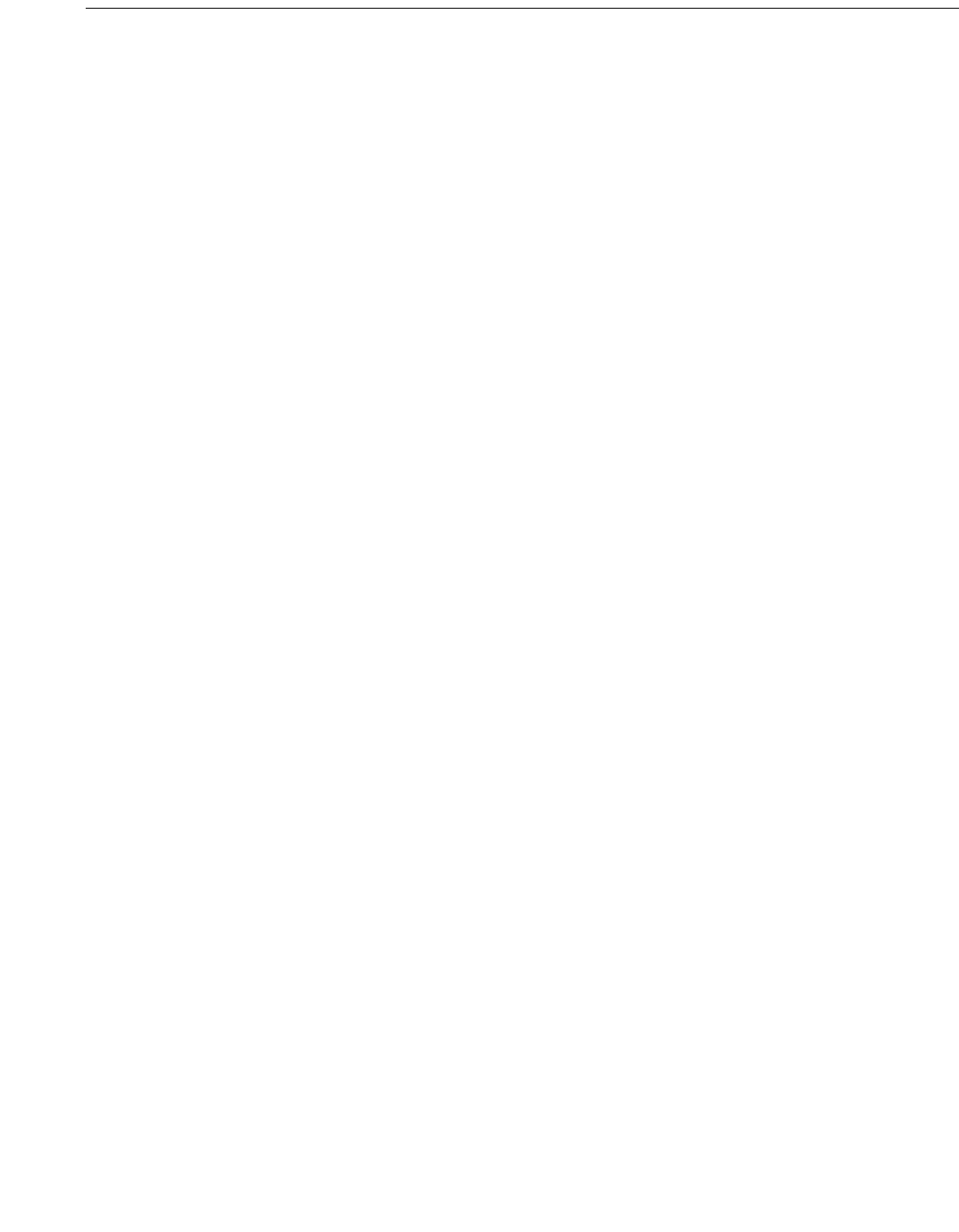
AXIAL AND CENTRIFUGAL COMPRESSORS AND EXPANDER-COMPRESSORS FOR PETROLEUM, CHEMICAL AND GAS INDUSTRY SERVICES 4-43
F.6.4.1.1 Local electronics, if required, shall be provided.
Local electronics to be suitable for specified hazardous area
and for specified ambient temperature and humidity range.
F.6.5 POWER INPUT FILTERS
F.6.5.1 Vendor shall provide EMF filters on control cabinet
power supply, if necessary, to avoid contamination of input
power by magnetic bearing power amplifiers.
F.6.6 MAN-MACHINE INTERFACE
F.6.6.1 Vendor’s standard MMI shall be provided. English
language shall be used.
