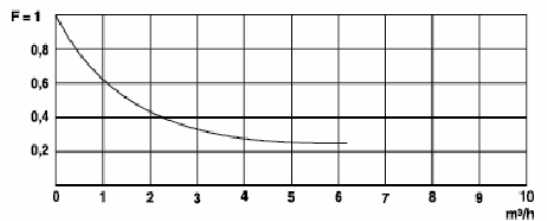
42
made of aluminum weights about 610g which when added with the heat sink the whole
enclosure weights 3.5kg.
2.7.1.2. Interior heat sink
When mounting the heat sink inside the chassis the air circulation would be very limited
if not increased via an external source, the ambient temperature in the chassis along with
the junction temperature would probably rise to a critical level and the system would
eventually shut-down or burn. However even with a small fan airflow can be produced
through the interior raising the performance of the heat sink, often many times over as
illustrated in the figure below.
Figure 30: Thermal resistance factor vs. airflow
Where F is a factor of which the thermal resistance of a heat sink is reduced depending on
the airflow across the heat sink. The curve resulting in a horizontal line is mostly due to
the fact that airflow does not increase the radiated heat.
This would allow a reduction in weight due to removal of excess heat sink at the cost of a
few watts of lost effect for the fan and the possibility of fan-breakdown, causing a fatal
temperature build-up. The fan would at best push in air at the temperature up to 70°C and
the slightly warmer air coming out would blend with the ambient air and if the
compartment is not too small it would not raise the environment temperature
significantly. The increased internal temperature has to be included in the calculations
where size of the heat sink is determined. This solution would also suffer in cooling
capacity due to a decreasing air density but it can at least be reduced by serial-coupling
many fans which can create a strong pressure in the chassis by having a smaller outlet.
However it would not be nearly enough to compensate for the loss in pressure at higher
altitudes since even if the convection could be doubled or tripled it initially represents
such a small share of the total the reduction in thermal resistivity would be insignificant.
Most aircrafts and particularly JAS 39 GRIPEN have equipment for providing
pressurized air at a few degrees above 0°C and this can strongly reduce the need for a
large heat sink at the cost of a less stand-alone device. Since the air can contain moist and
particles the air cannot be sprayed directly on a heat sink or the component but is meant
to be ran through a cooling block similar to the one of conventional fluid cooling;
although not nearly as effective due to the difference in specific heat capacity. Here a
failure in the cooling system would inevitable lead to a failure in the inverter as well as
all other equipment depending on the same cooling system. It has to be considered here