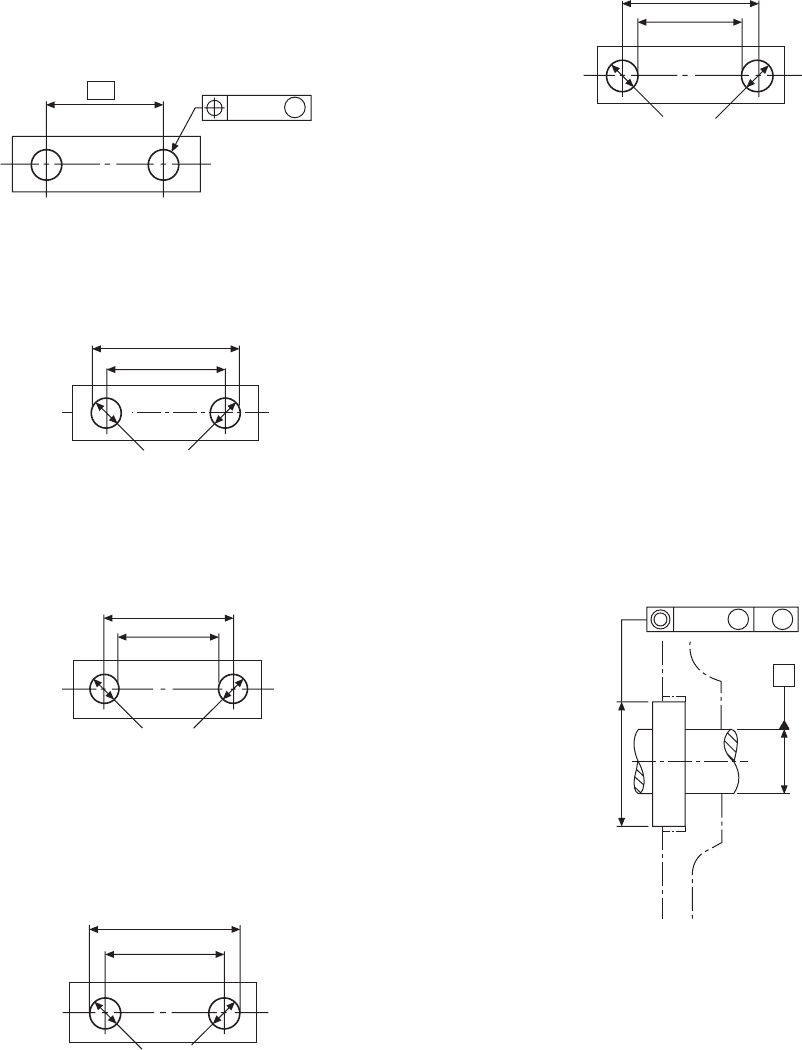
Maximum material and least material principles 181
Maximum material
condition applied to
position
A typical drawing instruction is given in Fig. 22.8,
and the following illustrations show the various extreme
dimensions which can possibly arise.
when the holes are finished away from the maximum
material condition.
Note that the total tolerance zone is 0.2 + 0.1 = 0.3, and
therefore the positional tolerance can be increased where
the two holes have a finished size away from the maximum
material condition.
70
Ø 0.2 M
2 Holes Ø 12.0
12.1
Fig. 22.8
Condition D (Fig. 22.12)
To give the same assembly condition as in B, the
maximum distance between hole centres is increased
Condition B (Fig. 22.10)
Maximum distance between hole centres and maximum
material condition of holes
Condition A (Fig. 22.9)
Minimum distance between hole centres and the
maximum material condition of holes.
Ø 12
69.8
81.8
Fig. 22.9
70.2
58.2
Ø 12
Fig. 22.10
Condition C (Fig. 22.11)
To give the same assembly condition as in A, the
minimum distance between hole centres is reduced
when the holes are finished away from the maximum
material condition.
81.8
69.8
Ø 12.1
Fig. 22.11
Maximum material
condition applied to
coaxiality
In the previous examples, the geometrical tolerance
has been related to a feature at its maximum material
condition, and, provided the design function permits,
the tolerance has increased when the feature has been
finished away from the maximum material condition.
Now the geometrical tolerance can also be specified
in relation to a datum feature, and Fig. 22.13 shows a
typical application and drawing instruction of a shoulder
on a shaft. The shoulder is required to be coaxial with
the shaft, which acts as the datum. Again, provided the
design function permits, further relaxation of the quoted
geometrical control can be achieved by applying the
maximum material condition to the datum itself.
70.3
58.2
Ø 12.1
Fig. 22.12
Ø 0.2
M
M
X
X
15.00
Ø
14.98
30.0
Ø
29.8
Various extreme combinations of size for the shoulder
and shaft can arise, and these are given in the drawings
below. Note that the increase in coaxiality error which
could be permitted in these circumstances is equal to
the total amount that the part is finished away from its
maximum material condition, i.e. the shoulder tolerance
plus the shaft tolerance.
Condition A (Fig. 22.14). Shoulder and shaft at
maximum material condition; shoulder at maximum
permissible eccentricity to the shaft datum axis X.
Fig. 22.13