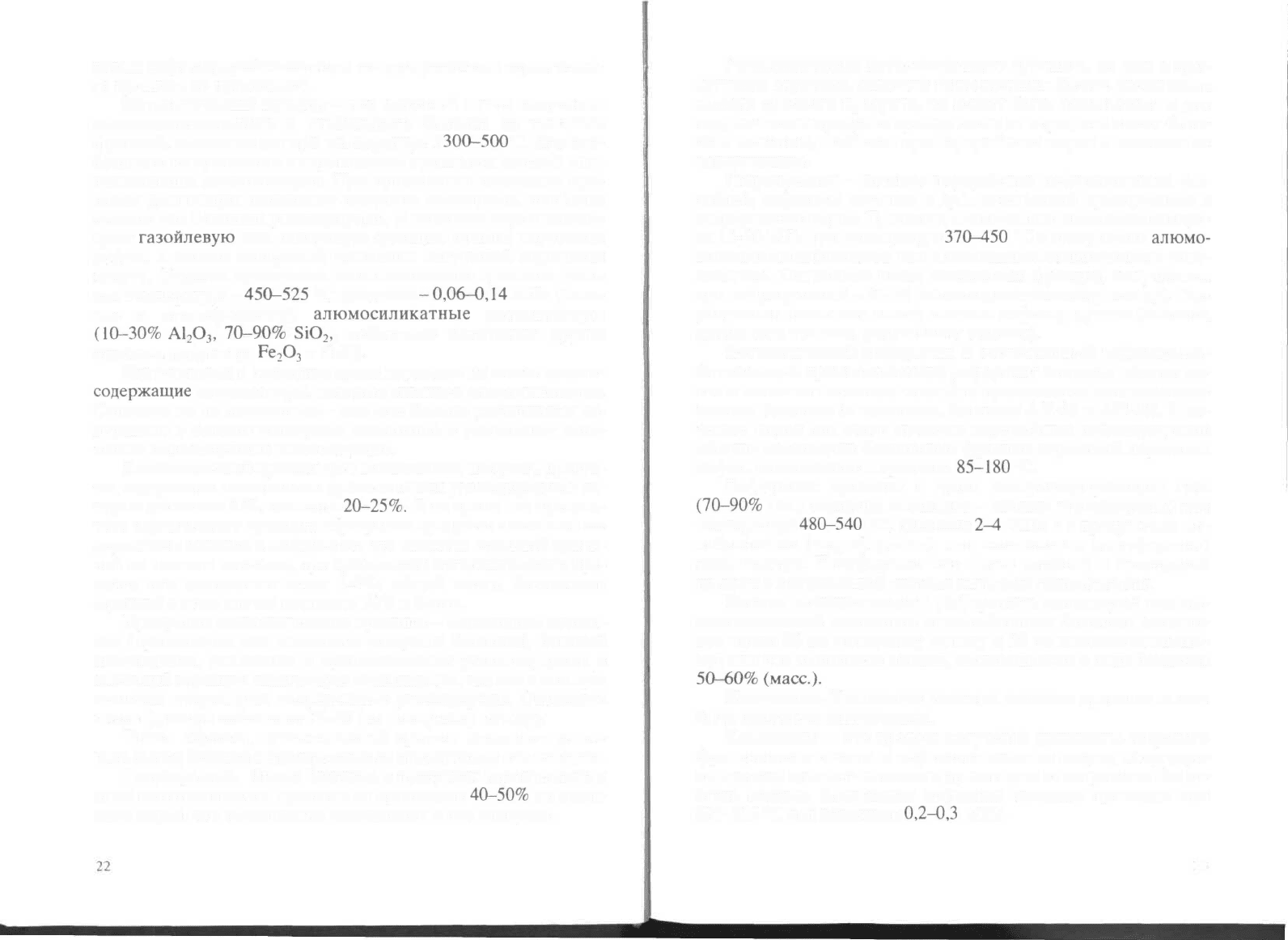
новых нефтеперерабатывающих заводах установки термическо-
го крекинга не применяют).
