовать
толщина наплавленного слоя d
в
, наносимого за один проход.
4.2 Классификация способов наплавки
Способы наплавки классифицируют по физическим, техническим и
технологическим признакам. Наиболее распространенной и удобной является
классификация по физическому признаку – по используемым источникам
нагрева. По этому признаку основные способы наплавки и наварки можно
разделить на три группы (рис. 4.1):
-термические (электродуговая, электрошлаковая, плазменная);
-электроннолучевая, лазерная (световая), индукционная, газовая, печная;
-термомеханические (электроконтактная, прокаткой, экструдированием);
-механические (взрывом, трением).