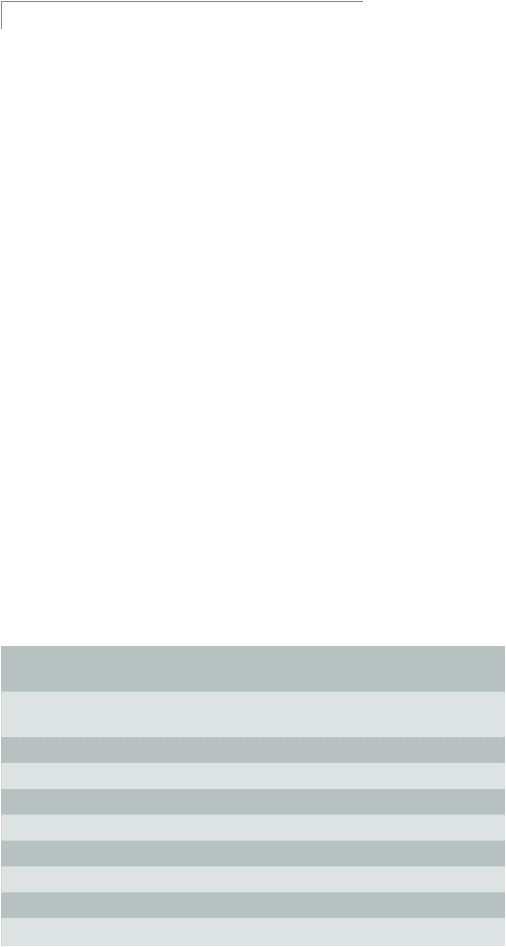
32 NOVEMBER 2010 INTERNATIONAL WATER POWER & DAM CONSTRUCTION
OPERATION AND MAINTENANCE
the entire weight of rotating parts and the hydraulic thrust on
the runner were supported by the turbine head cover, and would,
therefore, resist most, if not all of the hydraulic uplift. This is
conrmed by the photographs. [15, 5 through 8]
The stud fatigue failure was attributed to the large vibration which
had plagued Unit 2 for a very long time, both before and after the
refurbishment in the rst quarter of 2009. It appears that the runner
repairs that year were made in place, without removal of the head
cover, so the studs would not have been replaced. [10, 14]
The Unit 2 operating zones were dened in the report as acceptable
between 0 and 265MW (Zone 1), unacceptable between 265 and
570MW (Zone 2), acceptable between 570 and 640MW (Zone 3),
and prohibited above 640MW (Zone 4). The loads carried during
the nine hours leading up to the failure indicate that the rough zone
(Zone 2) was transited by the machine several times, and it was in
that zone at the time of the load rejection and failure. [10]
The report contains several interesting facts taken from logs and
automatic recording equipment. It notes that the Unit 2 load changed
12 times between midnight and 0230 on 17 August, and the range of
total plant load was 2800 to 4415 MW. Unit 2 was known to have
passed through its rough operating zones some six times in the few
hours preceding the failure. (10)
Some sample times and Unit 2 loads before and after midnight on
16-17 August (10) are shown in the table below:
At the time of the load rejection and failure, the load on Unit 2
was apparently being reduced. At 0800, Unit 2 was reported to be
carrying a 605 MW load, with a turbine owrate of 312m
3
/sec and a
gate setting of 72.5%. At 0813, Unit 2 was carrying 475MW, with a
ow of 256m
3
/sec at an opening of 69%. Twenty-ve seconds later,
the load was recorded as zero, indicating a sudden load rejection from
475MW. It should be noted that the load at 0813 was in the middle
of Zone 2, and considerable vibration should have been occurring,
based on previous experience with the machine. [10]
WHAT COULD HAVE CAUSED THIS ACCIDENT?
Early hypotheses
An early analysis [1] that was distributed via the internet only a week
after the accident postulated causes for the Unit 2 failure including
ingestion of debris and a broken governor oil pipe. The failures of
Units 7 and 9 were attributed to runaway of the units under ooded
conditions. As photographic evidence subsequently showed (Figures
10, 11, and 12), these explanations are not consistent with the events
that have been shown to have occurred.
Another early hypothesis was that one of the draft tube piers col-
lapsed causing a blockage of the draft tube. This seemed not to be
credible at the outset, and the Rostekhnadzor report makes no men-
tion of such a scenario, which would have left a clear set of evidence,
had it occurred.
