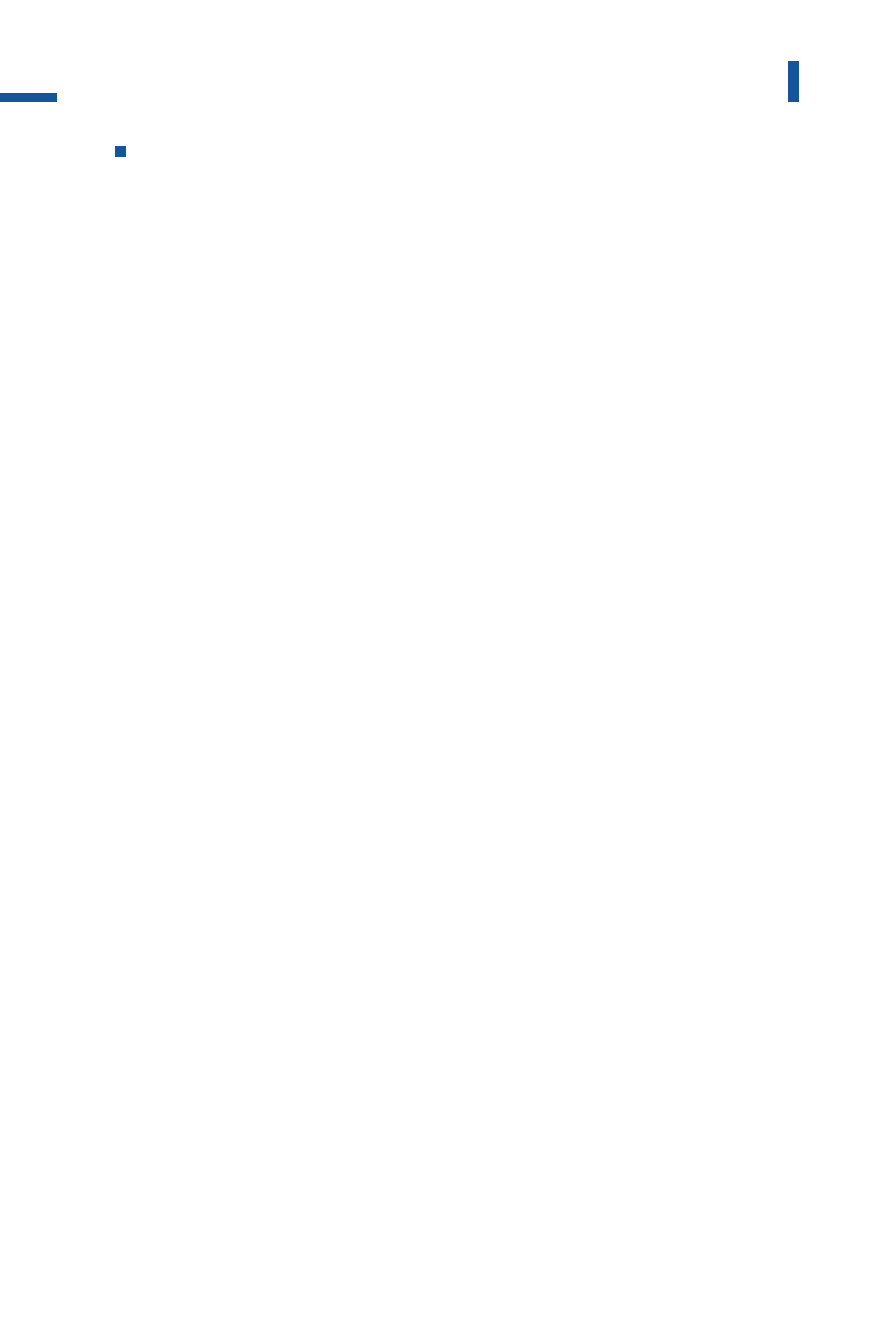
4.6.6Perforating presses
Perforated sheets are in widespread use in almost every sector of indus-
try: in the form of sieves and filters in the food industry, in mining and
gravel pits, as protective covers in the electrical industry, in building
machinery and machine tools, as partitions and for decorative purpos-
es, in household appliances, office furniture, aircraft and industrial con-
struction.
The number of punch contours and hole patterns is almost infinite.
Steel, NF metals or combinations are among the materials used, and sheet
thicknesses can range anywhere between 0.3 and 30mm. Perforated sheet
metal is manufactured either off the coil or in plate form. Basically, two
main methods are used: Continuous or periodically interrupted hole pat-
terns are manufactured in large series from coil or plate stock on all-across
perforating presses, while strip perforating presses are used for the small-
series production of optional hole patterns from plate material.
Both machine systems can be equipped with units for automatic
sheet metal feed, for removal of finished parts, notching, separating
and splitting, and with quick-action die changing devices, die monitor-
ing systems and sound enclosures.
All-across perforating presses
Sheet metal with continuous or periodically repeated hole patterns are
manufactured on all-across perforating presses (Fig.4.6.28).These
presses process both coil and plate stock up to a thickness of around
6mm. The sheet metal runs through the press only in the feed direction
and is normally perforated in a single working stroke over the entire
width. The nominal press force lies between 800 and 5,000kN, the
maximum material width between 1,000 and 1,600mm. Depending on
the press size and feed system, all-across perforating presses operate at
up to 800 strokes per minute.
The press frame is configured as a monobloc (Fig.4.6.29).The slide
runs in clearance-free hardened roller gibs (cf.Fig.3.1.6)via two columns,
and is driven by a DC or threephase control motor via a flywheel, eccen-
tric shaft and two connecting rods. This configuration guarantees a long
die life. Short switching times, short stroke lengths and high resistance to
wear are achieved through the use of a quick-action clutch-brake combi-
nation (cf.Fig.3.2.8).
314
Sheet metal forming and blanking
Metal Forming Handbook / Schuler (c) Springer-Verlag Berlin Heidelberg 1998