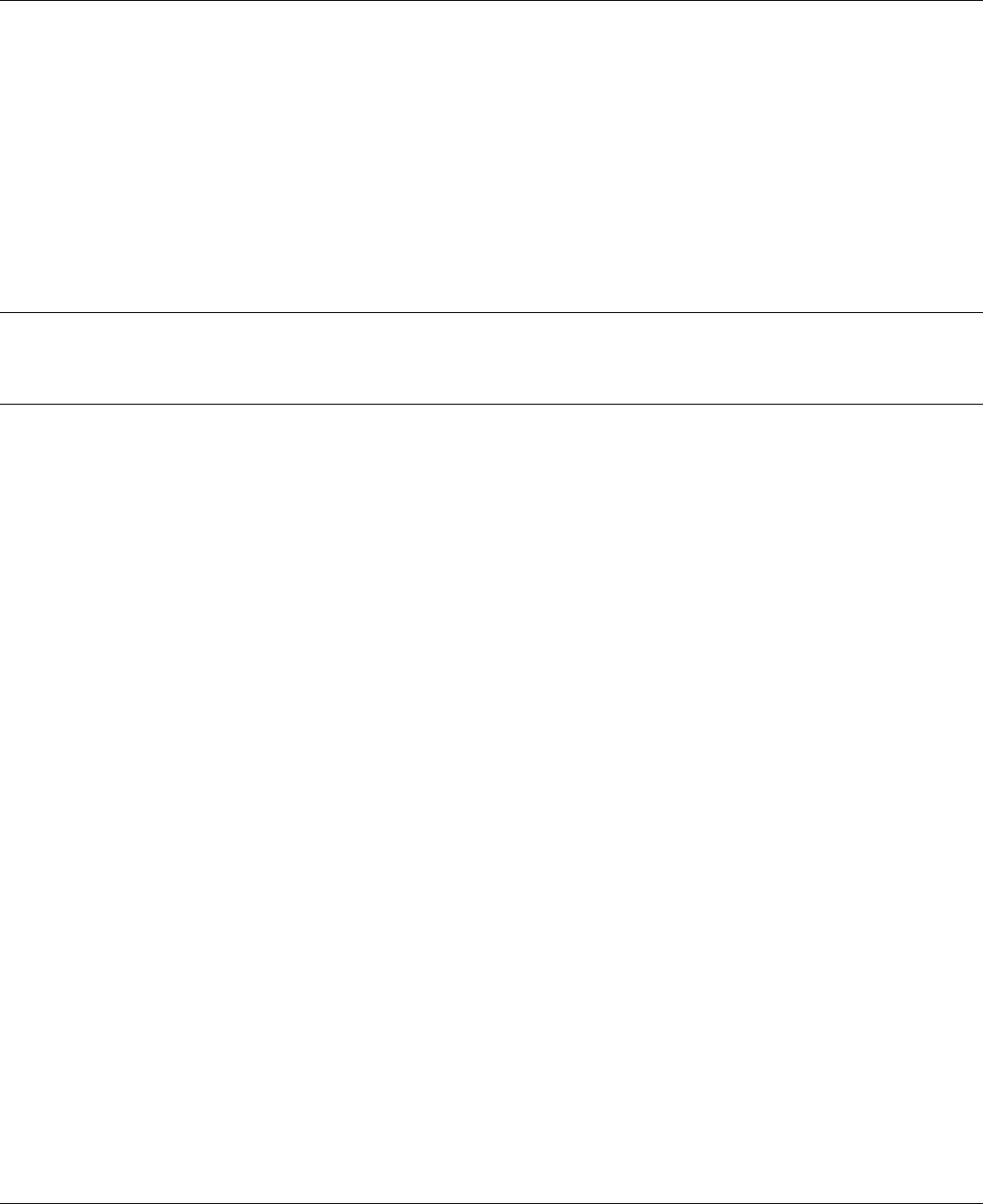
a given pair of columns, the two columns are balanced or orthogonal. Figure 18 shows that all column combinations have
an equal number of 11, 12, 21, and 22 combinations; therefore, all interactions are within the experimental design. After
the eight experiments are completed, the data are analyzed according to a prescribed procedure in order to determine the
level of each variable that contributes to the most robust (most insensitive process) combination of processing variables.
