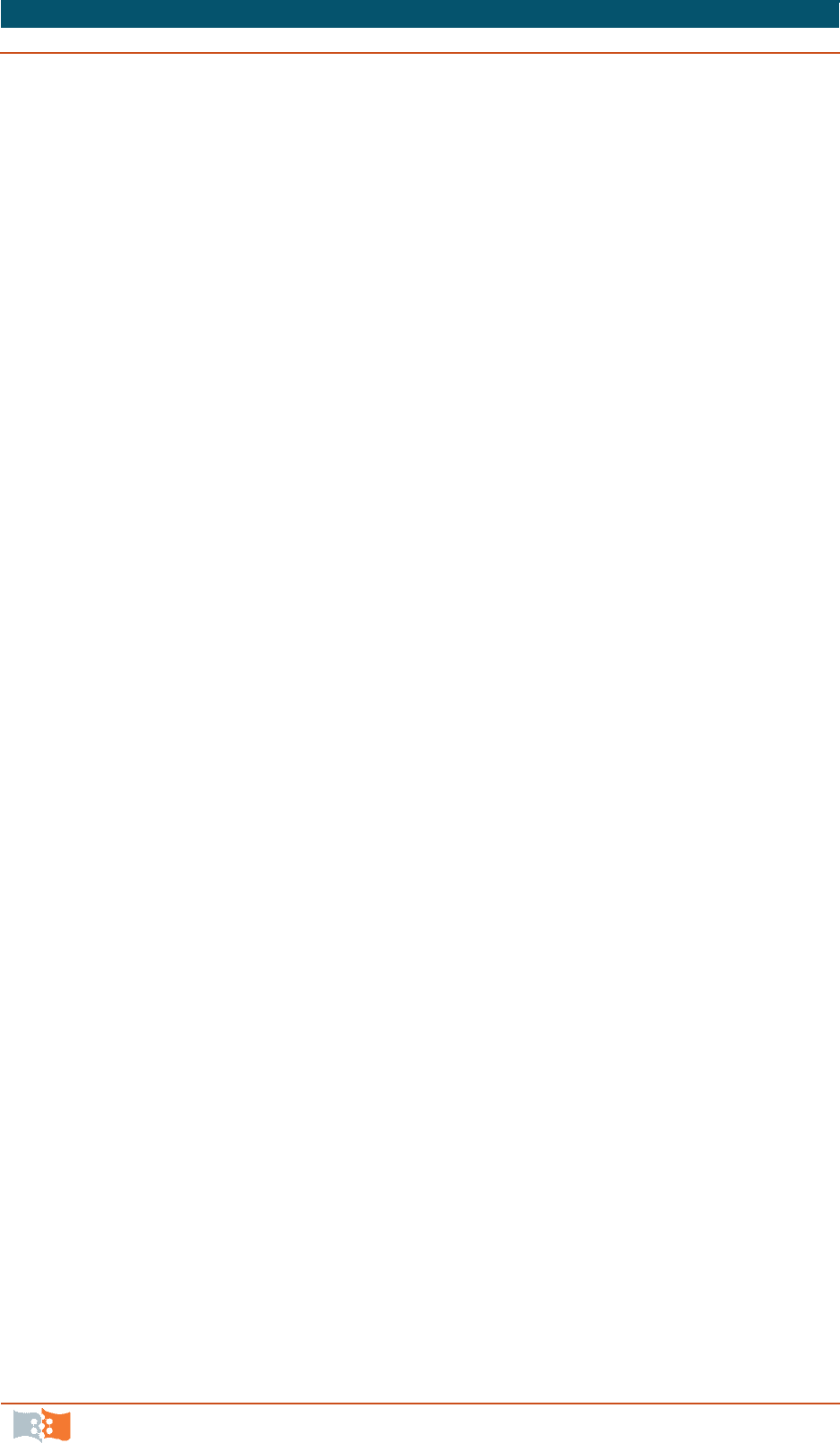
2.6. Автогенные процессы в металлургии свинца
Металлургия тяжелых цветных металлов. Учеб. пособие
осуществляется реакционная плавка с получением свинца и богатого шлака
(~60 % свинца). Полученный в окислительной зоне свинец непрерывно выте-
кает из реактора через сифон. Богатый шлак перетекает в восстановительную
зону, где восстанавливается вдуваемой через фурмы угольной пылью до ко-
нечного содержания свинца 2 % в шлаке. В восстановительной зоне темпера-
тура поддерживается 1 100–1 230 °С.
Шлаковая ванна между окислительной и восстановительной зонами
разделена перегородкой. Восстановленный из шлака свинец выпускается из
восстановительной зоны. Обедненный шлак после отстаивания выпускают
через летку и гранулируют. В процессе предусмотрена высокая степень ути-
лизации тепла.
Планируется строительство на этом же заводе промышленного ком-
плекса «Q-S-L» мощностью 100 тыс. т в год чернового свинца. Процесс
«Q-S-L» будет также внедрен в промышленном масштабе на новом заводе в
Бей-Ине (КНР). Мощность завода 50 тыс. т чернового свинца в год.
В начале 1928 г. на заводе «Реншер» (Швеция) прошла промышленное
опробование плавка богатых свинцовых концентратов (66,1–76,4 % Pb) в
конвертере TBRC. Способ основан на совмещении процессов плавки сухих
концентратов и обеднения шлаков в одном агрегате.
Процесс осуществляется в две стадии: автогенная плавка концентратов
при обогащении дутья кислородом с образованием чернового свинца и шла-
ка; предварительное восстановление шлака исходным концентратом, а затем
заключительное восстановление коксовой мелочью. На первой стадии ведут
плавку концентрата и загрузку извести. Продувку осуществляют на обога-
щенном до 50 % О
2
дутье. Содержание серы в первичном свинце 0,5 %. Со-
держание свинца в шлаке будет составлять 35–55 % при извлечении свинца в
металл на первой стадии менее 70 %. Во вторую стадию ведут загрузку флюсов
к шлаку, количество которых дозируют исходя из условий получения шлака
после восстановления следующего состава, %: 20 СaО; 25 SiО
2
; 35 (Fe + Zn).
Предварительное восстановление шлака осуществляют свинцовым
концентратом, вдуваемым в ванну воздухом со скоростью 300 кг/мин. После
снижения содержания свинца в шлаке меньше 35 % приступают к заключи-
тельному восстановлению коксовой мелочью, загружаемой в ванну.
Скорость
вращения конвертера в восстановительный период составляет 4–5 об/мин;
здесь особенно важна поверхность контакта коксика со шлаком.
Восстановление заканчивается при содержании свинца в шлаке 3 %,
дальнейшее снижение экономически не оправдано. Испытания данного ме-
тода выплавки свинца показали, что износ футеровки конвертера не превы-
шал 30 мм в неделю. Энергозатраты в 3 раза ниже, чем при традиционной
шахтной плавке. Содержание SO
2
в отходящих газах составило 10–12 %.
Процесс плавки свинцовых концентратов в конвертере позволяет соблюдать
жесткие требования по содержанию свинца в воздухе.
Процесс фирмы «Каминко» испытан на опытной установке производи-
тельностью 100 т концентрата в сутки. Для введения концентрата в печь ис-
пользуется вертикальная фурма. Из-за небольшого расстояния между концом