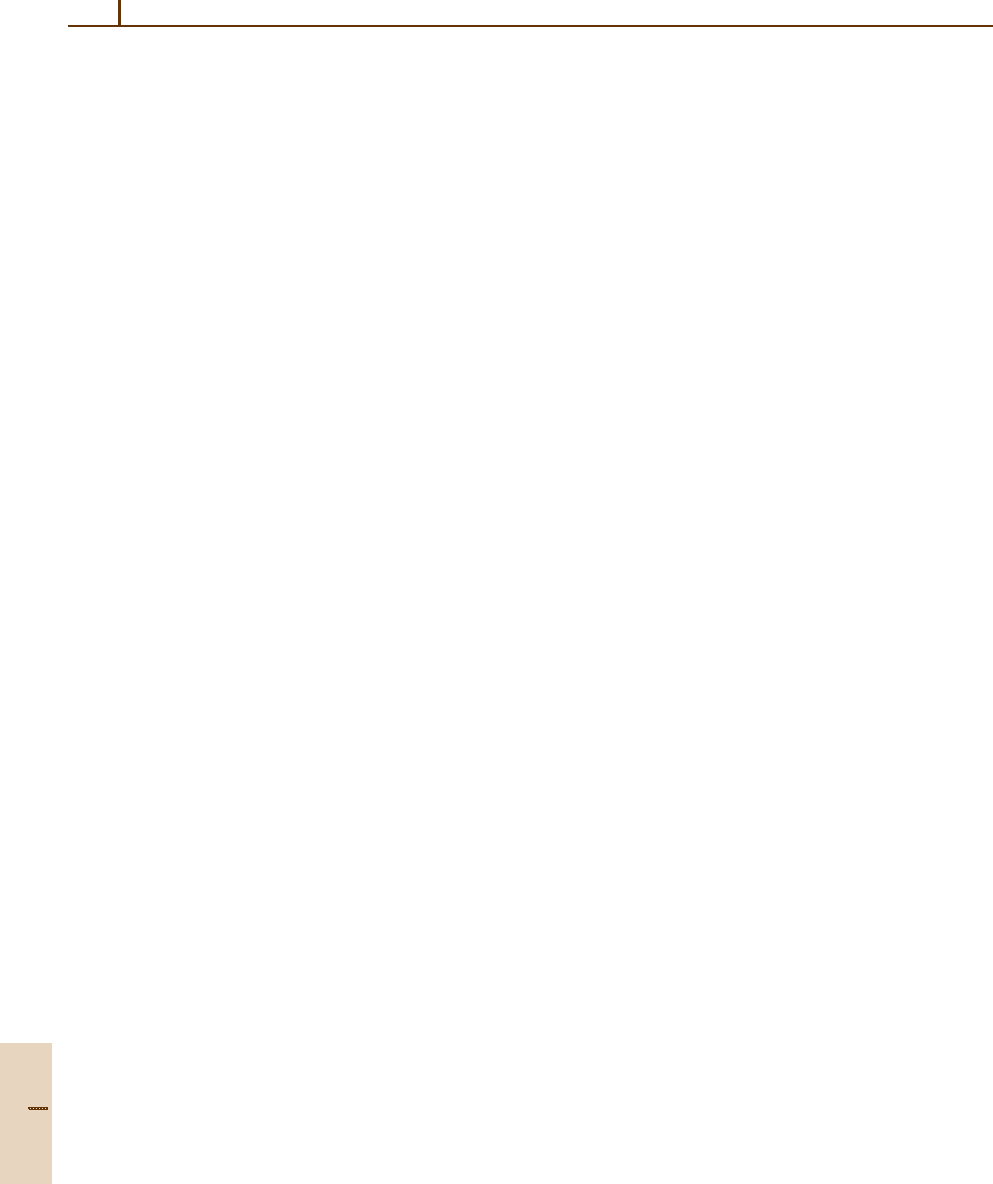
612 Part C Molecules
40.6 The Scanning Michelson Interferometer
Optical throughput is not only determined by the area of
the field of view stop, but also the solid angle subtended
by the rays traversing this area. The solid angle Ω of
rays traversing a Jacquinot stop positioned in the focal
plane of an input collimator is given by the ratio of the
interferometer beam area divided by the square of the
focal length of the collimator.
