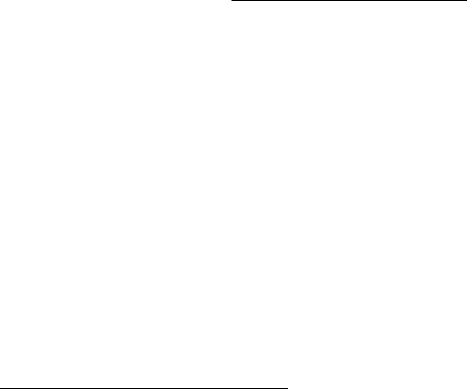
130 A. Pramanik et al.
near the particle occurs due to higher obstruction to plastic deformation; this
causes easier particle fracture. In addition, the coarse particles themselves may
have more defects, which will result in higher tool wear and worse surface finish
during machining of MMCs. A large quantity of harmful dust after machining
MMCs with larger particle sizes has been reported, although this disappears when
machining MMCs with a smaller particle size.
The effect of particles on processes parameters during machining of MMCs can
be explained explicitly by comparing machining outcomes and those of the corre-
sponding matrix material. These are described in the following sections.
5.2.1 Strength of MMC During Machining
The chip formation forces during turning depend on the strength of the material,
cutting conditions and tool geometry. Speed and feed influence the strength of the
workpiece material in the deformation zones through temperature, strain and strain
rate [29,
30]. The strength of the non-reinforced aluminium alloy is nearly insensi-
tive to strain rate at low strain and strain rate [31–33]. However, at higher strains
(more than 1) and strain rates (10
3
s
–1
or higher), i.e., as experienced during turn-
ing, the strength is considerably dependent on strain rate, increasing with increas-
ing strain rate [34–39]. In the following work, due to a lack of data, the effects of
strain, strain rate and temperature on shear strength are not considered explicitly.
However, it was found that the measured chip formation forces in the cutting and
thrust directions (F
cc
1
and
F
tc
, respectively), and shear angle (
φ
) depend on the
cutting conditions. Hence, the experimental shear strength values, τ
s
, for both the
MMC and corresponding aluminium alloy at different machining conditions were
determined using Equation (5.1) following the procedure described in [29,
34].
φφ
τ
−
=
cc tc
s
c
[(F cos ) (F sin )] sin
A
(5.1)
The shear strength values of MMC and non-reinforced alloy for different ma-
chining conditions are presented in Figure 5.1. It can be seen that the strength of
MMC is significantly lower than that of non-reinforced alloy for all the machining
conditions considered. At low feeds, the strength of MMC and non-reinforced
alloy decreases with increasing feed (Figure 5.1(a)). However, at higher feeds, τ
s
does not vary with feed significantly. Similarly speed does not influence the
strength of the MMC (Figure 5.1(b)). At lower speed ranges, the strength of non-
reinforced alloy increases with increasing speed, but after a certain speed it de-
creases with further speed increases.
At low feed (cut thickness), the cut area is small and the entire cut area may
have been work-hardened by previous tool passage. This will result in a higher
τ
s
value at lower feeds than at higher feeds. Increased percentage of particle
fracture/debonding forces (as will be seen in Figure 5.25) indicates higher tool–
particle interactions at low feed for MMCs, which may be another reason for in-
1
Chip formation forces were calculated by subtracting the ploughing and particle frac-
ture/debonding forces from total machining forces.