References cited in this section
13.
N.M. Wang and S. Tang, Ed., Computer Modelin
g of Sheet Metal Forming Processes: Theory, Verification, and
Application, The Metallurgical Society, 1986
14.
H. Yamasaki, T. Nishiyama, and K. Tamura, Computer Aided Evaluation Method for Sheet Metal Forming in Car
Body, in Proceedings of the 14th Biennial Congress of the IDDRG
(Koln, Germany), International Deep Drawing
Research Group, April 1986, p 373-382
15.
K. Chung and D. Lee, Computer-
Aided Analysis of Sheet Material Forming Processes, in Advanced Technology of
Plasticity, Proceedings of the First International Conference of Plasticity
(Tokyo), Japan Society for Technology of
Plasticity and Japan Society of Precision Engineering, 1984, p 660-665
16.
Y. Wu and W.H. Moore, Quality Engineering--Product and Process Design Optimization, American Suppl
Institute, 1985
Statistical Analysis of Forming Processes
Stuart Keeler, The Budd Company Technical Center
References
1. Statistical Quality Control Handbook, Western Electric Company, 1977
2. J.M. Juran, F.M. Gryna, Jr., and R.S. Bingham, Jr., Quality Control Handbook, McGraw-Hill, 1979
3. E.L. Grant and R. S. Leavenworth, Statistical Quality Control, 5th ed., Mc-Graw-Hill, 1980
4.
A.L. Strongrich, G.E. Herbert, and T.J. Jacoby, "Statistical Process Control: A Quality Improvement Tool," Paper
83099, Society of Automotive Engineers, 1983
5. General Motors Statistical Process Control Manual, Document 1893, General Motors Corporation, 1984
6. J.F. Siekirk, Process Variable Effects on Sheet Metal Quality, J. Appl. Metalwork., Vol 4 (No. 3), July 1986, p 262-
269
7.
"Final Report on Manufacturing Cost Study Conducted by Pioneering Engineering," American Iron and Steel
Institute, 1986
8. S. Dinda, K. James, S. Keeler, and P. Stine, How to Use Circle Grid Analysis for Die Tryout,
Metals, 1981
9. Sheet Steel Formability, American Iron and Steel Institute, 1984
10.
S.P. Keeler, Understanding Sheet Metal Formability, Sheet Met. Ind., Vol 48 (No. 5-10), 1971
11.
W.G. Brazier and S.P. Keeler, Relationship Between Laboratory Material Ch
aracterization and Press Shop
Formability, in Proceedings of Microalloying 75, Union Carbide, 1977, p 517-530
12.
S.P. Keeler, "Statistical Deformation Control for SPQC Monitoring of Sheet Metal Forming," Paper 850278, Society
of Automotive Engineers, 1985
13.
N.M. Wang and S. Tang, Ed.,
Computer Modeling of Sheet Metal Forming Processes: Theory, Verification, and
Application, The Metallurgical Society, 1986
14.
H. Yamasaki, T. Nishiyama, and K. Tamura, Computer Aided Evaluation Method for Sheet Metal Fo
Body, in Proceedings of the 14th Biennial Congress of the IDDRG
(Koln, Germany), International Deep Drawing
Research Group, April 1986, p 373-382
15.
K. Chung and D. Lee, Computer-Aided Analysis of Sheet Material Forming Processes, in Advance
Plasticity, Proceedings of the First International Conference of Plasticity
(Tokyo), Japan Society for Technology of
Plasticity and Japan Society of Precision Engineering, 1984, p 660-665
16.
Y. Wu and W.H. Moore, Quality Engineering--Product and Process Design Optimization,
Institute, 1985