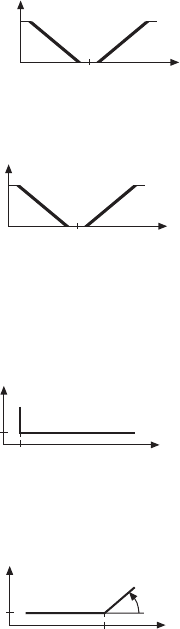
Engineering diagrams 229
Building management
Figure 27.8 and 27.9 show possible schemes for partial
and full air conditioning. In addition to the controls
indicated there will be all the associated ductwork,
filters, water, steam and electrical services. An electrical
control panel is usually necessary for the wiring of
interconnected equipment, instrumentation, and to
isolate plant for servicing. Although operations are
generally fully automatic, emergency hand control
facilities are often specified.
In an industrial situation where many departments
exist under the one roof, a central building management
system is necessary if the Plant Engineer requires to
know what is happening in the installation at any time.
Figure 27.10 shows a diagrammatic arrangement of
a building management system with software designed
specifically for the installation. Control is from a
standard IBM compatible PC(1), see Fig. 27.11.
The operator can check how any of the peripheral
components (4) are working. Control units for major
items of equipment such as boilers, fans, etc. are shown
as item (3). Individual room controllers (5) control
energy consumption as a function of room occupacy,
the time of day and season. System controllers (2)
coordinate process control tasks such as the overall
management of energy.
The Plant Manager has instant access to data using
a mouse operation and pull down menus. Individual
schematic diagrams can be displayed. Recorded data
over a period of time can be displayed or printed out.
The psychrometric chart (Fig. 27.13)
In air conditioning technology, it is necessary to define
thermodynamic processes and the properties of moist
air.
This may be achieved by a good knowledge of
physics, with theoretical calculations using complicated
formulae and tables. The procedure can be time
consuming.
By presenting the interrelated factors on a
psychrometric chart, an immediate decision can be
made regarding the feasibility of controlling an air
Functions
Temperature control
The duct sensor f1 or the room sensor f2 measures the
temperature t
R
. The controller u1 compares this value with
the selected setpoint X
K
and adjusts the heating coil valve
s1 or the cooling coil valve s2 in sequence in accordance
with the difference between the two.
Humidity control
The duct sensor f1 or the room sensor f2 measures the
humidity ϕ
R
. The controller u2 compares this value with the
selected setpoint X
K
and adjusts the humidfying value s3 or
the cooling valve s2 in sequence in accordance with the
difference bentween the two.
Safety devices
When there is danger of frost, the frost protection thermostat
f4 must switch off the fan, close the damper s4, open the
heating coil valve s1 and, where appropriate, switch on the
heating pump.
Variant: with low limit supply air temperature control
The low limit supply air temperature sensor f3 prevents the
supply air temperature t
zu
from dropping below the cut-in
point X
E
set on the controller u1 (draught elimination).
Variant: with summer compensation.
The outside temperature compensation sensor u3 is used to
increase the room temperature t
R
in summer. If the outside
temperatue t
a
rises above the cut-in point X
E
(22°C), the
setpoint X
K
is increased continuously by the selected
steepness S
S
.
Engineer uses a psychrometric chart to determine the
physical properties of the air to be handled.
Controller output temperature
t
R
[°C]
+
x
K
s2
s1
–
0 V
Y
20 V
Controller output humidity
ϕ
R
[%rH]
+
x
K
s2
s3
–
0 V
Y
20 V
t
R
[°C]
u3
+
t
s
[°C]
+
x
K
–
–x
E [22 °C]
s
S
Setpoint curve
Setpoint curve
t
R
[°C]
f3
+
t
zu
[°C]
+
x
K
–
– x
E