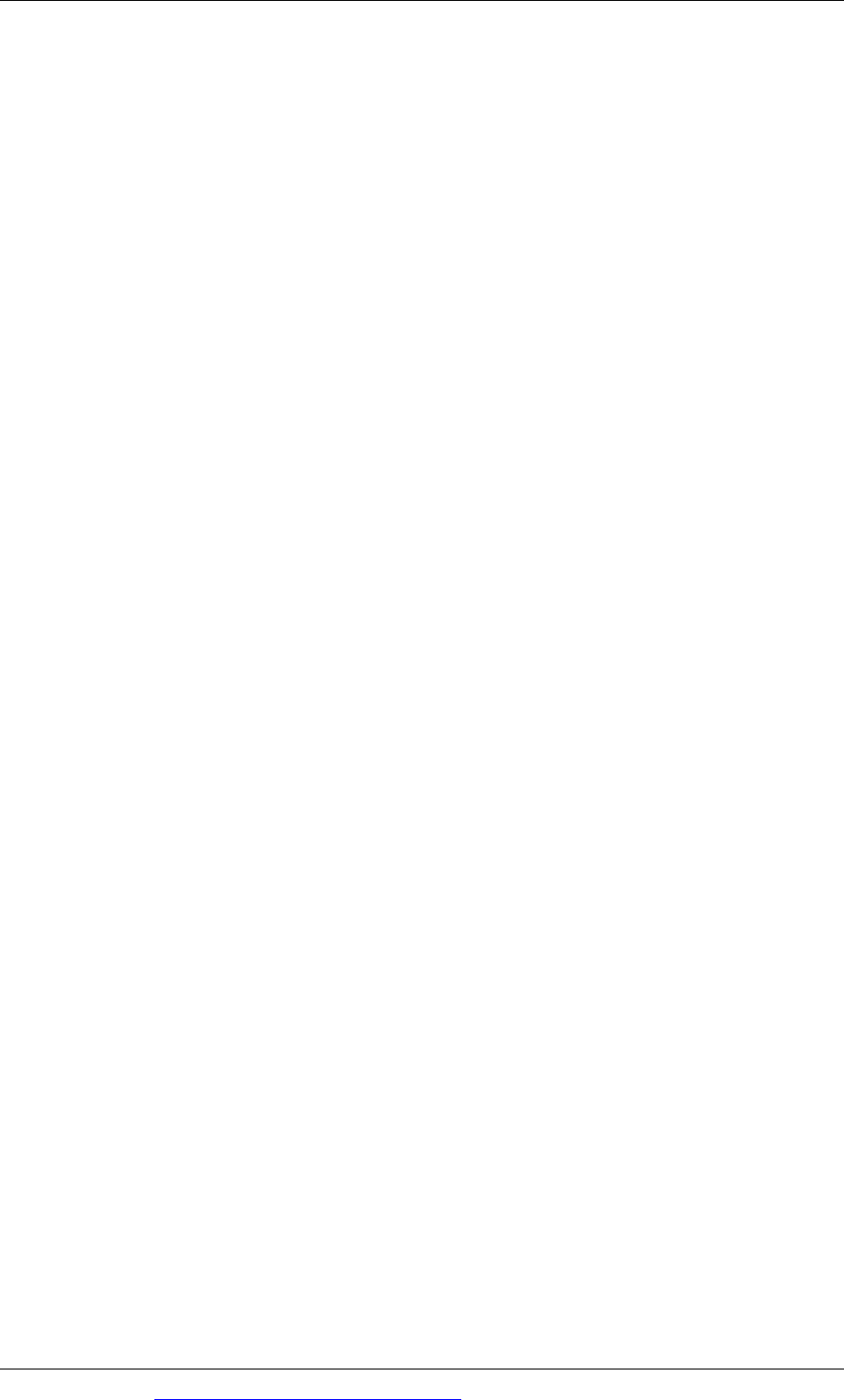
Chapter 13: Business strategy and quality initiatives
© EWP Go to www.emilewoolfpublishing.com for Q/As, Notes & Study Guides 337
2 A new philosophy. Companies outside Japan should adopt the new
philosophy of quality that Japanese manufacturers apply. Delays, mistakes
and defects in materials and workmanship that some companies consider
‘acceptable’ should not be tolerated.
3 Cease dependence on mass inspection to achieve quality. Quality should be
built into products and processes in the first place, so that defects do not
happen. It is inappropriate to rely on quality checks and inspections to
achieve target standards of output quality.
4 End lowest tender contracts. Companies should not always buy from the
supplier who quotes the lowest prices. The quality of supplied items is
important, and the purchasing decision should be based on factors other than
cost.
5 Improve every process. Every process should be improved. There should be a
continual search for ways of introducing further improvements into
processes. Improvements should never end.
6 Institute training on the job. On-the-job training should be used to improve
the skills levels of employees.
7 Institute leadership. Managers should provide leadership that helps
everyone to do their job better. Managements should be responsible for
quality, not just larger volumes of output.
8 Drive out fear. Two-way communications between manager s and employees
should be developed, so that communications are open and honest. This mans
driving out the fear of blame for making mistakes.
9 Break down barriers. The barriers between different functions and
departments within the entity should be removed. Individuals in different
functions and departments should learn to co-operate with each other,
working in teams where necessary to deal with problems that arise.
10 Eliminate exhortations. Management should eliminate the use of slogans that
urge individuals to do better. Slogans such as ‘Avoid waste!’ or ‘Keep on
doing better!’ are more likely to arouse hostility than obedience.
11 Eliminate arbitrary numerical targets. Quantifiable targets should not be
used of they are arbitrary. (Deming was a supporter of the concept of
statistical quality control, but this does not require arbitrary quality standards:
quality standards can be set objectively through statistical methods.)
12 Permit pride of workmanship. Employees should be given the opportunity to
take pride in their quality performance. This could mean avoiding reward
systems that reward employees for ‘good performance’, because ‘good
performance’ usually means a high volume of production or sales rather than
better quality.
13 Encourage education. Employees should be encouraged to improve their
education, because the knowledge built up within an entity is a way of
achieving competitive advantage.
14 Top management commitment and action. The success of quality
management initiatives depends on the total support and commitment of top
management.
Deming’s views can be applied to business strategy development, where quality is
considered an important strategic objective. Deming would have argued that in
order to achieve continuous quality impro
vements, it is essential to remain
committed to the objective of better quality, even if this means some loss of profits
and benefits in the short term.