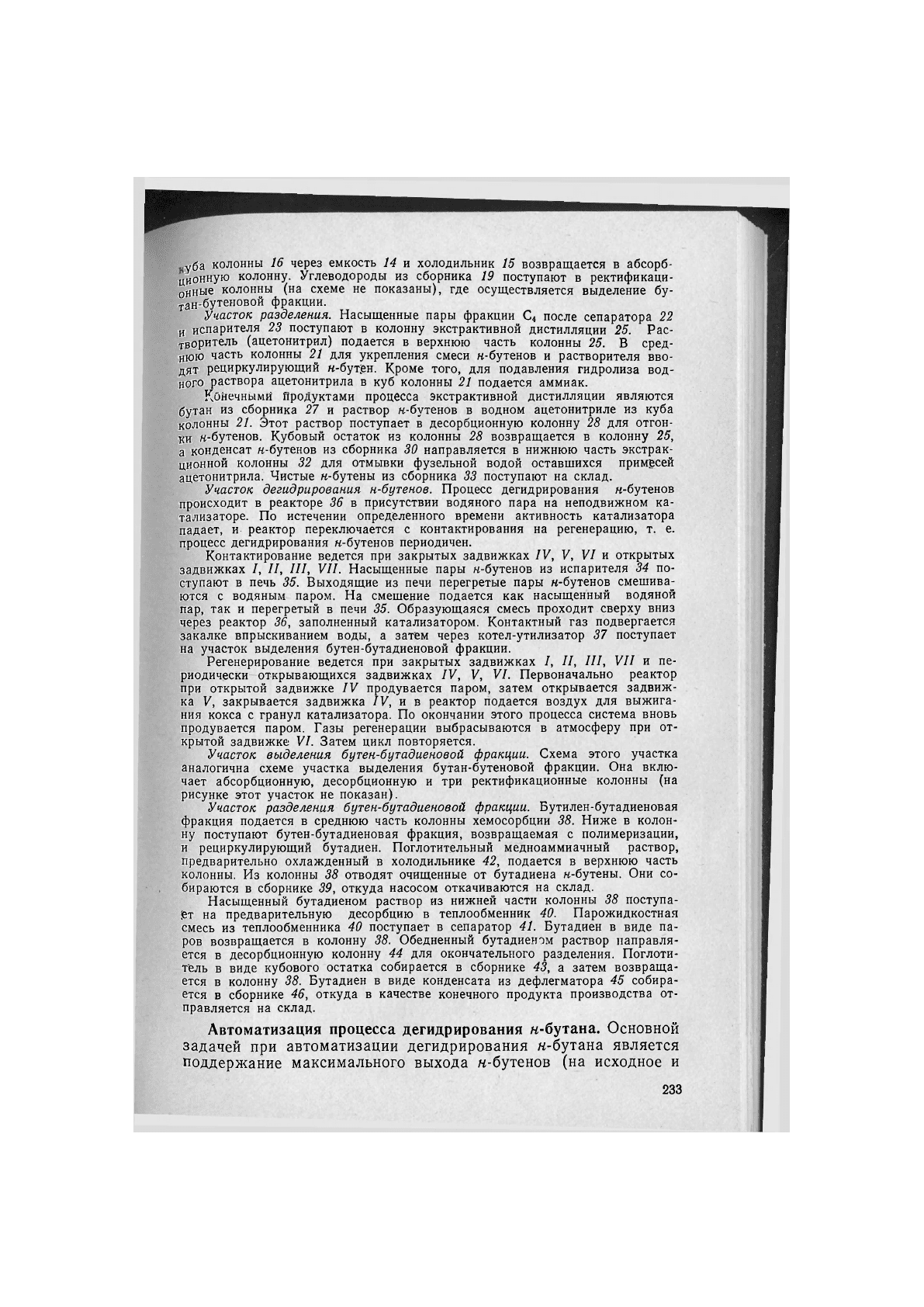
уба колонны 16 через емкость 14 и холодильник 15 возвращается в абсорб-
ционную колонну. Углеводороды из сборника 19 поступают в ректификаци-
онные колонны (на схеме не показаны), где осуществляется выделение бу-
тан-бутеновой фракции.
