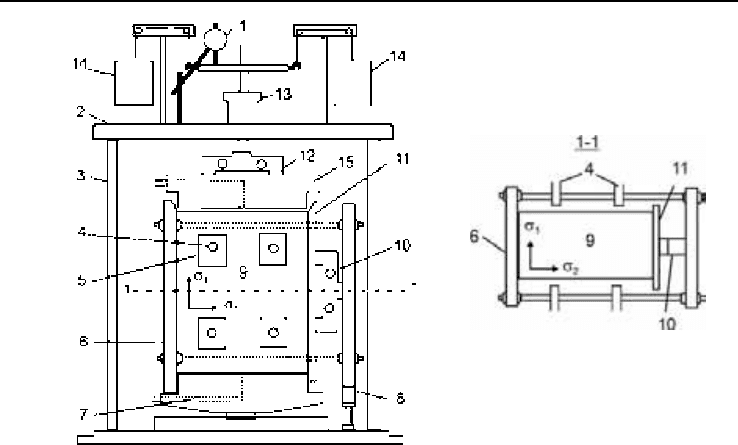
Испытания в условиях плоской деформации
461
(а)
(б)
Рис. 10.2. Схема прибора (а) и сечение 11 (б) (Yasin et al., 1999):
1 – цифровой индикатор перемещения; 2 – верхняя плита; 3 – стойка камеры;
4 – бесконтактный датчик для измерения
3
;ε
5 – кусочек алюминиевой фольги;
6 – прозрачная стенка из акрила; 7 – нижний штамп; 8 – датчик силы для измерения трения;
9 – образец; 10 – датчик силы для измерения
2
;σ
11 – стальная стенка;
12 – датчик силы для измерения
1
;σ 13 – направляющая втулка с подшипником;
14 – противовес; 15 – верхний штамп
Детальное описание второго типа прибора плоской деформации приведено
в работе Ogubekun (1988). Это прибор с контролем напряжений при нагру
жении, в котором границы
1
σ и
3
σ являются гибкими и создаются воздухом,
который подается в резиновые подушки (рис. 10.3). Две другие боковые
границы
2
σ выполнены жесткими: одна сделана из стали, а вторая – из акрила
с покрытием латексом толщиной 0,3 мм и смазкой. Образец имеет размеры
100×100×100
мм и покрыт резиновой оболочкой толщиной 0,3 мм.
Датчики силы для измерения трения на границе
2
σ
отсутствуют. Новым в
этой конструкции прибора является механизм регулирования границ
1
σ
и
2
σ
образца, действующий так, чтобы они оставались плоскими при дефор
мировании образца грунта. Это достигается использованием обратной связи с
контактными датчиками, которые закреплены в центральной части
внутренней поверхности резиновых подушек давления (см. рис. 10.3).
Вначале шток датчика на границе
1
σ поверхности находится в касании с ней,
а на
3
σ
поверхности отделены. При создании девиатора напряжения границы
1
σ и
3
σ образца становятся вогнутыми и выпуклыми, соответственно при этом