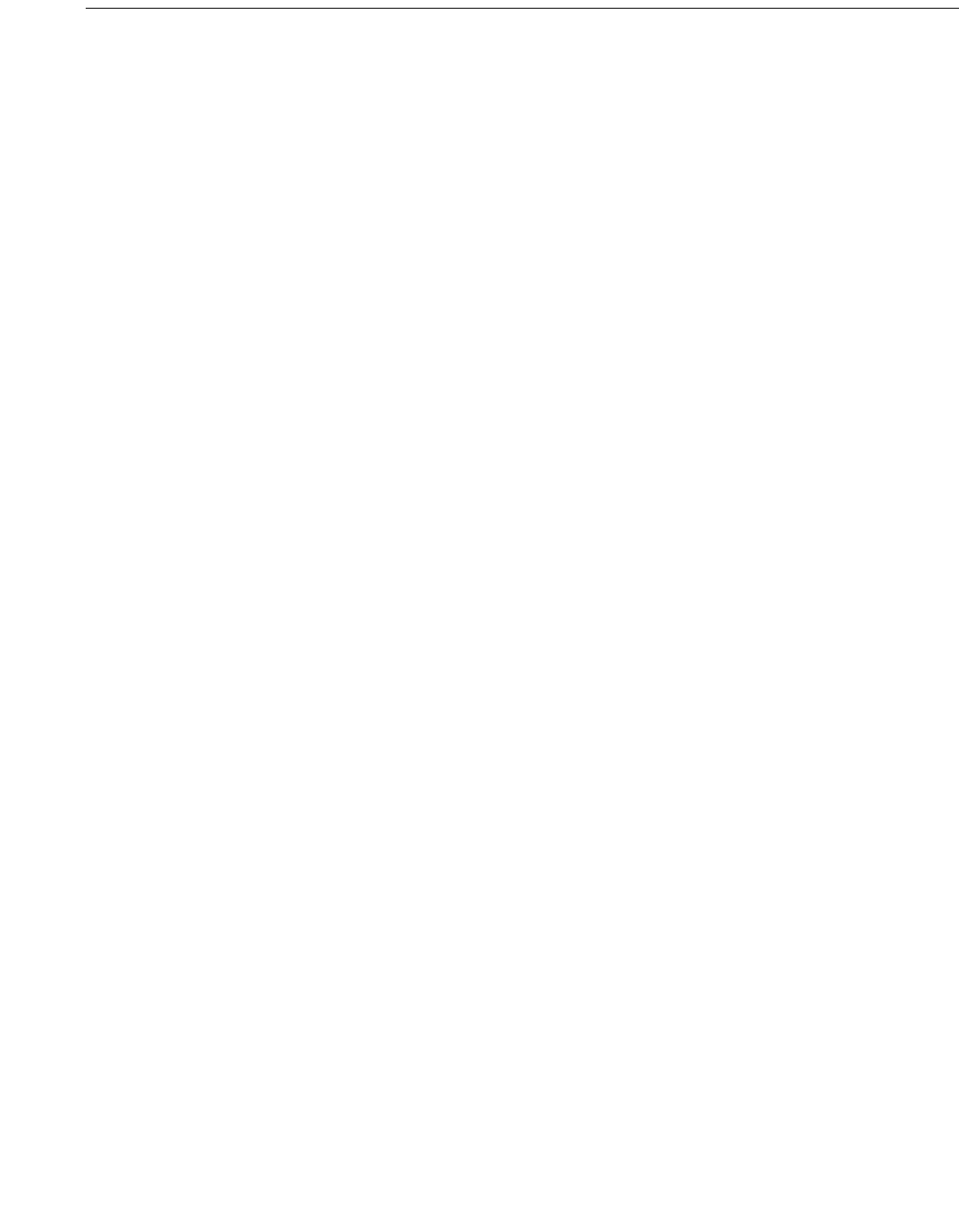
A
XIAL
AND
C
ENTRIFUGAL
C
OMPRESSORS
AND
E
XPANDER
-
COMPRESSORS
FOR
P
ETROLEUM
, C
HEMICAL
AND
G
AS
I
NDUSTRY
S
ERVICES
4-5
2.6.1.7 Residual Unbalance Procedure
When specified, a residual unbalance check shall be per-
formed on assembled rotors. The residual unbalance check
shall be performed after assembly balancing or assembly
check-balancing is complete and before the assembled rotor
is removed from the balancing machine.
Note: Refer to Annex 1B for a description of the procedure for resid-
ual unbalance verification.
