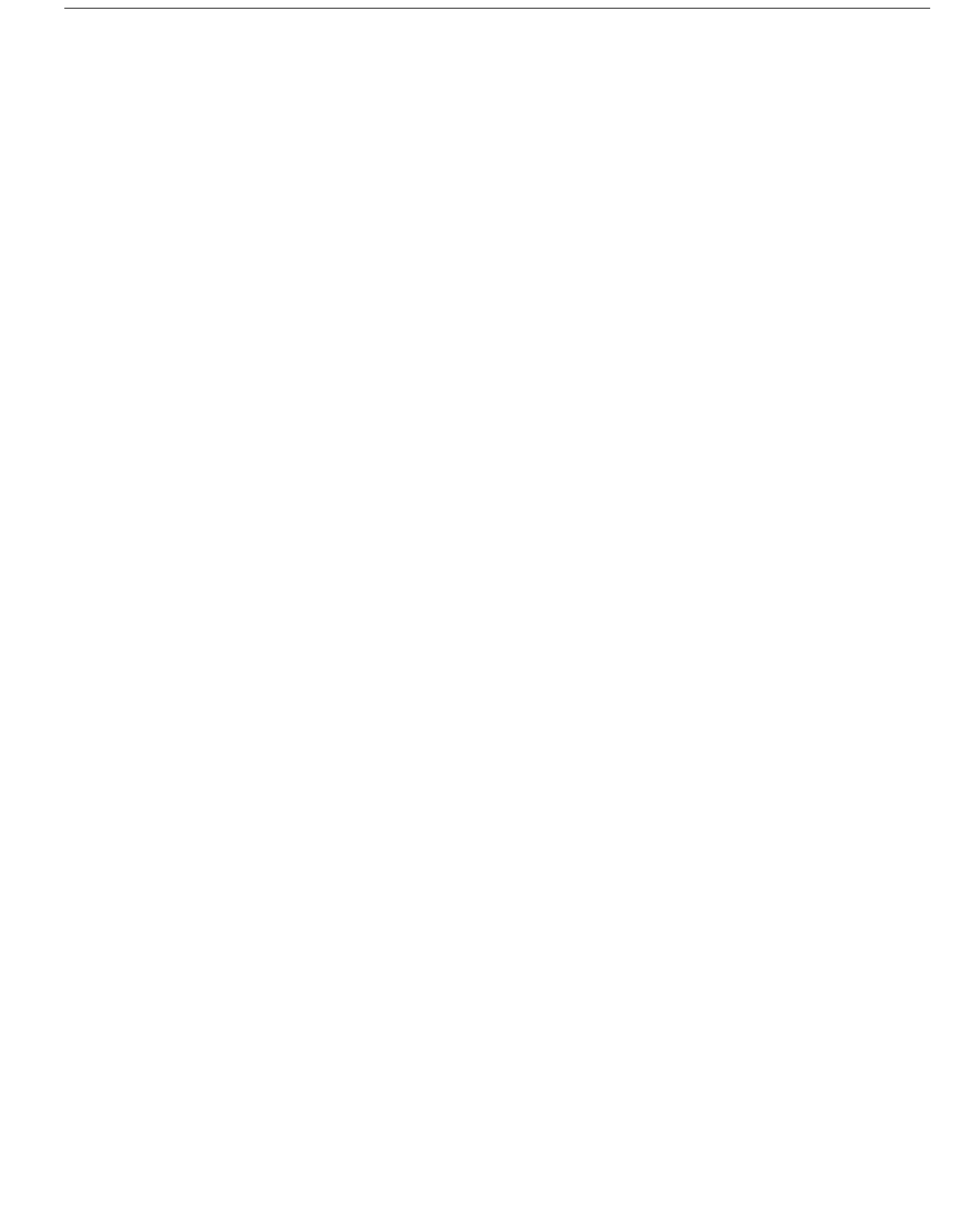
3-40 API STANDARD 617—CHAPTER 3
The rating formula’s given below are based on the methods
from AGMA 2101. The constant of 0.8 at the beginning of the
formulas below is to provide increased reliability.
