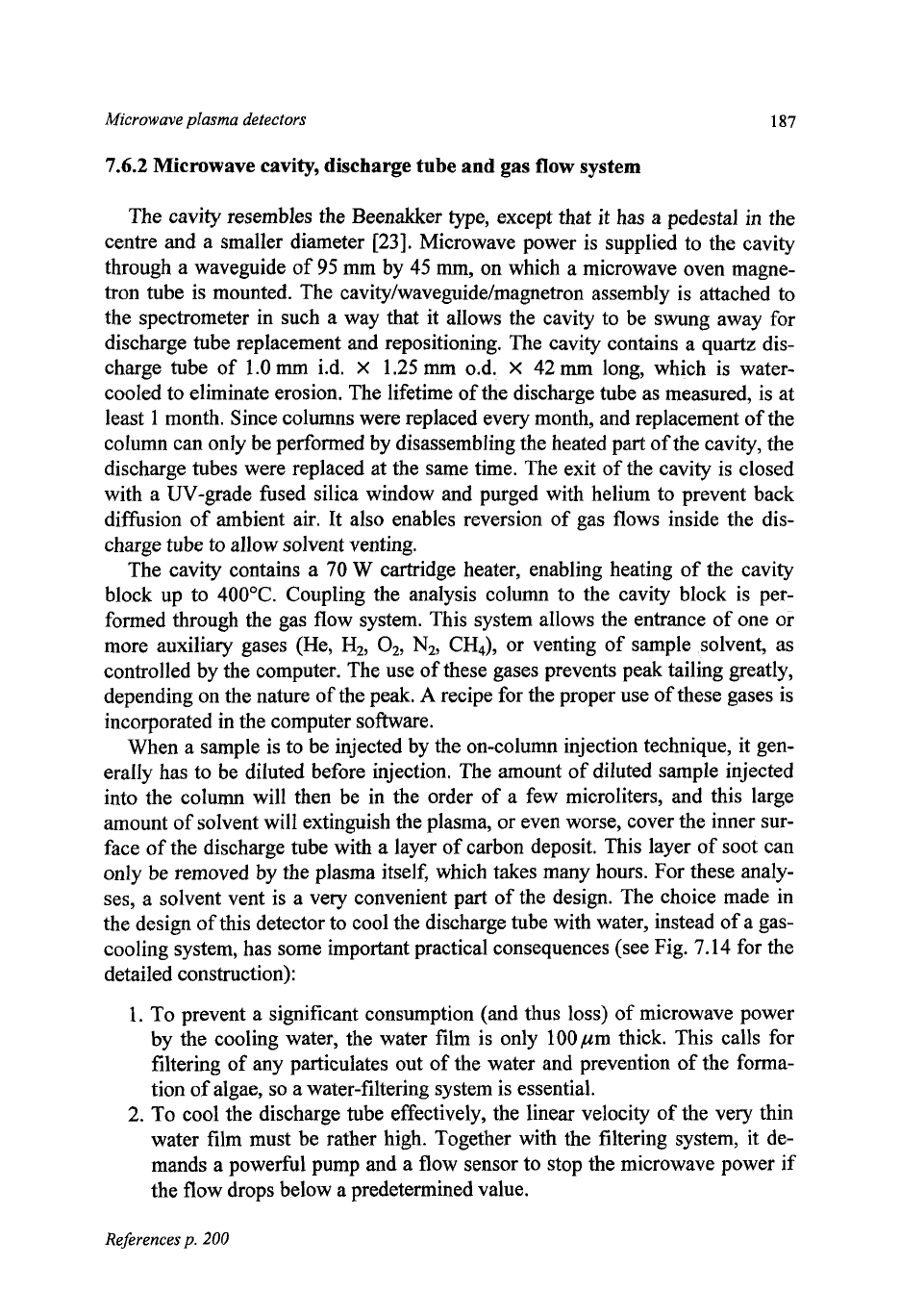
Microwave plasma detectors
187
7.6.2
Microwave cavity, discharge tube and gas flow system
The cavity resembles the Beenakker type, except that it has a pedestal in the
centre and a smaller diameter
[23].
Microwave power is supplied to the cavity
through a waveguide of
95
mm by
45
mm,
on which a microwave oven magne-
tron tube is mounted. The
cavity/waveguide/magnetron
assembly is attached to
the spectrometer in such a way that it allows the cavity to be swung away for
discharge tube replacement and repositioning. The cavity contains a quartz dis-
charge tube of
1.0
mm
i.d.
X
1.25
mm 0.d.
X
42
mm
long, which is water-
cooled to eliminate erosion. The lifetime of the discharge tube as measured, is at
least
1
month. Since columns were replaced every month, and replacement of the
column can only be performed by disassembling the heated part of the cavity, the
discharge tubes were replaced at the same time. The exit of the cavity is closed
with a UV-grade fused silica window and purged with helium to prevent back
diffusion of ambient air. It also enables reversion of gas flows inside the dis-
charge tube to allow solvent venting.
The cavity contains a
70
W
cartridge heater, enabling heating of the cavity
block up to 400°C. Coupling the analysis column to the cavity block is per-
formed through the gas flow system. This system allows the entrance of one or
more auxiliary gases (He,
H2,
02,
N2,
CH,),
or venting of sample solvent, as
controlled by the computer. The use of these gases prevents peak tailing greatly,
depending on the nature
of
the peak.
A
recipe for the proper use of these gases is
incorporated in the computer software.
When a sample is to be injected by the on-column injection technique, it gen-
erally has to be diluted before injection, The amount of diluted sample injected
into the column will then be in the order of a few microliters, and this large
amount of solvent will extinguish the plasma, or even worse, cover the inner sur-
face of the discharge tube with a layer of carbon deposit. This layer of soot can
only be removed by the plasma itself, which takes many hours. For these analy-
ses, a solvent vent is a very convenient part of the design. The choice made in
the design of this detector to cool the discharge tube with water, instead of a gas-
cooling system, has some important practical consequences (see Fig.
7.14
for the
detailed construction):
1.
To
prevent a significant consumption (and thus loss)
of
microwave power
by the cooling water, the water film is only 100,um thick. This calls
for
filtering of any particulates out of the water and prevention of the forma-
tion of algae,
so
a water-filtering system is essential.
2.
To
cool the discharge tube effectively, the linear velocity of the very thin
water film must be rather high. Together with the filtering system, it de-
mands a powerful pump and a flow sensor to stop the microwave power if
the flow drops below a predetermined value.
References
p.
200