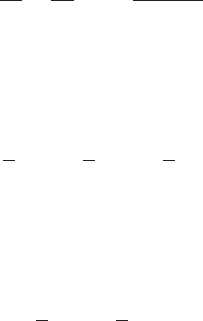
where the equivalent stiffness k
te
is
(2.22)
The potential energy for the torsion-spring combination shown in Fig-
ure 2.7a is given by
where we have used Eq. (2.12). For the torsion-spring combination shown in
Figure 2.7b, the system potential energy is given by
Equivalent Spring Constants of Common Structural Elements
Used in Vibration Models
To determine the spring constant for numerous elastic structural elements one
can make use of known relationships between force and displacement.
Several such spring constants that have been determined for different geom-
etry and loading conditions are presented in Table 2.3. For modeling pur-
poses, the inertias of the structural elements such as the beams of Cases 4
to 6 in Table 2.3 are usually ignored. In Chapter 9, it is shown under what
conditions it is reasonable to make such an assumption.
3
Since it may not always be possible to obtain a spring constant for a given
system through analysis, often one has to experimentally determine this con-
stant. As a representative example, let us return to Figure 2.4a, and consider
the experimental determination of the spring constant for this system. The
loading F is gradually increased to a chosen value and the resulting deflection
x from the unstretched position of the element is recorded for each value of F.
These data are plotted in Figure 2.8, where open squares are used to denote
the values of the experimentally obtained data. Then, assuming that the stiff-
ness element is linear, curve fitting is done to estimate the unknown param-
eter k in Eq. (2.9). The resulting value of the spring constant is also shown in
Figure 2.8. Note that the stiffness constant k is a static concept, and hence, a
static loading is sufficient to determine this parameter.
Force-displacement relationships other than Eq. (2.9) may also be used
to determine parameters such as k that characterize a stiffness element.
Determinationofparameters for anonlinearspring is discussedinSection 2.3.3.
In a broader context, procedures used to determine parameters such as k of a
vibratory system element fall under the area called system identification or
1
2
k
t
1
u
1
2
1
2
k
t
2
u
2
2
V1u
1
, u
2
2 V
1
1u
1
2 V
2
1u
2
2
1
2
k
t
1
u
2
1
2
k
t
2
u
2
1
2
1k
t
1
k
t
2
2u
2
V1u 2 V
1
1u 2 V
2
1u 2
k
te
a
1
k
t1
1
k
t 2
b
1
k
t1
k
t2
k
t1
k
t2
34 CHAPTER 2 Modeling of Vibratory Systems
3
See Eqs. (9.105) and (9.162).