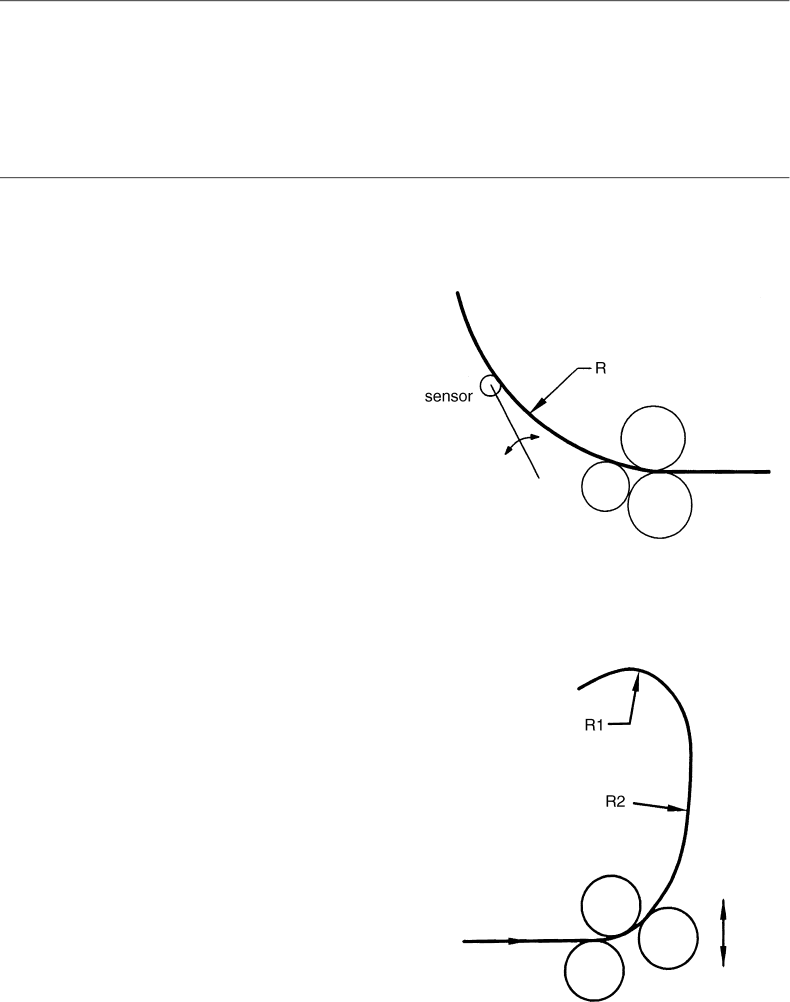
The biggest obstacle in introducing hot roll forming is not the cost of the equipment, but rather the
resistanceofmetal fabricators to change. Eventually,perhaps this resistance will be overcome as the
benefits of the process are seen to outweighthe additional costs.
15.16 Press Tooling for Conventional Roll Forming Lines
Dramatic changes in prepunching or postpunching,notching,orcutoffdies are not expected. However,
the already available compact high-speed hydraulic presses will allow operation at 600 to 800 ft/min
(180 to 245 m/min) and faster.These small presses, along withtechnologyborrowed from the turret
punch system, will speed up tool change and the N/C or computer control will provide versatility.
15.17 Computer-Controlled Roll Forming Lines
The application of N/C, PLC, computers, and other devices will greatly increase in the near future.Some
lines will operate accordingtothe prepared programs, while others will be based on data received from
sensors, and will adjust the mill, tooling,and other componentstomaintain uniform quality.
Forexample, in the case of athree-roll curving
unit, asensor can measurethe curving radius
during the curving process (Figure 15.24). The
data feedback can be used to adjust the curving
rolls to maintain the specified radius.
Curving rolls, controlled by servo motor and
governed by preprogrammed data, are already
used to form parts with variable radii to tight
tolerances (Figure15.25). Some dimensions of
the products, for example, the width of a“U”
channel, can be held tightly by either measuring
or sensing the width. The pass influencing the
width can be adjusted either manually by push
buttons or automatically through servo motors
(see Figure15.26).
When aroll forming mill with good tooling is
properly set up,itcan produce parts to very tight
tolerances without anyadjustment from consist-
ent, uniform material. However,owing to fluctu-
ation in strip dimensions,dev iationfrom
straightness andflatness, andvariations in
mechanical properties,the material is never
uniform. Therefore, operators regularly have to
makeadjustments to the mill. Onceenoughdata
is available to knowwhat mill adjustment has to
be made when the finished product deviates from
the specified shape, length, or straightness, a
properly programmed computer can adjust the
mill using servo motors. Servo motor adjusted
shafts or side rollers can keep formed angles
within tight tolerances.
Servomotor controlled straightenershave
already been developed to keep products straight
at the end of the line.
FIGURE15.24 Sensor- co ntrolled, servomotor
adjusted curving unit.
FIGURE 15.25 Computer-controlled curving unit can
curve sections with different radii.
Roll Forming Handbook15-16