Каталитический крекинг - это основной метод получения
высококачественного и стабильного бензина из тяжелых
фракций, выкипающих при температуре
300-500
°С. Его осо-
бенность по сравнению с термическим крекингом состоит в ис-
пользовании катализаторов. При применении последних про-
цессы деструкции позволяют получить изомерные, наиболее
ценные для бензинов углеводороды. В качестве сырья исполь-
зуют
газойлевую
или соляровую фракции прямой перегонки
нефти, а иногда соляровый дистиллят вакуумной перегонки
мазута. Условия проведения каталитического крекинга тако-
вы:
температура
-
450-525
°С,
давление
-0,06-0,14
МПа
(близ-
кое к атмосферному),
алюмосиликатные
катализаторы
(10-30%
А1
2
О
3
,
70-90%
SiO
2
,
небольшое количество других
окислов, например,
Fe
2
O
3
и СаО).
Ряд установок в последнее время переводят на новые цеолит-
содержащие
катализаторы, которые активнее алюмосиликатов.
Основное же их достоинство - они еще больше увеличивают со-
держание в бензине изомерных соединений и уменьшают коли-
чество ненасыщенных углеводородов.
Каталитический крекинг дает возможность получать продук-
ты, содержание изоалканов и ароматических углеводородов в ко-
торых достигает 55%, цикланов
20-25%.
В то время как в резуль-
тате термического крекинга образуются продукты с высоким со-
держанием алкенов и алкадиенов, что является основной причи-
ной их низкого качества, при применении каталитического кре-
кинга они составляют всего 5-9%; общий выход бензиновых
фракций в этом случае достигает 50% и более.
Продукция каталитического крекинга - бензиновый дистил-
лят (применяется как компонент товарных бензинов), богатый
изоалканами, цикланами и ароматическими углеводородами и
имеющий хорошую химическую стабильность, так как в нем пра-
ктически отсутствуют непредельные углеводороды. Октановое
число фракции составляет 78-85 (по моторному методу).
Таким образом, каталитический крекинг позволяет увели-
чить выход бензина с одновременным повышением его качества.
Гидрокрекинг. Выход бензинов в продуктах термического и
даже каталитического крекинга не превышает
40-50%
от исход-
ного сырья, что обусловлено недостатком в них водорода.
Разновидностью каталитического крекинга, но уже в при-
сутствии водорода, является гидрокрекинг. Кроме увеличения
выхода целевого продукта, он может быть использован и для
гидроочистки продукта прежде всего от серы, что имеет боль-
шое значение, особенно при переработке сырья с высоким ее
содержанием.
Гидрокрекинг - процесс переработки нефтепродуктов (га-
зойлей, нефтяных остатков и др.), сочетающий крекирование и
гидрирование сырья. Процесс проводится под давлением водоро-
да 15-20 МПа при температуре
370-450
°С в присутствии
алюмо-
кобальтомолибденового или алюмоникельмолибденового ката-
лизатора. Октановые числа бензиновых фракций, получаемых
при гидрокрекинге - 85-88 (по исследовательскому методу). Гид-
рокрекинг повышает выход светлых нефтепродуктов (бензина,
дизельного топлива, реактивного топлива).
Каталитический риформинг. В отечественной нефтеперера-
батывающей промышленности риформинг занимает важное ме-
сто и является основным способом производства высококачест-
венных бензинов (в частности, бензинов АИ-93 и АИ-98). В ка-
честве сырья для этого процесса переработки нефтепродуктов
обычно используют бензиновые фракции первичной перегонки
нефти, выкипающие в пределах
85-180
°С.
Риформинг проводят в среде водородсодержащего газа
(70-90%
(об.) водорода остальное - низшие углеводороды) при
температуре
480-540
°С, давлении
2-4
МПа и в присутствии мо-
либденового (гидроформинг), или платинового (платформинг)
катализатора. Платформинг как более удобный и безопасный
процесс в значительной степени вытеснил гидроформинг.
Бензин каталитического риформинга используют как вы-
сокооктановый компонент автомобильных бензинов (октано-
вое число 85 по моторному методу и 95 по исследовательско-
му) или для выделения аренов, составляющих в этих бензинах
50-60%
(масс.).
Коксование. Утилизация тяжелых остатков крекинга может
быть проведена коксованием.
Коксование - это процесс получения дистиллята широкого
фракционного состава и нефтяного кокса из мазута, полугудро-
на, гудрона крекинг-остатков и др. методом их нагревания без до-
ступа воздуха. Коксование нефтяных остатков протекает при
505-515 °С под давлением
0,2-0,3
МПа.
23