F.1 Pitting Resistance Power Rating
The pitting resistance allowable transmitted power, P
az
, for
a gear set is:
(3.F-1)
where
ω
1
= pinion speed (rpm),
b = face width (mm),
d
w1=
operating pitch diameter of pinion (mm) =
2a/(u – 1),
a = center distance (mm),
u = gear tooth ratio (never less than 1.0),
Z
E
= elastic coefficient = 190 for steel pinion and
gear,
Z
I
= geometry factor (reference AGMA 908).
F.2 Bending Strength Power Rating
The bending strength allowable transmitted power, P
ay
, for
a gear pair is:
(3.F-2)
where
m
t
= transverse module (equal to normal module
divided by the cosine of the helix angle at the
standard pitch diameter),
Y
J
= geometry Factor (reference AGMA 908).
F.3 Load Distribution Factor,
K
H
If the value of K
H
calculated below is less than 1.1, then
1.1 shall be used as the value of K
H
. Gear designs shall not
result in a calculated value of K
H
over 1.50 without approval
from the purchaser.
K
H
= 1.0 + 0.8 (K
Hpf
+ 0.054 + 0.4032 ×
10
-3
b – 1.152 × 10
-7
b
2
) (3.F-3)
where
b = face width of narrower member of gear set
(mm)
K
Hpf
= bod – 0.025
when b ≤ 25 mm
= bod – 0.0375 + 0.000492 b
when 25 < b < 432
= bod – 0.1109 + 0.000815 b – 3.53 × 10
-7
b
2
when 432 < b ≤ 1020
bod = the greater of 0.05 or b/(10 d
w1
)
Note: The distance from the center of the gear mesh to the center of
the bearing span divided by the bearing span must be less than 0.175.
The tooth contact must be checked at assembly, with contact adjust-
ments as required. If these conditions are not met, or for wide face
gears, an analytical approach may be used to determine a more con-
servative load distribution factor, with prior approval by the purchaser.
F.4 Dynamic Factor,
K
v
ISO 1328 Grade 5 = > K
v
= 1.135
ISO 1328 Grade 4 = > K
v
= 1.120
ISO 1328 Grade 3 = > K
v
= 1.105
ISO 1328 Grade 2 = > K
v
= 1.090
The dynamic factor, K
v
, does not account for dynamic
tooth loads that may occur due to torsional or lateral natural
frequencies. System designs should avoid having such natural
frequencies close to an excitation frequency associated with
an operating speed since the resulting gear tooth dynamic
loads may be very high.
F.5 Stress Cycle Factors,
Z
N
and
Y
N
Z
N
= 2.466 N
-0.056
, pitting stress cycle (life) factor,
Y
N
= 1.6831 N
-0.0323
, bending stress cycle (life) factor.
N is the number of stress cycles,
N = pinion RPM 1.052 × 10
7
for the pinion,
N = bull gear RPM × 1.052 × 10
7
× number of pin-
ions in mesh for the bull gear.
Note: These factors are based on the lower line in Figures 17 and 18
of ANSI/AGMA 2101-C95 with 175,316 hours (20 years
× 365.242
days/year
× 24 hours/day) of continuous service at rated operating
speed.
F.6 Allowable Stress Numbers, σσ
σσ
HP
and
σσ
σσ
FP
The values of σ
HP
and σ
FP
shall be for Grade 2 materials
per ANSI/AGMA 2101-C95, Clause 16.
P
az
0.8
ω
1
b
1.91
7
×10
---------------------
Z
I
K
v
K
H
C
SF
----------------------
d
w1
σ
HP
Z
N
Z
E
-----------------------
2
=
P
ay
0.8
ω
1
d
w1
1.91
7
×10
---------------------
bm
t
Y
J
σ
FP
Y
N
K
V
K
H
K
SF
------------------------------
=
COPYRIGHT 2002; American Petroleum Institute
Document provided by IHS Licensee=Shell Services International B.V./5924979112,
User=, 10/07/2002 18:49:21 MDT Questions or comments about this message: please
call the Document Policy Management Group at 1-800-451-1584.
-- | ||| | | | |||| || | |||| || | | | | ||| | |---