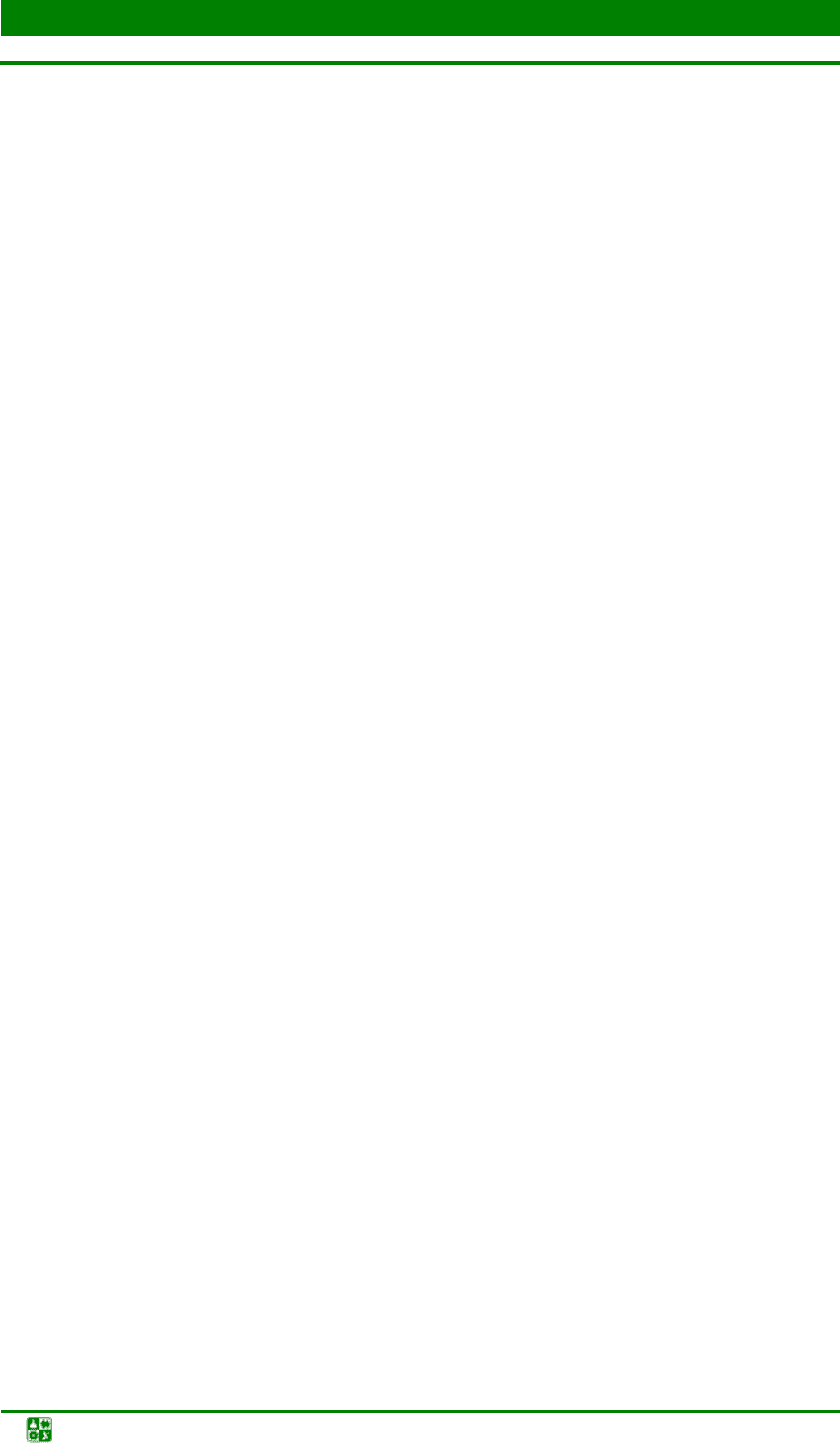
ГЛАВА 12. ТЕХНОЛОГИЧЕСКИЕ ПРОЦЕССЫ ФОРМИРОВАНИЯ ЗАДАННЫХ ФИЗИКО-МЕХАНИЧЕСКИХ И
ЭКСПЛУАТАЦИОННЫХ СВОЙСТВ ПОВЕРХНОСТНЫХ СЛОЕВ
12.1. Наплавка и газотермическое нанесение покрытий
Технология конструкционных материалов. Учебное пособие -420-
горящая между водоохлаждающими электродами. В качестве плазмообра-
зующих газов применяют аргон, водород, азот, аммиак, гелий, воздух и др.
Частицы порошка, попадая в плазменную струю, расплавляются и перено-
сятся на поверхность обрабатываемого изделия.
При детонационном напылении источник нагрева представляет собой
высокоскоростной поток газовой смеси, образующийся в результате направ-
ленного взрыва, обусловленного детонацией. Скорость продуктов детонации
определяет скорость напыляемых частиц, которая обычно составляет 800–
1200 м/c.
При электродуговом напылении образование потока наплавляемых
частиц происходит в результате плавления материала высокоамперной дугой.
Особенностью горения дуги в электрометаллизаторе является воздействие
мощного скоростного потока распыляющего газа, в результате чего
происходит сжатие дуги, температура которой достигает 4000 °С.
Процесс высокочастотного напыления основан на использовании
токов высокой частоты. Помещенный в индуктор стержень (проволока)
расплавляется вихревыми токами, возникающими под действием перемен-
ного магнитного поля, образующегося при прохождении высокочастотного
тока по катушке. Расплавленный металл распыляют струей сжатого воздуха
и наносят на обрабатываемую поверхность. При напылении металлов,
активно взаимодействующих с кислородом, используют инертные газы.
Газотермическое нанесение покрытий может о
существляться как при
атмосферном, так и при пониженном или повышенном давлении. Размер
частиц наплавляемого материала существенно влияет на структуру и свой-
ства покрытия. С увеличением размера частиц повышается плотность и одно-
родность покрытия. Частицы размером менее 10 мкм становятся непригод-
ными для напыления на воздухе, так как они не дост
игают поверхности
изделия, поскольку увлекаются потоком газа, обтекающим изделие.
Различные способы газотермического напыления применяют для
получения коррозионно-стойких, износостойких, жаростойких и других
покрытий из алюминия, цинка, сталей, бронзы, карбидов вольфрама,
керамики. Размеры и форма изделий при этом методе не ограничены, а
толщина покрытия может составлять от 0,1 до 2 мм. Для получения прочного
соединен
ия покрытия с поверхностью заготовки необходима ее специальная
подготовка. Перед нанесением металла толщиной до 1 мм поверхность
обдувают корундом для очищения, придания необходимой шероховатости и
активации. Если напыляют более толстые слои, то шероховатость
обеспечивают черновым точением или фрезерованием канавок типа
«ласточкин хвост».
Преимуществом газотермического нанесения покрытий является воз-
можность применения широкого спектра материалов и проведение процесса
как в атмосфере, та
к и в защитных камерах. Недостатками являются высокая
стоимость процесса, относительно низкая производительность, высокий
уровень шума.