For a given collimator focal length, the area of the
Jacquinot stop is inversely proportional to the resolving
power. To maintain equal throughput, the area of the
interferometer optics should be increased as resolving
power is increased in order to offset the decrease in the
Jacquinot stop area.
It is common to construct interferometers with
2.5 cm diameter optics for resolving powers up to 5000,
5.0 cm diameter optics for resolving powers up to 40 000
and 7.5 cm diameter optics for resolving powers up to
1 000 000.
In order to obtain a uniform state of interference
across the entire beam of the interferometer, the beam-
splitter substrate and the two mirrors must be flat to
within a small fraction of the wavelength used. Also,
these elements must be oriented correctly so that the op-
tical path difference error across the beam is less than
a small fraction of the wavelength.
Figure 40.1 shows two substrates at the beam-
splitter position. One of the substrates supports the
beamsplitting coating, while the companion substrate
of precisely the same thickness acts as a compensat-
ing element to insure identical optical paths through
the two arms of the interferometer. To avoid sec-
ondary interference effects, both beamsplitter and
compensator substrates are normally wedged. The di-
rection of the wedges of the two substrates must be
aligned again to insure symmetry in both arms of the
interferometer.
The maintenance of a very close orientational align-
ment tolerance of the two mirrors with respect to the
beamsplitter in a stable manner over time and while
scanning one of the mirrors is the greatest challenge of
interferometer design and is also the greatest weakness
of FTIR.
In early models of FTIRs, alignment was maintained
by means of a stable mechanical structure and a highly
precise linear air bearing for the scanning mirror. Sat-
isfactory operation required a stable environment and
frequent alignment tuning and could be achieved for
mirror displacements of only several centimeters, thus
limiting the maximum resolution.
Different techniques have been developed to over-
come this weakness in FTIR. The two most prominent
are (1) Dynamic alignment of the interferometer, where
optical alignment is servo-controlled using the refer-
ence laser not only for mirror displacement control
but also for mirror orientation control, and (2) the
use of cube corner mirrors in place of the flat mir-
rors in the interferometer. Dynamic alignment has the
advantage of retaining a high degree of simplicity in
the optical design of the interferometer. On the other
hand it is more complex electronically. Cube corners
have the property of always reflecting light 180
◦
to in-
cident light independent of orientation. Cube corners
always insure wavefront parallelism at the point of re-
combination of the two beams in the interferometer.
Cube corners lack a defined optical axis. In a cube
corner interferometer, the optical axis is defined as
the direction in which the wavefronts undergo zero
shear.
The scanning Michelson Interferometer is normally
provided with a drive mechanism to displace one of the
mirrors precisely parallel to its initial position and at
uniform velocity. The uniform velocity translates the
mirror displacement dependent intensities into time de-
pendent intensities. This facilitates signal processing
electronics. In some measurement scenarios however,
where the sample spectrum may vary with time, it
is undesirable to deal with the multifrequency time-
varying intensities of the interferogram signal. In this
case it is preferable to scan the moving mirror in
a stepwise mode, where the mirror is momentarily sta-
tionary at the time of signal measurement and then
advanced rapidly to the next position. The mirror scan
velocity v can be varied so that electrical signals can
have different frequencies for the same optical frequen-
cies:
f = σ/2v.
(40.17)
The scan velocity is normally selected to provide the
most favorable frequency regime for the detector and
electronics used and for the mechanical capabilities
of the mirror drive. Typically the velocity range is
from 0.05 cm/sto4cm/s, putting the frequencies in
the audio range. At these velocities, the measurement
scan may be completed in a shorter time than is de-
sired for signal averaging purposes. In this case it is
common to repeat the scan a number of times and
add the results together: this is called co-adding of
scans.
Part C 40.6