F.6.7 UPS/BATTERY BACKUP SYSTEM
F.6.7.1 Vendor’s standard UPS/battery backup system shall
be provided if the customer’s UPS system is not utilized. It
shall allow a minimum of 5 min. of levitation upon loss of the
normal electric power supply.
F.6.7.2 Vendor’s monitoring system shall monitor the sta-
tus of vendor supplied batteries. Alarm and shutdown signals
shall be provided for low and low-low battery condition.
F.6.8 CABLING
F.6.8.1 The vendor shall specify cabling requirements for
the bearing power and sensor connections. Any electrical or
electronic components required to adjust for the installed
length shall be included in the vendor’s scope of supply.
Note: On systems where the cable distance between the expander-
compressor and the control cabinet are long (100 m – 300 m, or
300 ft – 1000 ft), special consideration should be given to the elec-
trical compensation and type of cable used to insure proper opera-
tion. In addition, long cable lengths are costly. For shop testing,
where the cable length is almost always shorter than field cable
lengths, electrical compensation is also necessary.
F.7 Shop Testing
F.7.1 All electronic components shall have a 24-hour burn-
in prior to shipment.
F.7.2 The insulation resistance of assembled bearing power
coils shall be greater than 50 megohms when tested with a
500 Volt DC megohmmeter.
F.7.3 The magnetic bearing control system shall be func-
tionally tested prior to shipment.
F.7.4 Static load capacity tests shall be performed on all
new bearing designs.
F.7.5 Static and dynamic test shall be performed using
cable provided by the vendor. In general, this will not be the
same cable as that used in the field. The vendor shall allow for
any special tuning adjustments in his design.
F.7.6 The dynamic test (mechanical running test) at the
vendor’s facility shall constitute shop acceptance of the mag-
netic bearing system. The acceptance criteria is as follows:
The maximum allowable rotor movement relative to the
center of the auxiliary bearing for any given axis of levitation
is 0.3 times the minimum radial clearance in the auxiliary
bearing in that axis. This movement can be the result of any or
all of various components, such as overall shaft vibration, cas-
ing distortion, aerodynamic loading, etc. However, the com-
bined total overall movement in any single axis, as measured
by the shaft position sensors, must not exceed 0.3 times the
minimum clearance to the auxiliary bearing in that axis. This
criteria supersedes all other vibration acceptance criteria as
described for oil bearing machines earlier in this specification.
Notes:
1. Magnetic bearings do not have a babbitted surface to fatigue
(like highly loaded oil film bearings) when subjected to high
vibration levels. In fact, transmitted forces in a magnetic bearing
equipped machine are minimized by allowing the shaft to rotate
about its inertial axis.
2. This criteria is somewhat like combining the AC and DC
components from a typical eddy current probe used on oil lubri-
cated machines. In effect, the magnetic bearing equipped rotor
must operate near the center of the clearance space provided by
the auxiliary bearing to avoid contact. If steady state forces or
internal misalignment cause the rotor to shift from this centered
position (i.e., the “DC” component), then less vibration (i.e., the
“AC” component) can be tolerated.
3. Example: Assume the minimum radial clearance from the
rotor to the auxiliary bearing is 250 microns (0.010 in.). 30% of
this value is 75 microns (0.003 in.). This represents the maxi-
mum shaft movement allowed relative to the center of the
auxiliary bearing clearance for this particular axis (radial or
axial). Thus, if the shaft operates eccentrically from the center by
50 microns (0.002 in.) in this axis, then the maximum allowable
overall vibration level allowed would be 25 microns (0.001 in.),
zero to peak. Note that this value is for one axis only, and is not
to be vectorially added to an orthogonal axis.
F.7.7 For new, unproven designs, a delevitation test shall be
performed during shop testing to verify that the auxiliary
bearings are acceptable for the intended duty. The delevita-
tion tests shall constitute shop acceptance of the auxiliary
bearing system. It shall be demonstrated that the auxiliary
bearing system can meet the following requirements:
While operating the expander-compressor at the maximum
continuous speed, with radial and axial loads no less than
those expected during normal operation of the equipment in
the field, all axes shall be delevitated for a 3-sec. period, then
re-levitated. The machine will then be stopped and internal
clearances will be checked electrically. If these clearances are
still acceptable, a second delevitation test will be performed as
above. Following the second test, the expander-compressor
will be disassembled and inspected. Any parts showing unac-
COPYRIGHT 2002; American Petroleum Institute
Document provided by IHS Licensee=Shell Services International B.V./5924979112,
User=, 10/07/2002 18:49:21 MDT Questions or comments about this message: please
call the Document Policy Management Group at 1-800-451-1584.
-- | ||| | | | |||| || | |||| || | | | | ||| | |---