2.7 BEARINGS AND BEARING HOUSINGS
2.7.1 General
2.7.1.1
Unless otherwise specified, hydrodynamic radial
and thrust bearings shall be provided.
Note: The typical expander-compressor has both the radial and
thrust bearing built into a single assembly.
2.7.1.2 When specified, magnetic bearings shall be sup-
plied in accordance with Annex 4F.
2.7.1.3 Since the bearings are generally in contact with the
process gas, bearing material selection criteria shall include
compatibility with the process gas as well as the normal factors
of strength, heat transfer rates, thermal growth properties, etc.
2.7.2 Hydrodynamic Radial Bearings
2.7.2.1 Sleeve or pad bearing types bearings shall be used.
The bearings shall be precision machined. Materials used
shall be steel, brass, bronze, aluminum, copper alloy or other
suitable material.
Note: At bearing velocities less than 60 m/sec. (200 ft/sec.), an
expander-compressor will typically use a babbited sleeve bearing. At
velocities above 90 m/sec. (300 ft/sec.), babbited pad type bearings
will typically be used. For speeds between these two values, the type
of bearing may be either sleeve or pad type, depending on such fac-
tors as speed, oil flow requirements, rotor dynamics, etc.
2.7.2.2 The bearing design shall suppress hydrodynamic
instabilities and provide sufficient damping over the entire
range of allowable bearing clearances to limit rotor vibration
to the maximum specified amplitudes (see 2.6.8.8 of Chapter 1
of this standard), while the equipment is operating loaded or
unloaded, including operation at any critical frequency within
the specified operating range.
2.7.2.3 Unless otherwise specified, hydrodynamic radial
bearings shall be fitted with bearing metal temperature sen-
sors installed in accordance with API Std 670.
2.7.3 Hydrodynamic Thrust Bearings
Hydrodynamic thrust bearings shall comply with the
requirements of 2.7.3 of Chapter 1 and the following
requirements:
2.7.3.1 Hydrodynamic thrust bearings shall be precision
machined, continuous or segmented face design. Continuous
face designs shall have grooving, such as spiral grooving, to
allow oil distribution. Segmented face designs may be either
fixed or tilting pad configuration. Materials used shall be
steel, bronze, aluminum, copper alloy or other materials suit-
able for the application. Thrust bearings shall be designed for
equal thrust capacity in both axial directions. Hydrodynamic
thrust bearings shall be arranged for continuous pressurized
lubrication to each side.
Note: A typical expander-compressor thrust bearing will be made of
brass or bronze, have a tapered land or spiral groove face design, and
be unbabbited.
2.7.3.2 Expander-compressors shall be equipped with
automatic thrust equalizing valves to reduce the bearing loads
for the specified conditions to a minimum, reducing expected
loads no more than 50% of the ultimate capacity of the bear-
ing (see Annex 4C).
Note: This device is normally a direct operated valve, using fluid
pressures taken from the thrust bearing oil film for actuation.
2.7.4 Bearing Housings
2.7.4.1 Bearing housings shall be in accordance with 2.7.4
of Chapter 1 of this standard and the following requirements:
2.7.4.2 Rotor support system parts (bearings, bearing
housings, bearing shells and bearing brackets) shall be sepa-
rable from the mating casings.
Note: Expander bearing housings are normally pressurized.
2.8 EXPANDER-COMPRESSOR SHAFT SEALS
2.8.1 General
Shaft seals shall comply with the requirement of 2.8 of
Chapter 1 of this standard and the following:
Note: Expander-compressors do not have shaft end seals, but the
same types of seals are used for internal sealing between the process
gas and the bearing housing.
2.8.1.1 Shaft seals shall be provided to restrict the leakage
of process gas into the bearing housing over the range of
specified operating conditions, including start-up and shut-
down. Seals shall be suitable for specified variations in seal
operating conditions that may prevail during start-up, shut-
down, or settling out, and during any other special operation
specified.
2.8.1.2 Shaft seals used in expanders may be either clear-
ance seals (see 2.8.2 of Chapter 1 of this standard) or self-act-
ing dry gas seals (see 2.8.4 of Chapter 1 of this standard).
2.9 GEARS
Gears are not applicable to expander-compressors.
l
l
COPYRIGHT 2002; American Petroleum Institute
Document provided by IHS Licensee=Shell Services International B.V./5924979112,
User=, 10/07/2002 18:49:21 MDT Questions or comments about this message: please
call the Document Policy Management Group at 1-800-451-1584.
-- | ||| | | | |||| || | |||| || | | | | ||| | |---