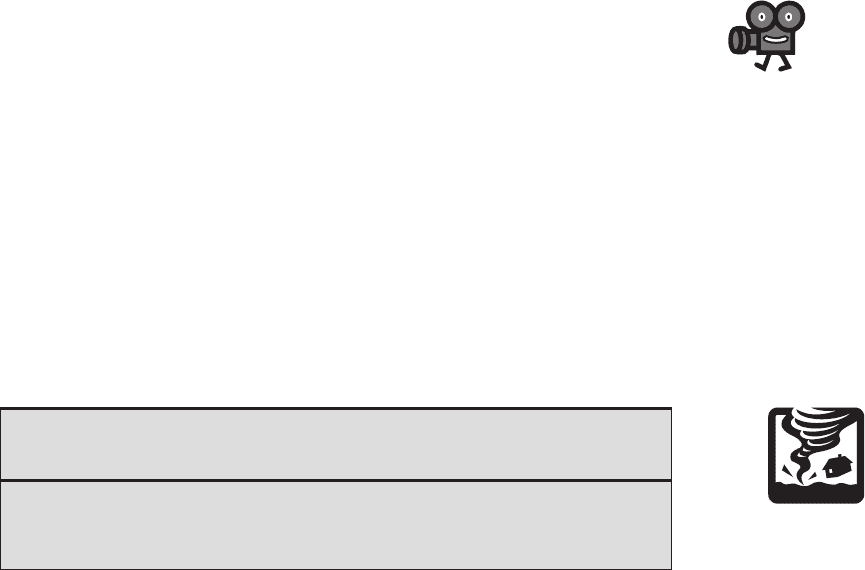
Confirming Pages
is a small air gap between the rotor and the stator where the magnetic fields interact.
In many DC motors, the rotor also includes a commutator that delivers and con-
trols the direction of current through the armature windings. For motors with a com-
mutator, “brushes” provide stationary electrical contact to the moving commutator
conducting segments. Brushes in early motors consisted of bristles of copper wire
flexed against the commutator, hence the term brush; but now they are usually made
of graphite, which provides a larger contact area and is self-lubricating. The brushes
are usually spring-loaded to ensure continual contact with the commutator. Video
Demo 10.11 shows a small, brushed, permanent-magnet DC motor disassembled so
you can see the various components and how they function.
A brushless DC motor has permanent magnets on the rotor and a rotating field
in the stator. The permanent magnets on the rotor eliminate the need for a commuta-
tor. Instead, the DC currents in the stator coils are switched in response to proximity
sensors that are triggered as the shaft rotates. Video Demos 10.12 and 10.13 show
two examples of brushless DC motors. One advantage of a brushless motor is that
it does not require maintenance to replace worn brushes. Also, because there are no
rotor windings or iron core, the rotor inertia is much smaller, sometimes making
control easier. There are also no rotor heat dissipation problems, because there are no
rotor windings and hence no I
2
R heating. Another advantage of not having brushes
is that there is no arcing associated with mechanical commutation. Therefore, brush-
less motors create less EMI and are more suitable in environments where explosive
gases might be present. One disadvantage of brushless motors is that they can cost
more due to the sensors and control circuitry required.
Figure 10.7 shows examples of commercially available assembled motors. In
the top figure, the motor on the left is an AC induction motor with a gearhead speed
reduction unit attached. The motor on the right is a two-phase stepper motor. Motors
come in standard sizes with standard mounting brackets, and they usually include
nameplates listing some of the motor’s specifications. The bottom figure shows the
internal construction of a permanent-magnet-rotor stepper motor. Video Demo 10.14
shows other examples of commercially available regular DC motors and stepper
motors.
Video Demo
10.11DC motor
components
10.12Brushless
DC motor from a
computer fan
10.13Brushless
DC motor gear
pump
10.14DC and
stepper motor
examples
■ CLASS DISCUSSION ITEM 10.2
Eddy Currents
Describe the causes of eddy currents that are induced in a conducting material expe-
riencing a changing magnetic field. The iron core in a motor rotor is usually lami-
nated. Explain why. What is the best orientation for the laminations?
Torque is produced by an electric motor through the interaction of either stator
fields and armature currents or stator fields and armature fields. We illustrate both
principles starting with the first. Figure 10.8 illustrates a DC motor with six armature
windings. The direction of current flow in the windings is illustrated in the figure.
10.4 Electric Motors 437
alc80237_ch10_431-477_sss.indd 437alc80237_ch10_431-477_sss.indd 437 10/01/11 10:24 PM10/01/11 10:24 PM