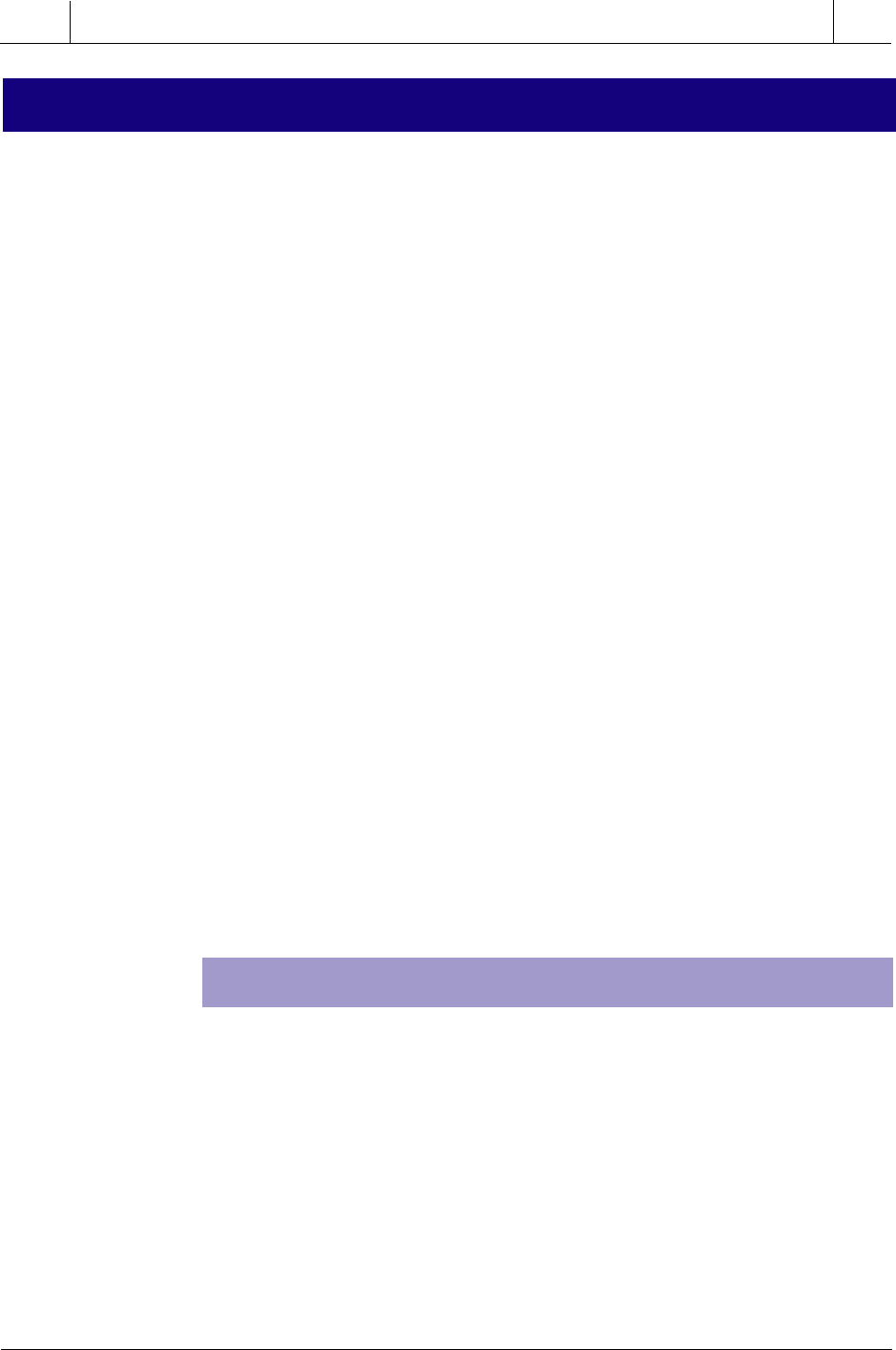
560
SECTION
4
PLC Process
Applications
Industrial Text & Video Company 1-800-752-8398
www.industrialtext.com
CHAPTER
13
Data Measurements
and Transducers
13-2 INTERPRETING ERRORS IN MEASUREMENTS
The discovery of errors is invaluable when controlling a machine or process
because error information helps the user improve the system. Errors can be
discovered in anticipation of the outcome (error prediction) or after a product
is made (error detection). Error prediction is more useful than error detection,
but it is harder to implement. Detection of an error after a product is made is
fairly easy, since the final product can be checked against a reference model
that matches all specifications. Although error prediction is much more
useful, error detection is better than not discovering the error at all. For
example, it is better to stop production of a machined piece because it has
been found that the piece does not meet the customer’s specifications than to
ship a bad product to the customer.
Once an error is detected, it can be interpreted using statistical analysis. This
type of statistical data analysis is, in fact, part of the foundation of artificial
intelligence systems. These systems continuously collect data about a
process and adjust production parameters accordingly. They then store their
data measurements in a global database for use in later statistical analysis
(see Chapter 16 for more about artificial intelligence systems).
In automated control systems, the controlling system and the process itself
usually generate system errors. Several events, composed of a mix of several
process errors, may combine to form a compounded system error. Likewise,
guarantee errors, caused by errors in raw materials or supplies, may also
generate system errors. Because their cause can be found, system errors can
be predicted and corrected.
Unknown events that occur during the process create random errors. There-
fore, unlike system errors, random errors can only be detected and corrected,
not predicted. Most of the time, the user must employ statistical analysis to
detect and remedy these errors.
INTERPRETING COMBINED ERRORS
Combined errors are errors caused by the interaction of two or more indepen-
dent variables, each one causing a different problem. The system propagates
the interaction of these variables; therefore, combined errors are also called
propagation errors. By calculating statistical data about the sample before
propagation and knowing the average and standard deviation requirements
for the final product, the user can predict the outcome of the final product
and make corrections for propagation errors throughout the process.
The value of an outcome formed by several variables (e.g., materials going
into a batching process) is directly related to the average value of each
variable. For instance, if a batching process uses two ingredients, A and B,