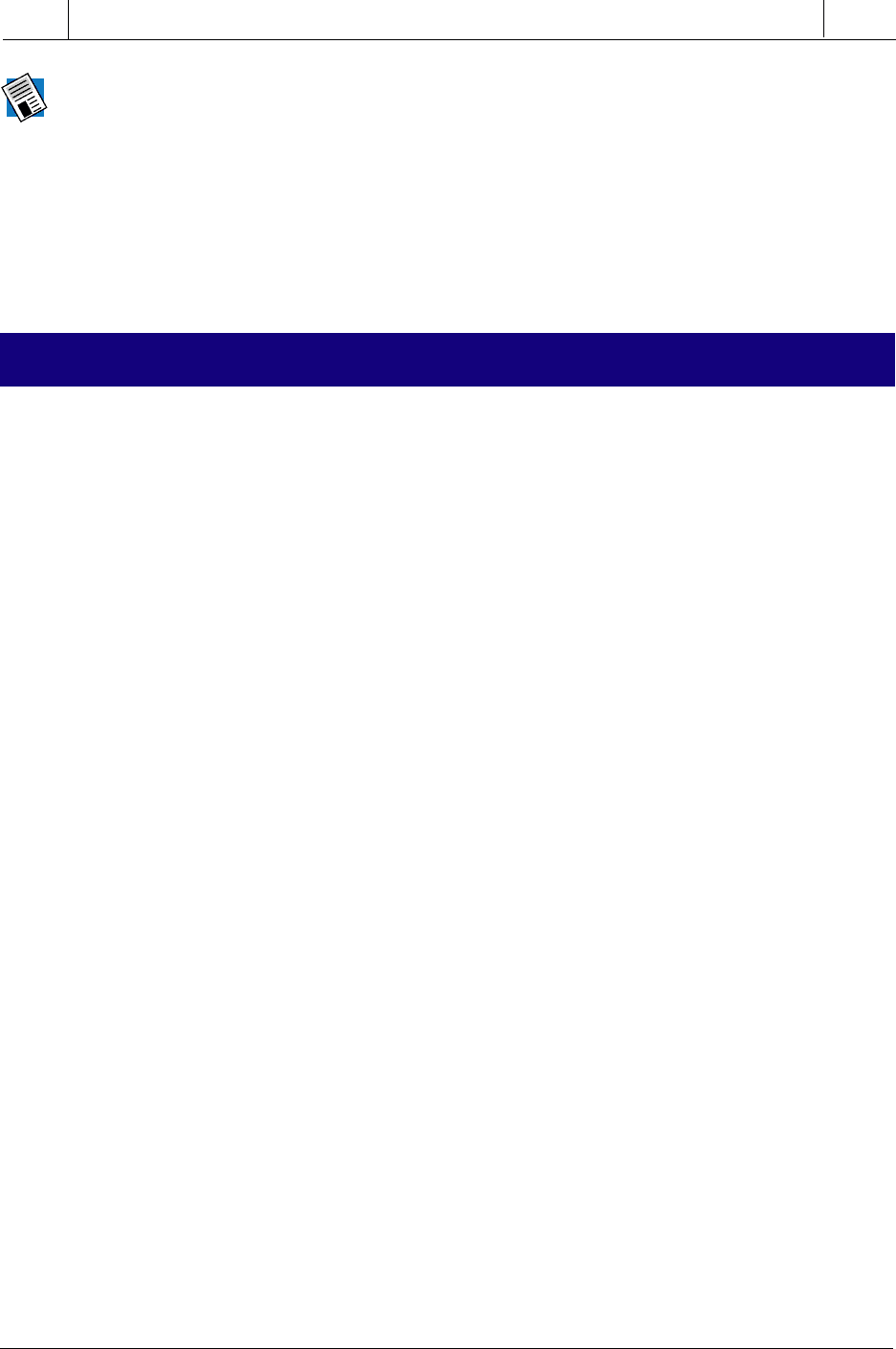
610
SECTION
4
PLC Process
Applications
Industrial Text & Video Company 1-800-752-8398
www.industrialtext.com
CHAPTER
14
Process Responses
and Transfer Functions
As we have already discussed, PLCs control machines and processes via
discrete, analog, and special I/O interfaces that communicate with the real
world. With the aid of control software, a user can program a PLC to control
any process through these I/O interfaces. In our discussion, however, we
have not yet explained process control in its true form, as it applies to the
behavior and control of a manufacturing activity. Therefore, we will
dedicate this chapter to the explanation of basic process control concepts. In
the next chapter, we will explain how these concepts apply to a process
control operation.
CHAPTER
HIGHLIGHTS
14-1 PROCESS CONTROL BASICS
Process control is the regulation of designated process parameters to within
a specified target range or to a set target value called the set point. Process
control is most often used in product manufacturing, because many factors,
such as color, composition, and density, must be accurate for a product to be
well made. Therefore, to implement a quality product, process control is used
to monitor and correct process parameters by analyzing the state of dynamic
variables. Dynamic variables are process characteristics, such as tempera-
ture, flow, and pressure, that vary with time. Through its I/O interfaces, a
PLC can regulate these dynamic variables to a desired set point, thus
implementing process control.
Figure 14-1 illustrates the basic concept of process control using a reactor tank
in which steam controls the temperature in the tank. In this case, the
temperature must be maintained at a target value, or set point, of 125°C.
Because it varies with time, the temperature is the dynamic variable, which
is also called the process variable (PV). The steam level, which regulates
the process variable (i.e., raises and lowers the temperature), is called the
control variable (CV). The valve that controls the amount of steam entering
the reactor tank’s jacket is called the control element, or final output field
device, because the more the controller opens the valve, the more the steam
increases the temperature.
Figure 14-2 shows the block diagram of the process control system illus-
trated in Figure 14-1. The PLC reads the process variable from the system
(i.e., obtains feedback) and compares it with the set point to determine how
well the temperature is being regulated. This configuration is known as a
closed-loop system, because the controller uses feedback to monitor the
system. An open-loop system does not use feedback, so the controller does
not receive process variable data. Figure 14-3 illustrates the configuration of
an open-loop system.
If the temperature reading in the process in Figure 14-2 is low, the controller
will adjust the control variable by opening the valve to allow steam to enter
the tank, thereby raising the temperature. The controller will then recheck