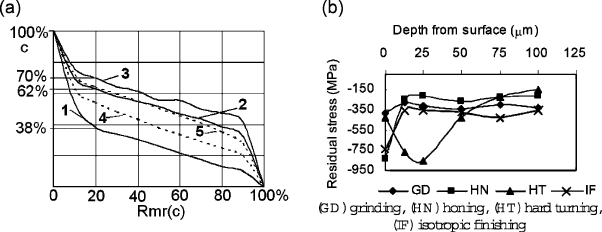
Machining of Hard Materials 117
In the contact zone, the austenite temperature of the workpiece material is
reached after an extremely short time of approximately 0.1 ms and structural
changes must be expected [11]. A metallurgically unetchable structure, called the
white layer, followed by a dark etching layer, results from microstructural changes
observed in hard machining, for example, on AISI 52100 steel surfaces of 60 HRC
hardness (Figure 4.23). The three lower scanning electron microscopy (SEM)
images show the white layer, the underlying dark layer and the bulk material,
consisting of carbides distributed in a martensitic matrix. In general, carbide size
and its distribution in both the white and dark layers indicate no difference from
the bulk.
4.4.4 Modification of Surface Finish in Hybrid Processes
In general, as shown in Figure 4.24(a), the shapes of the bearing (Abbot’s) curves
obtained with conventional CBN and MC cutting tools are not satisfactory and the
surfaces machined by hard turning require further improving by finishing belt
grinding or super-finishing operations. Additionally, it is possible to generate,
using a special wiper tools with varying chamfer geometry, the flatness of the
bearing area curve (BAC) comparable to honing effect [7].
The residual stress profiles for the four finished surfaces on a 58–62 HRC car-
burized medium carbon steel are presented in Figure 4.24(b). It can be observed in
Figure 4.24(b) that, although the surface compressive stress of the HT bearing is
less than the HN bearing, its area of compressive stress is much wider, which
leads to higher relative bearing life. In contrast, the GD surface has the lowest
surface stress and unsuitable surface finish (Table 4.1), which decrease the fatigue
life of such bearing surfaces.
In order to compare the four differently machined bearing surfaces some key
2D and 3D roughness parameters are given in Table 4.1. In contrast, IF generates
the lowest average roughness Ra and GD the highest one. This trend is also ob-
served for the maximum roughness height Rt. The values of the plasticity index
Ψ
exceed unity (indicating that the asperities are deformed plastically) in all cases
Figure 4.24. Comparison of hard turned and abrasive finished surfaces. (a) Differences in
BAC curves obtained in CBN (1) and MC (4) hard turning and finish abrasive processes
(preliminary (2) and finish (3) belt grinding and super-finishing (5)) after [33]. (b)
Distributions of residual stresses [37]