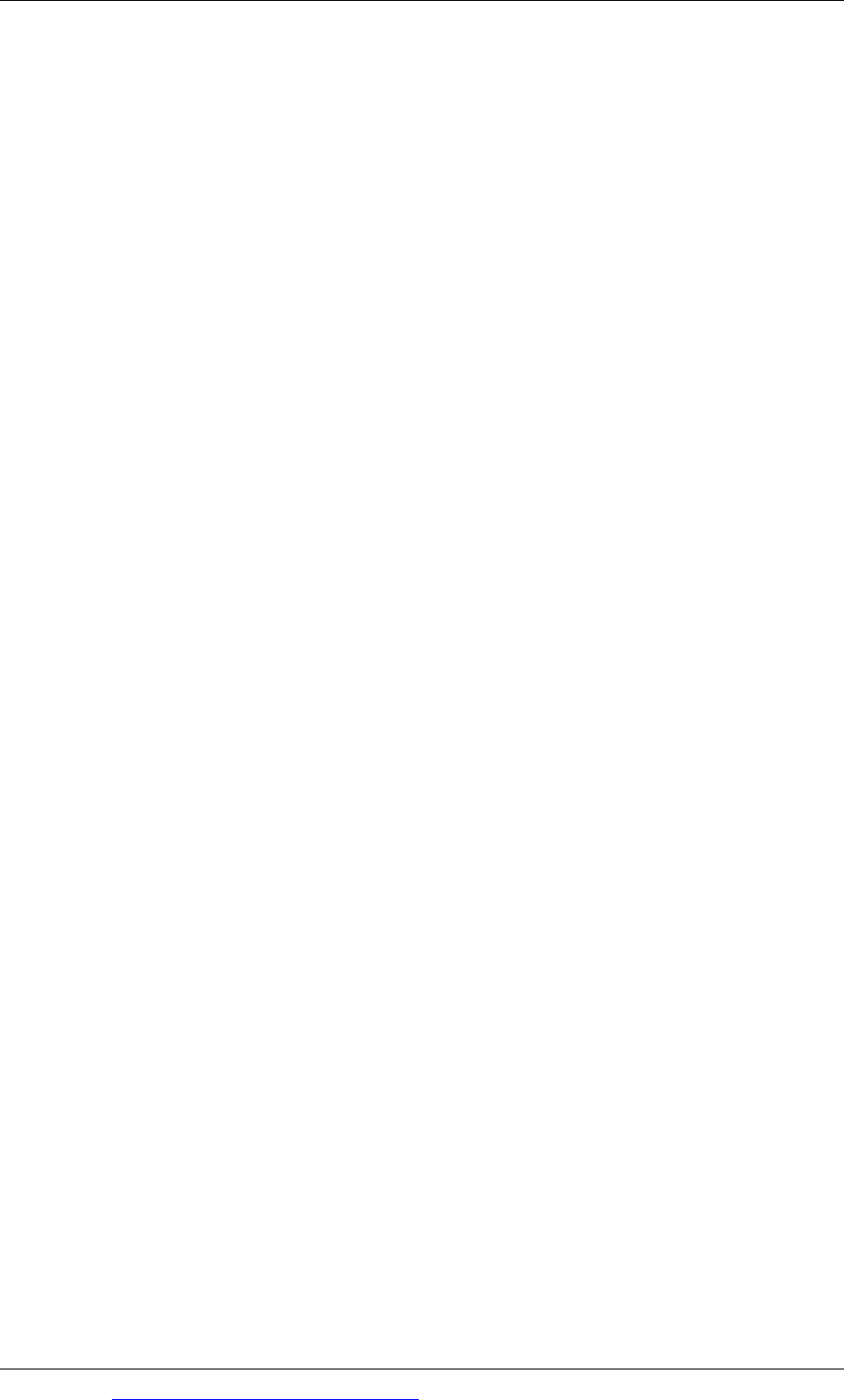
Paper P5: Advanced performance management
422 Go to www.emilewoolfpublishing.com for Q/As, Notes & Study Guides © EWP
Quality circles cannot replace other quality management processes and methods,
such as statistical quality control systems.
Quality circles are not used in all companies that use TQM. However, a system of
continuous improvement (Kaizen) does depend on work by teams of individuals
representing different functions and skills. For example, a team might be established
consisting of an engineer, an accountant, a person from manufacturing and a person
from the buying department. The team members then combine their knowledge and
skills to devise methods of achieving improvements in a particular aspect of
operations for which they have been given responsibility for improvement.
3.7 Potential benefits from TQM
There are several potential benefits that might be obtained from introducing a TQM
approach:
Formally establishing a TQM system will establish the importance of ‘quality’ in
a way that all employees and managers should recognise.
The commitment to quality should also establish ‘customer satisfaction’ as a
prime business objective.
A successful introduction of a TQM approach should result in continuous
improvements in all processes and operations.
However, the successful application of TQM will depend on the provision of
relevant and useful quality-related information, and in particular, information about
quality-related costs.
3.8 Performance measurement for TQM
A system of TQM and continuous improvement needs the support of an
information system that provides relevant information.
Management accounting information can be provided by the Kaizen costing
system.
There is extensive use of non-financial performance indicators, such as
production setup times, the number of times materials are moved, and the
number of units scrapped or wastage levels.
A report in the US (1993) on the use of Kaizen by Japanese manufacturing
companies commented: ‘These quantitative, non-financial measures allow
employees to monitor their performance and interpret the results of their efforts.
With relevant training and frequent reports on the company’s financial health,
companies ensure employees understand how their work directly affects the
company’s performance.’
3.9 TQM and JIT compared
Many of the concepts applied by total quality management are similar to those in a
just-in-time management philosophy.
The aim in both should be to have zero inventory. Raw materials should be
delivered from suppliers only when they are needed, and items should be