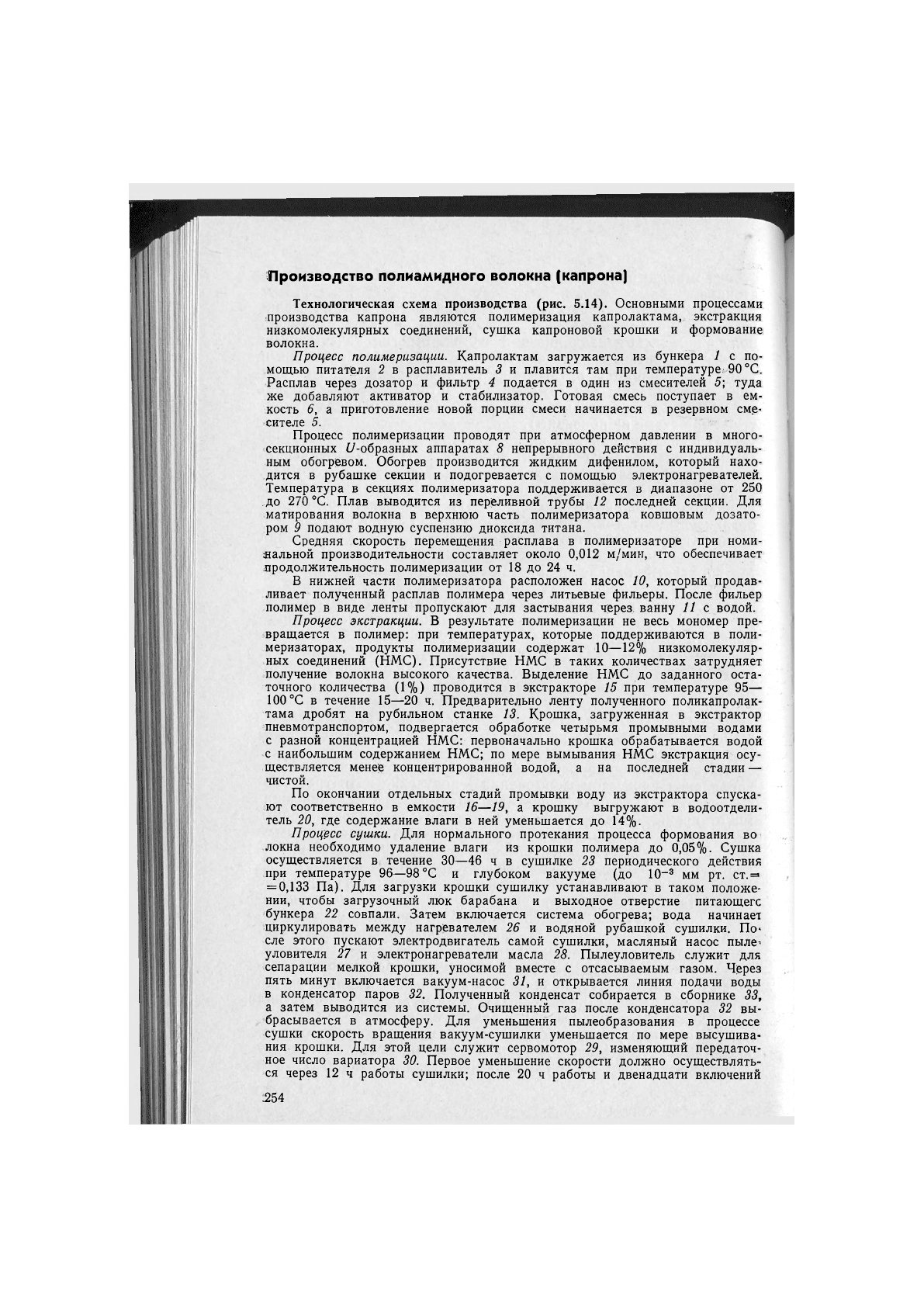
Производство полиамидного волокна (капрона)
Технологическая схема производства (рис. 5.14). Основными процессами
производства капрона являются полимеризация капролактама, экстракция
низкомолекулярных соединений, сушка капроновой крошки и формование
волокна.
