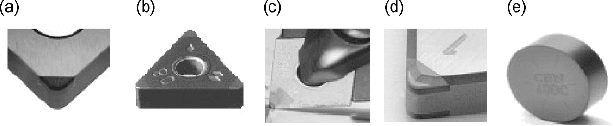
Machining of Hard Materials 103
The ceramic types suitable for machining hard materials are the aluminium-
oxide based, mixed and reinforced (whiskered) grades, and the silicon-nitride-
based grades. They have excellent characteristics including high wear resistance,
high hot hardness and good chemical stability. The mixed-type grade ceramic with
TiC content and micrograined structure is used most widely in continuous or
slightly interrupted hard machining of steels and cast iron. Normally, ceramics is
not recommended when tolerances are tighter than ±0.025 mm (±0.001 inches).
Machine tool condition and performance, methods and the insert types, as well as
edge preparation, are also important for the final machining effect. Edge rein-
forcement with –20° chamfer is typically applied when machining hard steels.
Polycrystalline CBN is an ideal cutting tool material for machining iron-based
workpiece materials, but in a production environment cost per piece is one of the
ultimate considerations. Excelent surface finish can be obtained in good, stable
machining conditions, and the harder the workpiece material is, the more advanta-
geous the use of CBN will be. As a rule, CBN tools are recommended for hard-
nesses above 50 HRC up to about 70 HRC to generate finishes down to
Ra
=
0.3 µm. Low-content CBN (45–65%), in combination with a ceramic binder,
has better shock and wear resistance and chemical stability, and is better suited
to hard steel components. Oppositely, higher-content CBN, which is tougher, is
more suitable for hard cast-iron and high-temperature alloys. A sufficiently large
tool radius and suitable edge reiforcement are also important. Honing of the cut-
ting edge reduces risk of microchipping. A typical S-edge treatment combines
a 0.1 mm × 20° chamfer with a radius on the cutting edge. Recently, both mixed
ceramic and CBN inserts are offered in so-called wiper configuration with special
smothing micro-edges or Xcel geometry with the smaller approach angle resulting
in a reduced chip thickness relative to the feed rate [6].
Some newely designed CBN inserts are shown in Figure 4.8. Figure 4.8(a)
shows the petite inserts (NEW PETIT CUT by Mitsubishi Carbide) in which the
CBN tip is directly brazed to the host carbide insert. This results in a stronger CBN
blank and allows more of the generated heat to be absorbed. All negative CBN
inserts produced by Sandvik Coromant are equipped with mechanically interlocked
CBN brazed corners (called Safe-Lok), as shown in Figure 4.8(c). This design
gives suprior strength and security of the cutting edges, especially beneficial when
machining up to shoulders, undercuts and in other profiling operations. In order to
simplify detection of used edges, the insert is coated with a thin, golden TiN film.
Figure 4.8. Examples of CBN inserts: (a) CBN tip brazed directly to the host carbide insert,
(b) double-sided, multicorner insert, (c) insert with mechanically interlocked CBN solid
corners brazed far from the hot tool–chip contact, (d) CBN insert equipped with chip
breaker and (e) solid PCBN insert coated with cooper coloured (Ti,C) Al layer [6]