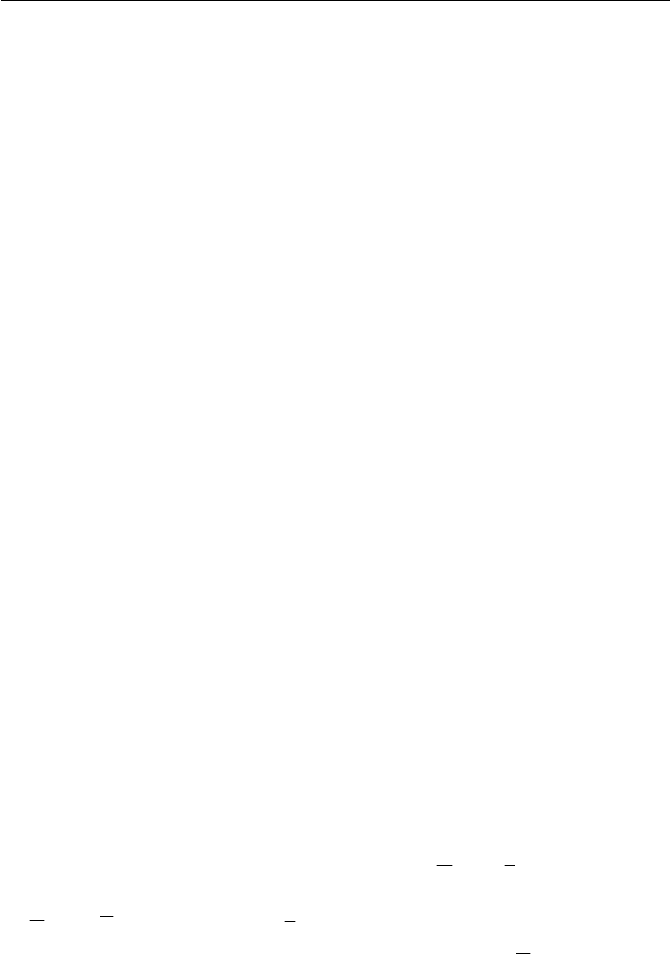
4.2 General Theories of Turbomachinery 189
and with a less contact surface area than with fluid flow. This is often en-
counters in axial flow turbomachines, where the flow to and from a turbo-
machine is in the axial direction of the rotation (shaft rotation), as illus-
trated in Fig. 4.37(a) and (b). In order to figure out the axial flow
turbomachine, (a) schematics of an axial flow pump and (b) an axial flow
turbine (Kaplan turbine) are displayed in Fig. 4.37. Usually in the actual
axial flow turbomachines, there are inlet guide vanes (which are not re-
garded as part of a control volume in the case of a pump. It usually func-
tions in directing flow away from the axial direction), rotor vanes (impeller
vane in pump and runner in turbine) and stationary guide vanes in pumps.
In axial flow turbomachines, a number of identical vanes, which are
equally spaced and paralleled to one another, are arranged so that they
form a cascade geometry. For the axial flow turbomachines of a high hub-
tip ratio, radial velocities are negligible and, to a close approximation, the
flow may be regarded as two dimensional. To obtain a truly two dimen-
sional flow, however, there would require a cascade of infinite extent so
that there would not be any flow interaction between each neighboring
vane. In Fig. 4.38(a), the control volume of an impeller vane is illustrated,
and with it the energy input through the shaft rotation is converted into
flow energy.
The flow approaches the cascade, as illustrates in Fig. 4.38(b), with an
absolute velocity
1
c at an angle
1
and leaves downstream of the cascade
with the absolute velocity
2
c
at an angle
2
. It is denoted that in the fol-
lowing analysis the flow is assumed to be incompressible
30.
M
and
steady in the control volume with the rotational speed
u . The assumption
of the steady flow is valid for an isolated cascade, where for the control
volume the number of vanes is low. The velocity diagrams at the inlet and
the outlet can be composed as shown in Fig. 4.38(b). The absolute veloci-
ties
1
c and
2
c are obtained by the vector sum of the rotational speed u
and the relative velocity w at the inlet and outlet respectively. In the airfoil
theory, approaching the axial flow turbomachines, the averaged velocities
to a representative airfoil are composed by taking the averaged velocity
diagram with reference to Fig. 4.38(c), where
w and c are the average
relative velocity and absolute velocity respectively with the average angle
is
and
E
. In Fig. 4.38(c), c is composed with u and the arithmetic
mean of
1
w
and
2
w
, whose circumferential component is
2
21 uu
www
.