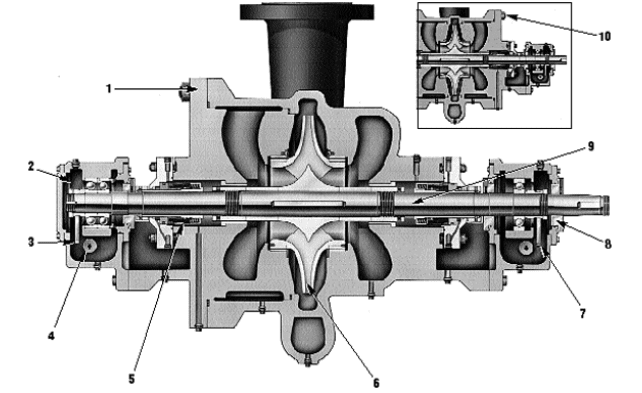
9.7 PETROLEUM INDUSTRY 9.137
FIGURE 3 Between bearings, single stage, double section radially split pump
—
API 610 Type BB2. (1) Pump
casing and cover with metal-to-metal confined gasketed joint, (2) Thrust bearing housing with back-to-back angular
contact ball bearings, (3) Oil ring lubrication, (4) Cooling insert, (5) Seal chamber and cartridge mechanical seal, (6)
Double suction impeller, dynamically balanced, (7) Radial bearing housing with deep-groove radial ball bearing and
oil ring lubrication, (8) Labyrinth-type flingers at all bearing housing—shaft openings, (9) Heavy duty shaft to limit
deflection at the seals and impeller, (10) Double cover design on some models. (Flowserve Corporation)
pumps must be able to withstand. Further, it outlines a test procedure to allow verification
that a pump meets these minimum nozzle load requirements.The coordinate system for ori-
entation of nozzle loads is in accordance with ISO 1503 standard convention.
Inline pumps have been developed, in part, to avoid the problem of misalignment due to
nozzle loads. Figure 6 shows a single stage, overhung, inline pump with a separate bearing
frame, Type OH3. Figure 7 shows a high-speed integrally geared inline pump, Type OH6.
For a given flange size, inline pumps are required to withstand twice the magnitude of noz-
zle loads allowed for horizontal pumps. In addition, installation is simplified and less expen-
sive because a block foundation is not required, and the pump mounts in a pipeline similar
to a valve, although most users supply a support of some kind for the pump. Furthermore,
the vertical arrangement causes the pump to take up much less space.The Type OH6 pump
(Figure 7) has a gear box that increases the speed at which the impeller spins and typically
produces high heads at relatively low flows.This type of design has many advantages in cer-
tain low flow, high head services. Some alternative inline pump designs utilize high-speed
motors that eliminate the need for the gearbox. High-speed pumps may also be supplied
with inducers in front of the typically radially bladed impellers to improve suction (NPSH)
performance. When this is done, the range of operation of the pump may be restricted to
avoid off-design flow instability. This should be recognized and the required range of pump
operation should be addressed during the applications stage of pump selection.
Pumps of overhung shaft construction are nominally limited by most manufacturers to
drivers rated below 500 hp (375 kW). Units with greater power requirements are usually
designed with bearings on both ends of the shaft and the impeller
—
or impellers
—
in
between the bearings (designated by API 610 as between bearings, or Type BB, pumps).
Ball bearing construction, in compliance with requirements of API 610, is used to a limit of
a bearing Nd
m
factor of 500,000.The Nd
m
factor is the product of the pump operating speed
(N), in revolutions per minute and the mean bearing diameter (d
m
), equal to the bearing
bore plus the bearing outside diameter, divided by 2 (all dimensions in millimeters). For
values of Nd
m
above 500,000, or where the bearing basic life rating (L
10h
) does not meet the