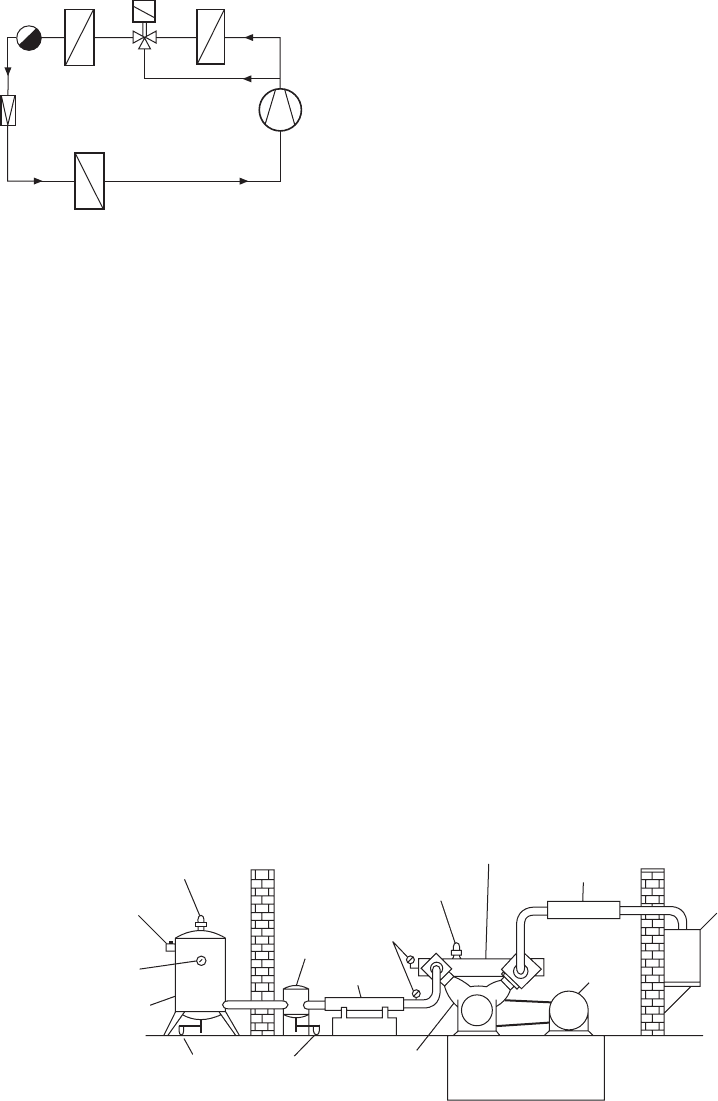
Engineering diagrams 235
The two condensers in the system illustrated are
connected in series. The heat recovery condenser (5)
can be switched off completely in summer. In winter,
spring and autumn it is used to pre-heat the outside in
accordance with demand.
Figure 27.22 shows a simplified schematic of the
refrigeration cycle.
be approximately equal to 30 times the rated free air
delivery of the compressor in dm
3
/s. Thus, a compressor
rated at 50 dm
3
/s free air delivery requires a receiver
of approximately 1500 litres capacity.
Compressed air in any normal supply mains contains
contaminants which need to be either completely or
partially removed depending on the ultimate use of
the compressed air. Naturally, the cleaner the air has
to be the greater the expense. The contaminants are:
(a) water in liquid and vapour form;
(b) oil which can exist in three forms, oil/water
emulsions, minute droplets suspended in the air as
an aerosol and oil vapours;
(c) atmospheric dirt particles and solid particles formed
by the heat of compression.
Having considered the types of contaminant present in
an air system, one can decide upon the degree of
cleanliness needed for any particular process and the
means required to obtain this. These include After-
coolers, Receivers, Air line filters, Air dryers, Coalescing
filters, Vapour adsorbers and Ultra high efficiency dirt
filters. Each application must be considered on its merits.
Figure 27.24 shows a typical air line installation for a
factory. Further cooling may occur in the distribution
mains themselves; these should be installed with a
pitch in the direction of the air flow, so that both gravity
and air flow will carry water to drain legs at appropriate
intervals. These legs should be fitted with automatic
drain valves. Note that take-off points are connected
to the top of the distribution mains to prevent water
entering the take-off lines.
The quality of air required for plant use will now
dictate which accessories are to be fitted at each take
off point. These range from a selection of filters and
pressure regulators; and if lubrication is required in
air actuated components, then lubricant can be metered
and atomized in the air line in the form of a fine fog to
coat all operating parts with a thin protective film. The
equipment is lubricated automatically through its
operating cycle.
Regular maintenance will ensure trouble-free
production facilities.
Industrial processes include: air agitation, air
bearings, air conveying of foodstuffs and powders, air
3
+
6
3
2
1
1
+
5
4
2
–
Key
1 Control valve 4 Compressor
2 Expansion valve 5 Heat recovery condenser
3 Evaporator 6 Outside condenser
Fig. 27.22 Refrigeration cycle of the shopping complex (simplified)
The authors wish to express their thanks for the
assistance given and permission to include examples
of applications engineered by Staefa Control System
Ltd, Hawthorne Road, Staines, Middlesex.
Pneumatic systems
Pneumatic systems require a supply of clean compressed
air to motivate cylinders, tools, valve gear, instruments,
delicate air controls and other equipment. Most factory
and plant installations operate between 5.5 and 7 bar.
A typical compressor installation is shown in Fig.
27.23.
Compressors are sized according to the amount of
free air delivered. Air flow is measured in cubic
decimetres per second (dm
3
/s) at standard atmospheric
conditions of 1013 mbar and 20°C as specified in ISO
554. The compressed air is stored in an air receiver
and, for a system operating at pressures in the region
of 7 bar gauge, the size of the receiver in litres should
Fig. 27.23
Automatic drain
valves
Two stage
double acting
air compresser
Motor
Air intake
filter
Air silencer
Intercooler
Relief
valve
Pressure
gauges
Aftercooler
Moisture
separator
Pressure
gauge
Air receiver
Stop valve
Safety
valve