An early hypothesis by a Russian engineer and hydraulic turbine
specialist, B. Kolesnikov [21], was that the accident was caused by the
seizure of either the turbine bearing or the upper runner seals causing
a very large twisting force to be transmitted to the head cover. The
fact that the studs were not sheared off eliminates this possibility, as
was pointed out by B. Kolesnikov in a later note written after addi-
tional photographs became available.
Hypotheses by Rostekhnadzor and a later writer
Rostekhnadzor attributed the accident to fatigue failure of the head
cover studs caused by the heavy vibrations that had plagued Unit 2
over considerable time.
An October 2009 presentation by E. Kolesnikov [19] expanded on
the Rostekhnadzor conclusions somewhat. He similarly attributed
the failure of Unit 2 to the fatigue failure of the head cover studs due
to the severe vibration the machine was experiencing, and he pointed
out that the vibration monitoring equipment on the unit was out
of service at the time of the failure. Neither he nor Rosteknadzor
alluded to a source of the large upward force necessary to lift the
machine, however. He did not attribute the failure to a load rejection
situation, implying that the failure occurred during an operating load
change. This does not seem likely, since, during even part load opera-
tion, there is a very signicant hydraulic down thrust exerted on the
runner (estimated to be of the order of 7500 tonnes) that is resisted
by the thrust bearing, which, in turn, is supported on the head cover.
This, combined with the weight of the parts supported by the thrust
bearing, would have left no load to be carried by the studs.
B. Kolesnikov (21) hypothesized early that the event may have been
caused due to a seizure of the turbine bearing or the upper runner
seals causing a large torsional load on the head cover, but he later
rejected these ideas since, as shown in the photographs in Figure 13,
the studs failed in tension; not in shear.
DISCUSSION AND A NEW HYPOTHESIS
Unit 2 essentially exploded. The fatigue failure of the head cover studs
during operation of the machine, as suggested by Rostekhnadzor
and E. Kolesnikov, does not lead to a source for the enormous and
sudden upward force necessary to achieve this violent explosion.
That upward force caused runner, shaft, head cover, wicket gate
upper trunnions and operating arms, both bearings, the generator
rotor, and all associated structure of Unit 2 to be forced upward with
enough violence to crush the rotor spider and destroy the stator. It
had to be triggered by something that occurred suddenly and vio-
lently (Figures 7, 8, and 9).
Although the compromised condition of the head cover studs cer-
tainly contributed to the failure of Unit 2, stud fatigue failure alone
seems very unlikely to have occurred in all three failed units (Units 2,
7 and 9) at the same time. In the absence of any stud failure at Units 7
and 9, it is very difcult to envision what could have caused the damage
that is clearly visible in the photographs (Figures 10, 11, and 12). Thus,
it is likely that the studs of Units 7 and 9 did fail, but their failure was
caused by an upward force on the head cover of each unit.
Each rotor weighed 920 tonnes. Each runner weighed 156 tonnes.
The entire assembly as supported by the thrust bearing weighed about
1500 tonnes, not including the downward hydraulic thrust on the
runner or the resistance of the various mechanical connections associ-
ated with the gate trunnions and any generator guide bearing lateral
supports. [1, 9, 10] Each head cover was exposed to draft tube head,
plus a contribution from penstock head, which was exerted on the head
cover annulus outside of the upper runner seal, and particularly that
part outside the wicket gate trunnion circle (Figure 6). [15] This could
have provided enough upward force to lift the cover during a full shut
down if the studs were truly so weak as to contribute little or nothing
to the resistance to upward load, the down thrust on the runner had
become negligible at full ow stoppage, and no signicant resistance
was exerted by trunnion connections or any connections of the gen-
erator guide bearing to its lateral bracing. The tables and diagrams
in the Rostekhnadzor report suggest that the static tailwater load on
the head cover at the time would have been about 10m. [10] This is
equivalent to about 350 tonnes of upward force on the gross area of the
head cover inside the runner seal ring under static conditions; however,
during operation, and particularly during a load reduction, this upward
load would have been reduced substantially due to the effects of the
Sample times
Time Load (MW) Time Load (MW)
2315 50 0730 170
2317 110 0730 to 0745 170 to 260
2330 200 0746 610
2331 165 0747 to 0800 605
2344 to 0015 600 0812 575
0030 135 0813 475
0030 to 0703 10 to 255 0813 25secs 0
0703 to 0729 600