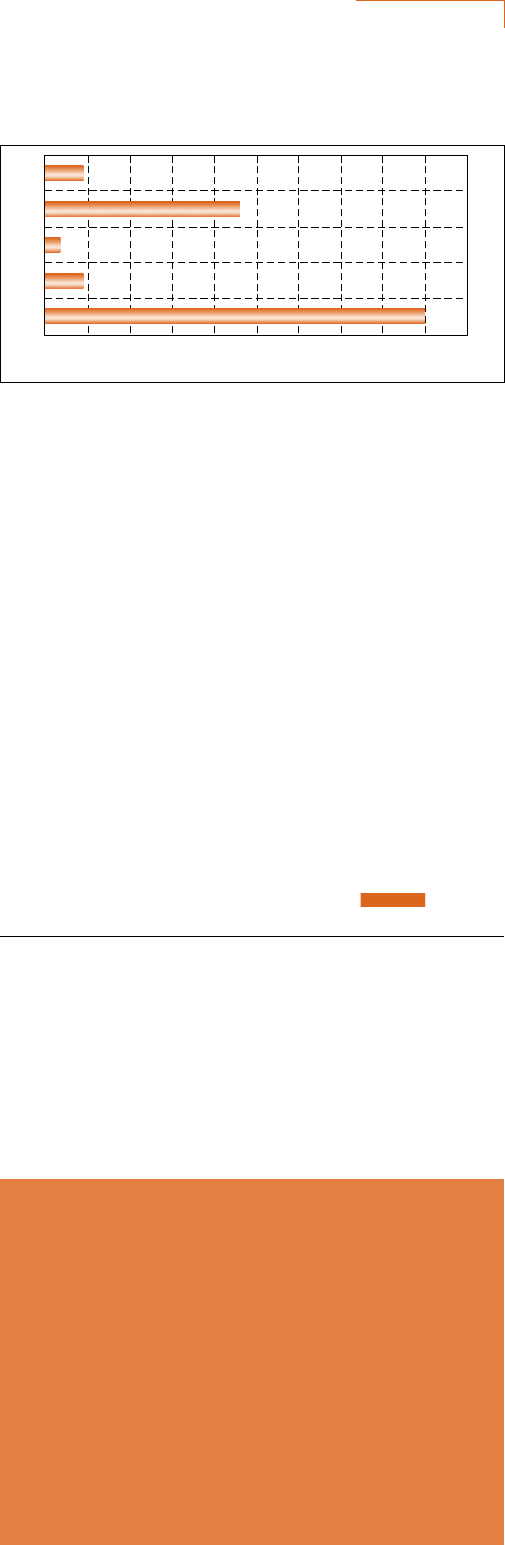
WWW.WATERPOWERMAGAZINE.COM APRIL 2010 37
TUNNELLING
measures will include grouting and icing of soft grounds. To evaluate
the effect of surface subsidence, extensometer grid systems in combina-
tion with a groundwater monitoring system will be installed.
CONVERG ENCE MEASU RE MENTS
During excavation of the tunnel, convergence measurements have been
taken and monitoring of deformation to the excavation chamber was
undertaken. Deformation of the excavation chamber is a result of stress
redistribution leading to increased stress in some parts and a reduction
of stress in other areas. Monitoring of this redistribution is necessary to
ensure stability of the construction. Convergence monitoring includes
in-situ measurements of the excavation chamber, but can sometimes
also require surface levelling and the use of surface installations such as
extensometer and inclinometer units along the axis of the tunnel.
Arrangement and installation – A standard cross-section for correct
data acquisition has been defined for the levelling of the crown and
sidewalls to monitor and record deformations. The distance between
the single convergence measurement stations must be under 10m.
Additional installation of pressure cells in the seam between rock
and shotcrete was also recommended to evaluate rock pressure. An
additional radial load cell to measure the concrete pressure was also
recommended every 50m. A standard cross-section for convergence
measurements must be comprised of at least five reading points to
ensure complete data acquisition of the crown, the sides and the base
of the tunnel cross section (Figure 8). The installation of the reading
points must be carried out directly after the installation of the support
so as to capture the initial deformation. An early reference measure-
ment must be carried out to assess the later data.
Interval of measurements – The time of the reference measurements
has been documented on the Poubara project. The following conver-
gence measurements are carried out quickly and must be executed on
a daily basis until the deformation has settled to an acceptable level.
The level of tolerance is dependent on the behaviour of the rock mass.
Deformations of 5 to 10cm are already critical for a brittle rock mass
and might be enough to produce a rock failure while deformations up
to 15cm in a ductile rock mass are still non-critical. An evaluation of
the fracture behaviour must be assessed to define a tolerable limit of
deformation. Once deformation is assessed to be below the tolerance
level, convergence measurements can be carried out on a weekly or
monthly basis. The time taken for one standard cross-section conver-
gent measurement is typically 10 minutes.
