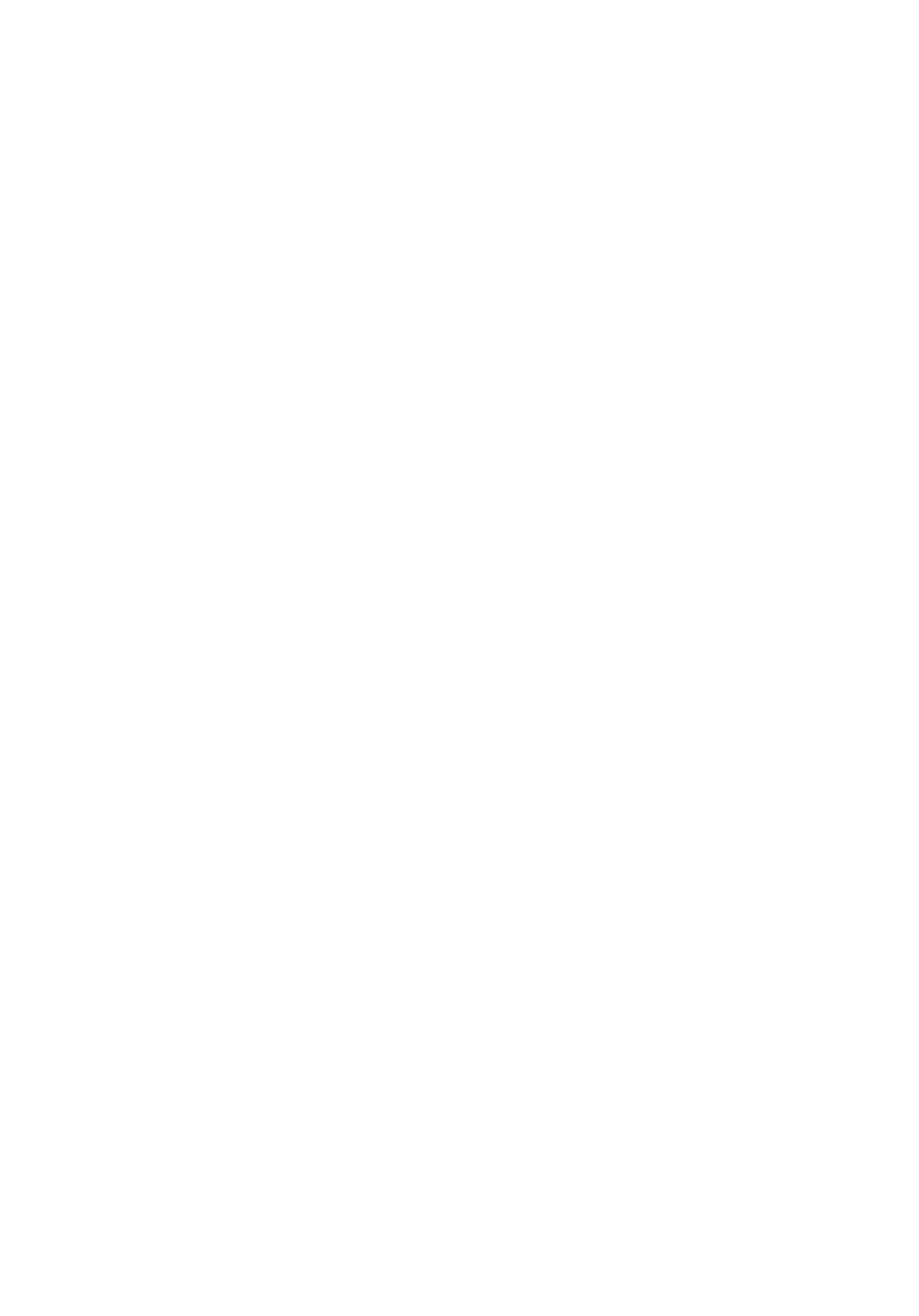
43
200…220
0
С. При повороте бункера на 180
0
модель покрывается сухой
смесью (рис.2.10 б). Под действием тепла моделей и модельной плиты
слой смеси, прилегающий к ним, оплавляется. Толщина оплавленного
слоя зависит от времени контакта смеси с моделью, а также от темпе-
ратуры предварительного нагрева модельной плиты и модели и состав-
ляет 5…25мм. Время контакта колеблется от 10 до 40с.
Следующий этап − поворот бункера на 180
0
. При этом излишки су-
хой смеси осыпаются на дно бункера (рис.2.10 в). Сформировавшаяся
пластичная оболочка вместе с модельной плитой снимается с бункера и
подается в печь с температурой 300-400
0
С, где она необратимо затвер-
девает в течение 60-90с.
Затвердевшая оболочка с помощью толкателей отделяется от мо-
дели. Аналогично изготавливают вторую полуформу. Готовые оболоч-
ковые полуформы склеиваются по плоскости разъема или скрепляются
скобами. При необходимости предварительно в форму устанавливается
стержень, тоже оболочковый. Собранная форма устанавливается в кон-
тейнер, который заполняется либо кварцевым песком, либо металличе-
ской дробью (рис.2.10 г).
Для литья в оболочковые формы характерны такие преимущества:
повышенная точность отливок и хорошее качество их поверхности за
счет использования металлической модели и мелкого кварцевого песка.
Это позволяет уменьшить величину припусков на механическую обра-
ботку и тем самым сократить объем механической обработки в целом на
20-50%.
Благодаря высокой цикличности процесс хорошо автоматизирует-
ся. В промышленности для изготовления оболочковых полуформ ис-
пользуют четырехпозиционные полуавтоматы, которые производят 150-
400 полуформ в час. Это в свою очередь влияет как на повышение про-
изводительности труда в целом, так и на улучшение условий труда в ли-
тейных цехах.
Отпадает трудоемкая операция выбивки отливок из формы и
стержней из отливок; тонкостенные формы от контакта с расплавлен-
ным металлом после заливки практически полностью разрушаются
вследствие выгорания связующей смолы, а оставшийся кварцевый пе-
сок используется повторно.
Расход формовочных смесей уменьшается в 10-20 раз по сравне-
нию с литьем в песчаные формы; особенно выгоден процесс при изго-
товлении полых оболочковых стержней.
При литье в оболочковые формы повышается качество отливок за
счет уменьшения дефектов по пригару, трещинам, газовым раковинам.
Рассматриваемый способ литья в оболочковые формы имеет не-
которые недостатки. Прежде всего, это ограниченность применения: ме-
тод экономически целесообразно использовать только в массовом и