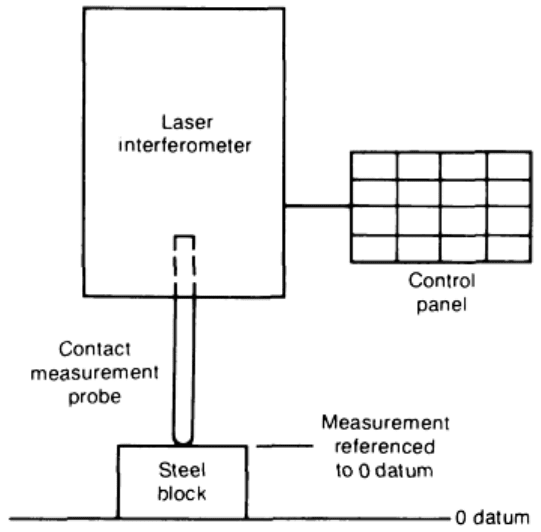
Whenever the measurement target mirror or retroreflector moves, the accompanying Doppler effect induces a frequency
shift in the returning beam. Because of their orthogonal polarization, the frequencies do not interfere to form fringes until
the beam reaches the receiver. Consequently, the receiver can monitor the frequency shift associated with the Doppler
effect, which is compared to the reference frequency to yield precise measurement of displacement.
The principal advantage of the two-frequency system is that the distance information is sensed in terms of frequency.
Because a change in frequency is used as the basis for measuring displacement, a change in beam intensity cannot be
interpreted as motion. This provides greater measurement stability and far less sensitivity to noise (air turbulence,
electrical noise, and light noise). Because motion detection information is embedded in the frequency of the measurement
signal, only one photodetector per measurement axis is required; this decreases the sensitivity of optical alignment.
Another advantage of the two-frequency interferometer is that the laser head need not be mounted on the machine or
instrument being tested.
Typical applications include the calibration of length-measuring standards such as glass scales and the characterization of
positional, angular, and straightness errors in precision equipment, such as machine tools, coordinate measuring
machines, and X-Y stages. The linear resolution of a two-frequency displacement interferometer is 1 nm (0.05 μin.), the
angular resolution is 0.03 arc seconds, and the straightness resolution is 40 nm (1.6 μin.).
The laser interferometric micrometer uses interferometric technology and a laser beam to perform absolute length
measurements to a resolution of 0.01 μm (0.4 μin.) with an accuracy of ±0.08 mm (±0.003 in.). A contact probe interfaces
with an internal interferometer that measures changes in distance (Fig. 8). The part to be measured is placed under the
probe, and the interference effects are electronically analyzed and displayed in terms of the distance from the probe to the
datum (Fig. 8).
Based on user-entered information, the system can
automatically compensate for room temperature,
humidity, atmospheric pressure, the temperature of the
part, and the thermal expansion of the probe. The
instrument performs gage comparison, maximum and
minimum surface deviation, and total indicator reading
measurements. Simple statistical functions include mean
and one standard deviation reporting. Actual measurement
readings can be compared to user-entered tolerance limits
for automatic "go, no-go" testing.
Sorting. Parts can be sorted by dimension, prior to
automatic assembly, with an in-process inspection system.
A laser beam sorting system can provide accept-or-reject
measurements of length, height, diameter, width, thread
presence, and count. Each production run of a different
part requires a simple setup to accommodate the part to be
measured.
In operation, a collimated laser beam is optically
processed, focused, and directed onto the part. A
photodetector converts the light signals to electrical
signals for processing. For length inspection, the laser
beam is split into three beams. The center beam is
stationary and acts as a reference beam. Both of the other
two beams are adjusted independently by micrometer
dials to define the distance between an over- or undersize
measurement. The parts can then be gravity fed past the laser quantification system for accept-or-reject measurement. In
many applications, parts can be inspected at a rate of 100 to 700 parts per minute. A typical application for a laser-based
sorting system is the in-process, accept-or-reject measurement of bolts, nuts, rivets, bearings, tubes, rollers, and
stampings.
Holography is an important measurement technique in the three-dimensional contouring of large spatial areas.
Holography can determine small deviations (as small as 0.1 μm, or 4 μin.) in surface shape over large areas for all types
of surface microstructure. This is accomplished by illuminating both the object and the hologram of its original or desired
Fig. 8 Schematic of a laser interferometric micrometer