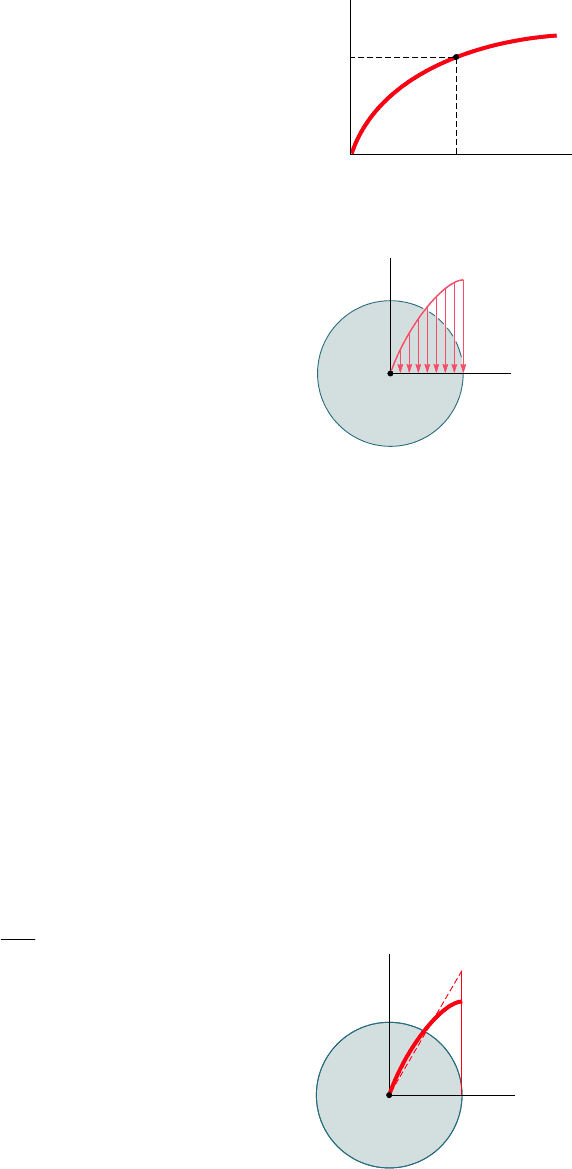
Apago PDF Enhancer
185
Assuming that the maximum value t
max
of the shearing stress t
has been specified, the plot of t versus r may be obtained as follows. We
first determine from the shearing-stress-strain diagram the value of g
max
corresponding to t
max
(Fig. 3.31), and carry this value into Eq. (3.4).
Then, for each value of r, we determine the corresponding value of g
from Eq. (3.4) or Fig. 3.30 and obtain from the stress-strain diagram
of Fig. 3.31 the shearing stress t corresponding to this value of g. Plot-
ting t against r yields the desired distribution of stresses (Fig. 3.32).
We now recall that, when we derived Eq. (3.1) in Sec. 3.2, we
assumed no particular relation between shearing stress and strain.
We may therefore use Eq. (3.1) to determine the torque T corre-
sponding to the shearing-stress distribution obtained in Fig. 3.32.
Considering an annular element of radius r and thickness dr, we
express the element of area in Eq. (3.1) as dA 5 2pr dr and
write
T 5
#
c
0
rt12pr dr2
or
T 5 2p
#
c
0
r
2
t dr
(3.26)
where t is the function of r plotted in Fig. 3.32.
If t is a known analytical function of g, Eq. (3.4) may be used
to express t as a function of r, and the integral in (3.26) may be
determined analytically. Otherwise, the torque T may be obtained
through a numerical integration. This computation becomes more
meaningful if we note that the integral in Eq. (3.26) represents the
second moment, or moment of inertia, with respect to the vertical
axis of the area in Fig. 3.32 located above the horizontal axis and
bounded by the stress-distribution curve.
An important value of the torque is the ultimate torque T
U
which causes failure of the shaft. This value may be determined from
the ultimate shearing stress t
U
of the material by choosing t
max
5 t
U
and carrying out the computations indicated earlier. However, it is
found more convenient in practice to determine T
U
experimentally
by twisting a specimen of a given material until it breaks. Assuming
a fictitious linear distribution of stresses, Eq. (3.9) is then used to
determine the corresponding maximum shearing stress R
T
:
R
T
5
U
c
(3.27)
The fictitious stress R
T
is called the modulus of rupture in torsion of
the given material. It may be used to determine the ultimate torque
T
U
of a shaft made of the same material, but of different dimensions,
by solving Eq. (3.27) for T
U
. Since the actual and the fictitious linear
stress distributions shown in Fig. 3.33 must yield the same value T
U
for the ultimate torque, the areas they define must have the same
moment of inertia with respect to the vertical axis. It is thus clear
that the modulus of rupture R
T
will always be larger than the actual
ultimate shearing stress t
U
.
3.9 Plastic Deformations in Circular Shafts
f( )
max
max
Fig. 3.31 Nonlinear, shear stress-
strain diagram.
O
c
max
Fig. 3.32 Shearing strain variation for
shaft with nonlinear stress-strain diagram.
O
U
c
R
T
Fig. 3.33 Shaft at failure.
bee80288_ch03_140-219.indd Page 185 11/2/10 3:06:52 PM user-f499bee80288_ch03_140-219.indd Page 185 11/2/10 3:06:52 PM user-f499 /Users/user-f499/Desktop/Temp Work/Don't Delete Job/MHDQ251:Beer:201/ch03/Users/user-f499/Desktop/Temp Work/Don't Delete Job/MHDQ251:Beer:201/ch03