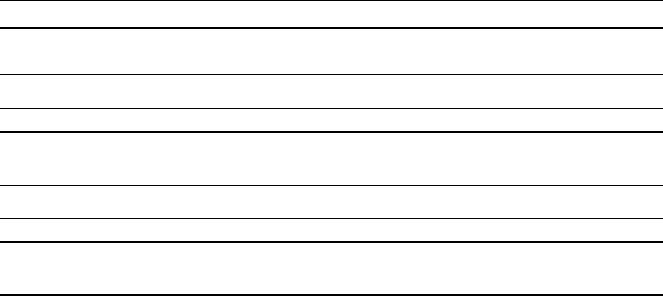
of the combined cycle plant. The synthetic gas is the result of several reactions
between fuel (a mix of coal and petroleum coke) with oxygen/steam at high
temperatures of up to 1,600C. The required oxygen for the gasification process is
produced in an integrated ASU (based on a cryogenic process), which also pro-
duces pure nitrogen for drying the pulverised fuel, for fuel transportation and for
the safety inertisation of the different circuits with a purity of 99.99% and waste
nitrogen with 98% purity to dilute clean gas from gasification unit before being
burnt in the gas turbine combustion chamber. Figure 3 shows the ELCOGAS
IGCC simplified flow diagram.
The synthetic gas obtained, which basically consists of CO and H
2
, is subse-
quently subjected to an exhaustive cleaning process to eliminate the small parts of
pollutants, fly ash, halogens, cyanides, sulphur compounds, etc. Then, the so-called
clean gas, free of pollutants, is saturated, mixed with waste nitrogen (to reduce
NO
x
formation) and burnt, with a high-efficiency level, in the gas turbine of the CC
electricity-generating unit. The gas turbine (model V94.3, 200 MW
e
under ISO
conditions) is capable of operating with both synthetic and natural gases. The gas
turbine exhaust gases with residual heat are fed into a heat recovery steam
generator (HRSG), producing steam that is used together with the steam produced
in the gasification process to generate additional electricity in a conventional steam
turbine (135 MW
e
under ISO conditions) with condensation cycle. The demon-
strated plant net efficiency is 42.2% under ISO conditions.
The design of the heat exchangers battery is particularly relevant in terms of
efficiency, basically as regard steam production and consumption, incorporating
two heat recovery boilers, one for the raw gas produced in the gasifier and the
other for the turbine exhaust gases. Furthermore, the steam acts as a heat conductor
for several uses in gasification, desulphurisation and air separation processes.
The Puertollano power plant was designed with a high-integration level that
involves the integration of the three previously mentioned units:
• Integration of the gasification island and combined cycle water–steam systems:
The water fed to the steam generators is pre-heated in a section of the combined
Table 1 Summary of the ELCOGAS IGCC power plant main data
Design fuel: coal and petcoke (50 wt%.)
Coal Petcoke Mix
LHV (MJ/kg) 13.10 31.99 22.55
Electrical output
Gas turbine (MW) Steam turbine (MW) Total gross (MW) Total net (MW)
ISO conditions 200 135 335 300
Site conditions 182.3 135.4 317.7 282.7
Efficiency (LHV)
Gross Net
Thermal efficiency 47.12% 42.2%
Heat rate 7,647 kJ/kWh 8,538 kJ/kWh
280 P. Coca et al.