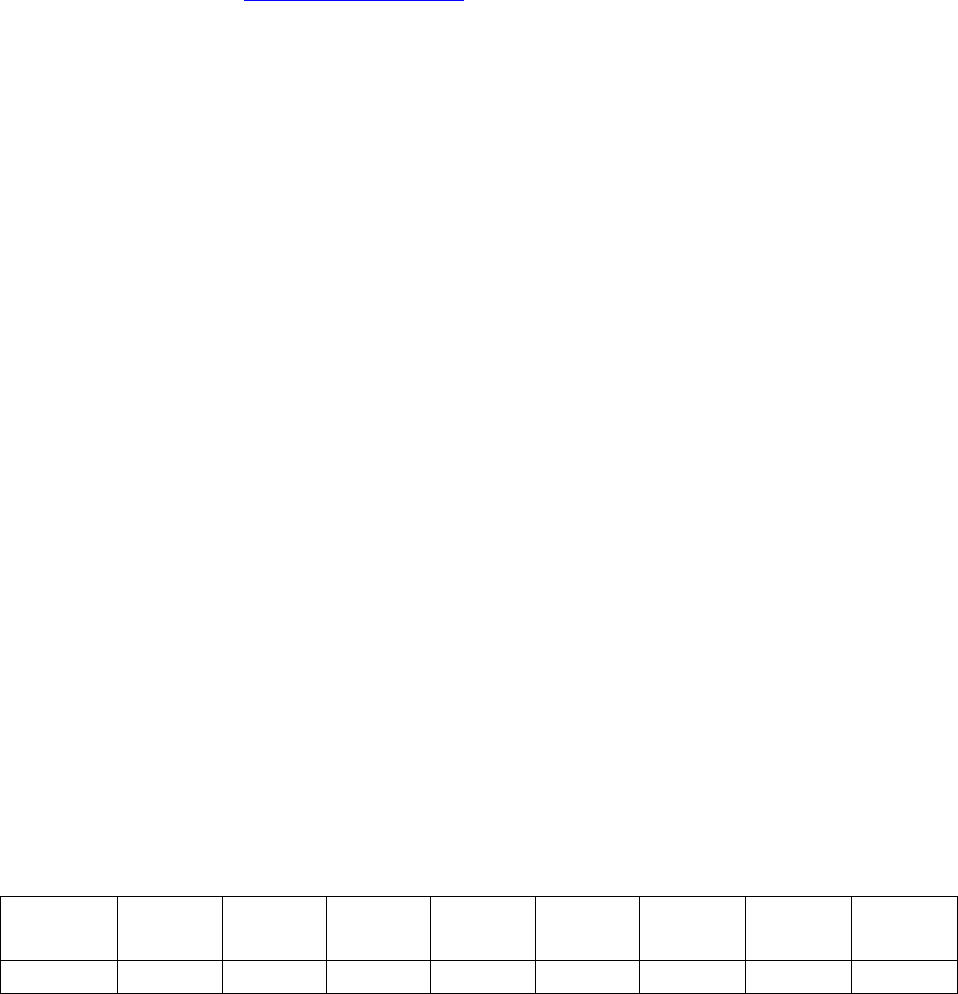
Секция 6. Формирование структуры и свойств металлопродукции.
555
ВЛИЯНИЯ ПАРАМЕТРОВ СТУПЕНЧАТОГО ОХЛАЖДЕНИЯ НА
ФОРМИРОВАНИЕ ДВУХФАЗНОЙ ФЕРРИТНО-МАРТЕНСИТНОЙ СТРУКТУРЫ
Шипунова М.В., Потемкин В.К.
РФ, Национальный исследовательский технологический университет «МИСиС»,
mvshipunova@mail.ru, potemkinvk@rambler.ru
Современные тенденции в производстве наземного транспорта выражаются в
стремлении к снижению его массы, повышению эффективности антикоррозионной
защиты, улучшению поведения автомобиля при столкновении, к уменьшению шумового
загрязнения среды, не теряя при этом за годы эксплуатации свой привлекательный вид и
т.п.[1]
К основным используемым в настоящее время сталям повышенной прочности
относятся стали с BH - эффектом, высокопрочные IF – стали, микролегированные
высокопрочные стали (HSLA), двухфазные (DP), комплексные (СP) и мартенситные стали
(Mart),
стали с остаточным аустенитом (TRIP).
Среди них наибольшее использование находят двухфазные ферритно-
мартенситные стали (ДФМС), применяемые для изготовления кузова, дисков колес,
диагональных рычагов подвески и других профилей автомобиля.[2]
Микроструктура двухфазных сталей (ДФМС) состоит из двух основных фаз:
ферритной мягкой и пластичной, которая определяет относительно невысокий предел
текучести, и мартенситной, твердой, придающей этой стали необходимую прочность.
Ступенчатое охлаждение на отводящем рольганге широкополосных станов,
позволяет эффективно регулировать соотношение ферритной и мартенситной фаз.[3]
Целью работы является исследование возможности управления соотношением
ферритной и мартенситной фаз горячекатаных двухфазных сталей путем изменения
параметров ступенчатого охлаждения на отводящем рольганге. В работе поставлены
следующие задачи: изучение влияния на соотношение фаз в ДФМС температуры конца
прокатки, температуры смотки, температуры начала ускоренного охлаждения и
длительности этапа ускоренного охлаждения.
Для исследования использовали экономнолегированную (не содержащая молибдена)
марку стали 06ХГСЮ. Химический состав этой стали приведен в таблице 1.
Таблица 1 – Химический состав исследуемой стали, %
Марка
стали
С Si Mn Cr A1 N S P
06ХГСЮ
0,08 0,42 1,1 0,33 0,04 0,005 0,015 0,015
Моделировали прокатку горячекатаной полосы толщиной 2,5 мм и шириной 1610
мм из указанной марки стали на НШПС 2000 Череповецкого металлургического
комбината.
Исследование проводили с использованием математической модели
прогнозирования структуры и механических свойств листовой стали при горячей прокатке,
разработанной ранее в НИТУ «МИСиС».
Математическая модель позволяет рассчитывать: