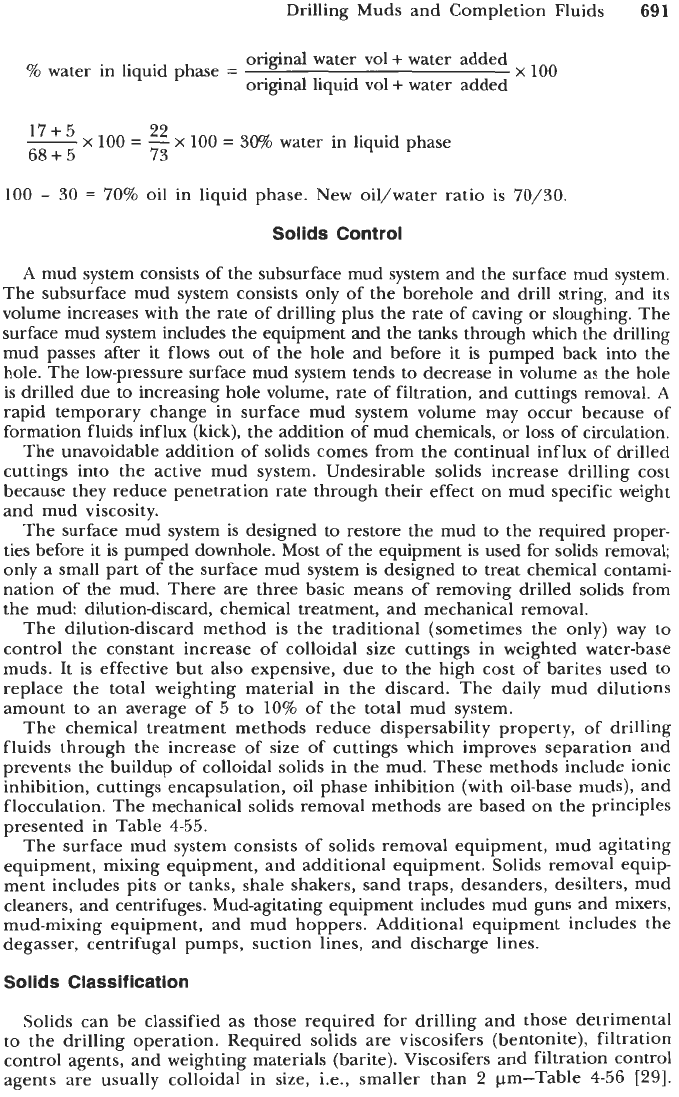
Drilling Muds and Completion Fluids
691
original water vol
+
water added
original liquid vol
+
water added
%
water in liquid phase
=
x
100
22
l7
+
68+5
73
x
100
=
-
x
100
=
30%
water in liquid phase
100
-
30
=
70% oil in liquid phase. New oil/water ratio
is
70/30.
Solids
Control
A
mud system consists of the subsurface mud system and the surface mud system.
The subsurface mud system consists only of the borehole and drill string, and
its
volume increases with the rate of drilling plus the rate of caving or sloughing. The
surface mud system includes the equipment and the tanks through which the drilling
mud passes after it flows out of the hole and before it is pumped back into the
hole. The low-pressure surface mud system tends to decrease in volume as the hole
is drilled due to increasing hole volume, rate of filtration, and cuttings removal.
A
rapid temporary change in surface mud system volume may occur because
of
formation fluids influx (kick), the addition of mud chemicals, or loss of circulation.
The unavoidable addition of solids comes from the continual influx of drilled
cuttings into the active mud system. Undesirable solids increase drilling cost
because they reduce penetration rate through their effect on mud specific weight
and mud viscosity.
The surface mud system is designed
to
restore the mud to the required proper-
ties before it is pumped downhole. Most of the equipment is used for solids removal;
only a small part of the surface mud system
is
designed to treat chemical contami-
nation of the mud. There are three basic means of removing drilled solids from
the mud: dilution-discard, chemical treatment, and mechanical removal.
The dilution-discard method is the traditional (sometimes the only) way to
control the constant increase of colloidal size cuttings in weighted water-base
muds. It is effective but also expensive, due to the high cost of barites used to
replace the total weighting material in the discard. The daily mud dilutions
amount to an average of
5
to
10%
of the total mud system.
The chemical treatment methods reduce dispersability property, of drilling
fluids through the increase of size of cuttings which improves separation and
prevents the buildup of colloidal solids in the mud. These methods include ionic
inhibition, cuttings encapsulation, oil phase inhibition (with oil-base muds), and
flocculation. The mechanical solids removal methods are based on the principles
presented in Table 4-55.
The surface mud system consists of solids removal equipment, mud agitating
equipment, mixing equipment, and additional equipment. Solids removal equip-
ment includes pits or tanks, shale shakers, sand traps, desanders, desilters, mud
cleaners, and centrifuges. Mud-agitating equipment includes mud guns and mixers,
mud-mixing equipment, and mud hoppers. Additional equipment includes the
degasser, centrifugal pumps, suction lines, and discharge lines.
Solids Classification
Solids can be classified as those required for drilling and those detrimental
to the drilling operation. Required solids are viscosifers (bentonite), filtration
control agents, and weighting materials (barite). Viscosifers and filtration control
agents are usually colloidal in size, i.e., smaller than
2
pm-Table 4-56
[29].