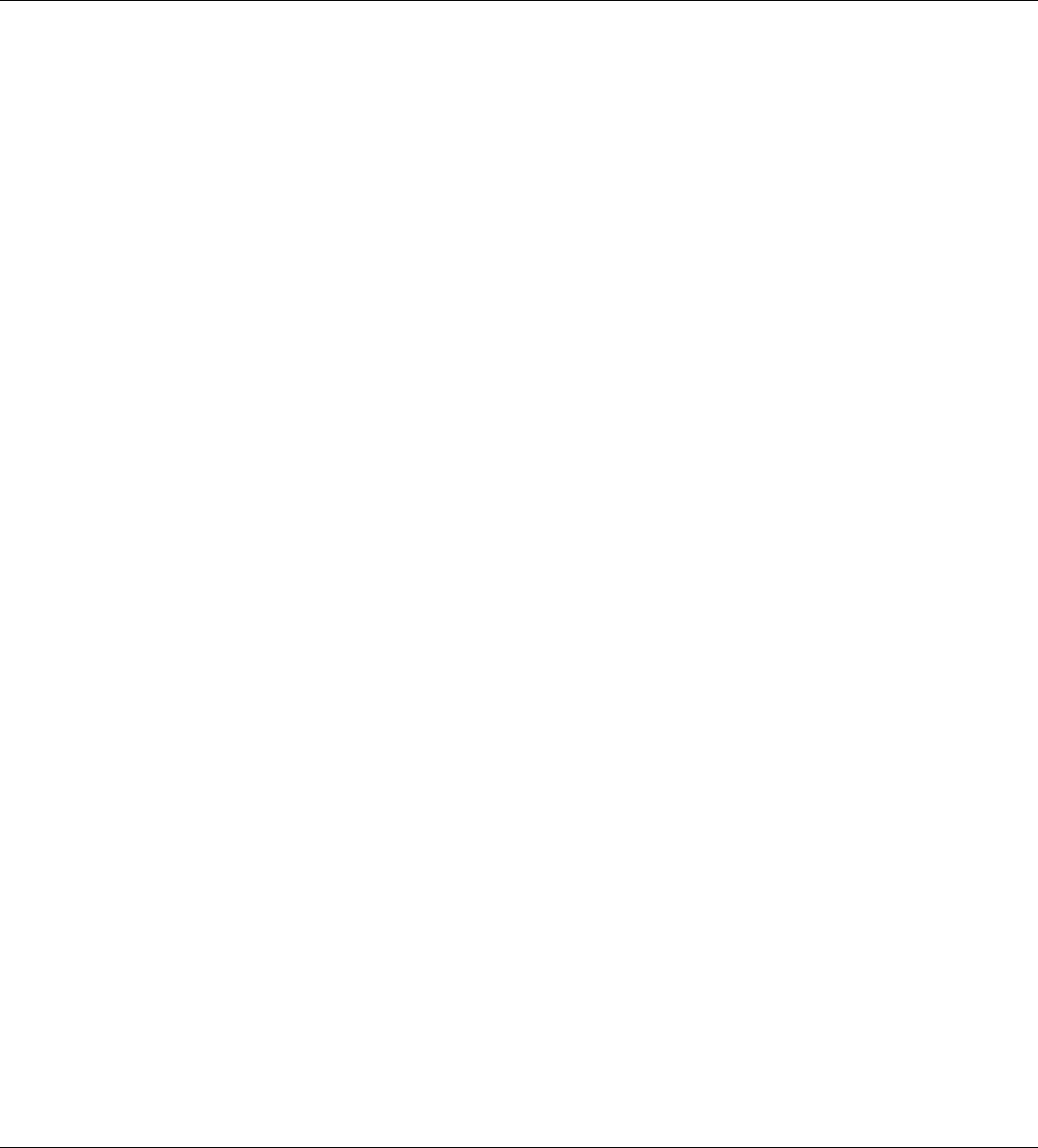
Ultrasonic Fatigue Testing
Historical Perspective
Development of higher-frequency testing machines began early in the 20th century. Prior to 1911, the highest
fatigue testing frequency was on the order of 33 Hz, using mechanically driven systems. Electrodynamic
resonance systems appeared in 1911 when Hopkinson (Ref 1) introduced a machine capable of 116 Hz. In
1925, Jenkin (Ref 2) tested wires of copper, iron, and steel at 2 kHz, using similar techniques. In 1929, Jenkin
and Lehmann (Ref 3) were able to test materials up to 10 kHz using a pulsating air resonance system.
Mason (Ref 4) achieved ultrasonic frequency (20 kHz) in 1950 with the adaptation of magnetostrictive and
piezoelectric-type transducers to fatigue testing. This method translated 20 kHz electrical voltage signals into
20 kHz mechanical displacements. A displacement-amplifying acoustical horn and the test specimen were
driven into resonance by the transducer. This concept has remained basically unchanged and is the foundation
of the practices used in modern ultrasonic fatigue test technology.
In the early 1960s, frequencies as high as 92 and 199 kHz were employed for fatigue tests using Mason's
techniques (Ref 5, 6) These extremely high frequencies surpass the upper limits of practicality because of the
constraints of specimen size (frequency is inversely proportional to specimen length), machining tolerances,
strain amplitude measurements, and energy considerations. A review of the ultrasonic fatigue testing in the
1970s and 1980s shows that the majority of test stands operate at frequencies between 17 and 25 kHz.
This unofficial standard is primarily dictated by the availability of commercial high-power ultrasonic
transducers and power supplies. These frequencies are also desirable from a safety viewpoint because they are
above the range of normal human hearing. Fatigue testing at 20 kHz proceeds quietly in comparison to testing
at 1 to 10 kHz.
References cited in this section
1. B. Hopkinson, Proc. R. Soc. (London) A, Vol 86, 1911, p 101
2. C.F. Jenkin, Proc. R. Soc. (London) A, Vol 109, 1925, p 119.
3. C.F. Jenkin and G.D. Lehmann, Proc. R. Soc. (London) A, Vol 125, 1929, p 83
4. W.P. Mason, Piezoelectric Crystals and Their Application in Ultrasonics, Van Nostrand, New York,
1950, p 161
5. F. Girard and G. Vidal, Rev. Metall., Vol 56, 1959, p 25.
6. M. Kikukawa, K. Ohji, and K. Ogura, J. Basic. Eng. (Trans. ASME D), Vol 87, 1965, p 857
Ultrasonic Fatigue Testing
Strain Rates, Frequency, and Time Compression
Ultrasonic fatigue testing increases the frequency of stress cycling to reduce the time necessary to accumulate a
large number of cycles. Consequently, the strain rate at these frequencies for a given strain amplitude is also
increased. In Table 1, strain rate is calculated as a function of frequency and strain amplitude. For typical
fatigue strain amplitudes in the range of 10
-4
to 10
-3
, the strain rate at 20 kHz ranges from 2 to 20 s
-1
.