Процесс полимеризации. Капролактам загружается из бункера 1 с по-
мощью питателя 2 в расплавитель 3 и плавится там при температуре 90 °С.
Расплав через дозатор и фильтр 4 подается в один из смесителей 5; туда
же добавляют активатор и стабилизатор. Готовая смесь поступает в ем-
кость 6, а приготовление новой порции смеси начинается в резервном сме-
сителе 5.
Процесс полимеризации проводят при атмосферном давлении в много-
секционных £/-образных аппаратах 8 непрерывного действия с индивидуаль-
ным обогревом. Обогрев производится жидким дифенилом, который нахо-
дится в рубашке секции и подогревается с помощью электронагревателей.
Температура в секциях полимеризатора поддерживается в диапазоне от 250
,до 270 °С. Плав выводится из переливной трубы 12 последней секции. Для
матирования волокна в верхнюю часть полимеризатора ковшовым дозато-
ром 9 подают водную суспензию диоксида титана.
Средняя скорость перемещения расплава в полимеризаторе при номи-
нальной производительности составляет около 0,012 м/мин, что обеспечивает
лродолжительность полимеризации от 18 до 24 ч.
В нижней части полимеризатора расположен насос 10, который продав-
ливает полученный расплав полимера через литьевые фильеры. После фильер
полимер в виде ленты пропускают для застывания через ванну 11 с водой.
Процесс экстракции. В результате полимеризации не весь мономер пре-
вращается в полимер: при температурах, которые поддерживаются в поли-
меризаторах, продукты полимеризации содержат 10—12% низкомолекуляр-
ных соединений (НМС). Присутствие НМС в таких количествах затрудняет
получение волокна высокого качества. Выделение НМС до заданного оста-
точного количества (1%) проводится в экстракторе 15 при температуре 95—
100 °С в течение 15—20 ч. Предварительно ленту полученного поликапролак-
тама дробят на рубильном станке 13. Крошка, загруженная в экстрактор
пневмотранспортом, подвергается обработке четырьмя промывными водами
с разной концентрацией НМС: первоначально крошка обрабатывается водой
с наибольшим содержанием НМС; по мере вымывания НМС экстракция осу-
ществляется менее концентрированной водой, а на последней стадии —
чистой.
По окончании отдельных стадий промывки воду из экстрактора спуска-
ют соответственно в емкости 16—19, а крошку выгружают в водоотдели-
тель 20, где содержание влаги в ней уменьшается до 14%.
Процесс сушки. Для нормального протекания процесса формования во
локна необходимо удаление влаги из крошки полимера до 0,05%. Сушка
осуществляется в течение 30—46 ч в сушилке 23 периодического действия
при температуре 96—98 °С и глубоком вакууме (до Ю
-3
мм рт. ст.=
= 0,133 Па). Для загрузки крошки сушилку устанавливают в таком положе-
нии, чтобы загрузочный люк барабана и выходное отверстие питающего
бункера 22 совпали. Затем включается система обогрева; вода начинает
циркулировать между нагревателем 26 и водяной рубашкой сушилки. По-
сле этого пускают электродвигатель самой сушилки, масляный насос пыле^
уловителя 27 и электронагреватели масла 28. Пылеуловитель служит для
сепарации мелкой крошки, уносимой вместе с отсасываемым газом. Через
пять минут включается вакуум-насос 31, и открывается линия подачи воды
в конденсатор паров 32. Полученный конденсат собирается в сборнике 33,
а затем выводится из системы. Очищенный газ после конденсатора 32 вы-
брасывается в атмосферу. Для уменьшения пылеобразования в процессе
сушки скорость вращения вакуум-сушилки уменьшается по мере высушива-
ния крошки. Для этой цели служит сервомотор 29, изменяющий передаточ-
ное число вариатора 30. Первое уменьшение скорости должно осуществлять-
ся через 12 ч работы сушилки; после 20 ч работы и двенадцати включений
-254