Участок разделения. Насыщенные пары фракции С
4
после сепаратора 22
й
испарителя 23 поступают в колонну экстрактивной дистилляции 25. Рас-
творитель (ацетонитрил) подается в верхнюю часть колонны 25. В сред-
нюю часть колонны 21 для укрепления смеси «-бутенов и растворителя вво-
дят рециркулирующий к-бут;ен. Кроме того, для подавления гидролиза вод-
ного раствора ацетонитрила в куб колонны 21 подается аммиак.
Конечными Яродуктами процесса экстрактивной дистилляции являются
бутан из сборника 27 и раствор н-бутенов в водном ацетонитриле из куба
колонны 21. Этот раствор поступает в десорбционную колонну 28 для отгон-
ки к-бутенов. Кубовый остаток из колонны 28 возвращается в колонну 25,
а конденсат н-бутенов из сборника 30 направляется в нижнюю часть экстрак-
ционной колонны 32 для отмывки фузельной водой оставшихся примесей
ацетонитрила. Чистые н-бутены из сборника 33 поступают на склад.
Участок дегидрирования н-бутенов. Процесс дегидрирования к-бутенов
происходит в реакторе 36 в присутствии водяного пара на неподвижном ка-
тализаторе. По истечении определенного времени активность катализатора
падает, и реактор переключается с контактирования на регенерацию, т. е.
процесс дегидрирования н-бутенов периодичен.
Контактирование ведется при закрытых задвижках IV, V, VI и открытых
задвижках I, II, III, VII. Насыщенные пары н-бутенов из испарителя 34 по-
ступают в печь 35. Выходящие из печи перегретые пары «-бутенов смешива-
ются с водяным паром. На смешение подается как насыщенный водяной
пар, так и перегретый в печи 35. Образующаяся смесь проходит сверху вниз
через реактор 36, заполненный катализатором. Контактный газ подвергается
закалке впрыскиванием воды, а затем через котел-утилизатор 37 поступает
на участок выделения бутен-бутадиеновой фракции.
Регенерирование ведется при закрытых задвижках I, II, III, VII и пе-
риодически открывающихся задвижках IV, V, VI. Первоначально реактор
при открытой задвижке IV продувается паром, затем открывается задвиж-
ка V, закрывается задвижка IV, и в реактор подается воздух для выжига-
ния кокса с гранул катализатора. По окончании этого процесса система вновь
продувается паром. Газы регенерации выбрасываются в атмосферу при от-
крытой задвижке VI. Затем цикл повторяется.
Участок выделения бутен-бутадиеновой фракции. Схема этого участка
аналогична схеме участка выделения бутан-бутеновой фракции. Она вклю-
чает абсорбционную, десорбционную и три ректификационные колонны (на
рисунке этот участок не показан).
Участок разделения бутен-бутадиеновой фракции. Бутилен-бутадиеновая
фракция подается в среднюю часть колонны хемосорбции 38. Ниже в колон-
ну поступают бутен-бутадиеновая фракция, возвращаемая с полимеризации,
и рециркулирующий бутадиен. Поглотительный медноаммиачный раствор,
предварительно охлажденный в холодильнике 42, подается в верхнюю часть
колонны. Из колонны 38 отводят очищенные от бутадиена н-бутены. Они со-
бираются в сборнике 39, откуда насосом откачиваются на склад.
Насыщенный бутадиеном раствор из нижней части колонны 38 поступа-
ет на предварительную десорбцию в теплообменник 40. Парожидкостная
смесь из теплообменника 40 поступает в сепаратор 41. Бутадиен в виде па-
ров возвращается в колонну 38. Обедненный бутадиеном раствор направля-
ется в десорбционную колонну 44 для окончательного разделения. Поглоти-
тель в виде кубового остатка собирается в сборнике 43, а затем возвраща-
ется в колонну 38. Бутадиен в виде конденсата из дефлегматора 45 собира-
ется в сборнике 46, откуда в качестве конечного продукта производства от-
правляется на склад.
Автоматизация процесса дегидрирования «-бутана. Основной
задачей при автоматизации дегидрирования я-бутана является
поддержание максимального выхода «-бутенов (на исходное и
.233