ESTIMAT IN G THE TUN NE LLING CO NS TRUCTIO N TIME
General – The main parameters guiding an estimation of tunnelling
progress include the available work force (teams, shifts), the machinery
and the maximum size of the construction site and its access routes.
The normal construction method is from one side only and represents
the slowest mode of excavation. The fastest progress can be made by
adopting simultaneous excavation from multiple tunnel endings. The
geological conditions in the project area favour a two- sided or even a
simultaneous excavation from three sides. The main parameter used for
the estimation of tunnelling progress is the weekly excavation progress.
This parameter was set at 21, 28 and 35m per week corresponding to
a daily progress of 3, 4 and 5m.
Construction time estimations – Excavation with one heading face
Daily progress is estimated using the parameters of work force and
machinery available for the main tunnelling construction. A constant
progress of 3, 4 and 5m per day is expected.
This constant progress can be achieved by two to three shifts per day,
with eight to ten hours per shift. The main tunnelling works include the
drilling and loading of blasts, scaling of loose material after blasting,
mucking, installation of ventilation and drainage units, and the installa-
tion of rock supports. The time for completion of the main excavation
works for this single sided excavation ranges from 2.52 (3m/day), 1.89
(4m/day) and 1.51 (5m/day) years depending on the daily progress.
Excavation with two heading faces – The time required for tunnelling
can be shortened substantially by a simultaneous excavation using
two heading faces. The following estimations were made by adopting
the same parameters mentioned above. Excavations using two portals
can yield time-savings of approximately 50 per cent. The two head-
ing faces are situated at the two tunnel endings with equal sections of
approximately 1600 m. The time for completion of the main excava-
tion works for the two sided excavation ranges from 1.46 years (3m/
day), 1.09 years (4m/day) and 0.87 years (5m/day).
Excavation with three heading faces – The fastest completion of the
tunnel can be achieved by a three-sided excavation. This involves
an intensive planning of the construction site taking into account
an economic evaluation of the available workforce, machinery and
access routes. Two portals are located at the end of tunnel and one
additional heading can be installed at the fault, 1800 m from the dam.
Each section consists of equal parts of 900 m. Time for completion
of the main excavation works for the three sided excavation ranges
from 1.05 year (3m/day), 0.84 year (4m/day) and 0.67 year (5m/day)
for each heading operation.
Estimation of quantities – Finally, Figure 10 provides estimations of
the consumption of different support materials.
Cesar Adolfo Alvarado-Ancieta (Peru), Civil Engineer,
Dipl.- Ing., M. Sc., Director of Project, Head Hydropower
Uwe Wackwitz, Maximiliam Riehl (Germany), Dipl.-
Geologists, GAUFF GmbH & Co. Engineering KG,
Patrick Yalis Ongalla (Gabon), Ing. Electrical - Deputy
Coordinator / Resident Engineer, Direction Générale de
l’Energie et des Ressources Hydrauliques, Republic of
Gabon, Franceville
IWP& DC
References
Hoek, E. and Brown, E.T. (1997): Practical estimates of rock mass strength. - Int.
J. Rock Mech. & Mining Sci & Geomechanic Absracts, Vol. 34(8), pp. 1165-1186.
Bieniawski, Z.T. (1989): Engineering rock mass classifications. - New York: Wiley.
Petterson, S-A, Molin, Hans (1999): Grouting & Drilling for Grouting. Purpose,
application, methods and equipment with emphasis on dam and tunnel projects -
Atlas Copco.
Palmström, A (2000): Recent developments in rock support estimates by the
RMI. - in: Journal of Rock Mechanics and Tunneling Technology, Vol. 6, No. 1, pp
1 - 19; ISRMTT.
Palmström, A. (1995): RMi - a rock mass characterization system for rock
engineering purposes. - Dissertation at the Departement of Geology, Faculty of
Mathematics and Natural Sciences, University of Oslo.
Norwegian rock and soil engineering association (2000): Engineering Geology and
Rock Engineering, Handbook No. 2. - Oslo: NRSEA.
U.S. Army Corps of Engineers (1997): Tunnels and shafts in rock, engineering and
design. - Engineer Manual No. 1110-2-2901; Washington, DC: USACE.
Rock bolts
0 1000 2000 3000 4000 5000
Shot-
crete
Mesh wire
Steel archbase lock
Steel arch
Shotcrete = [m
3
] / Other[t]
Material(s)
Figure 10 – Estimation for total material consumption: shotcrete, rock bolts,
mesh wire, steel arch and steel arch base lock