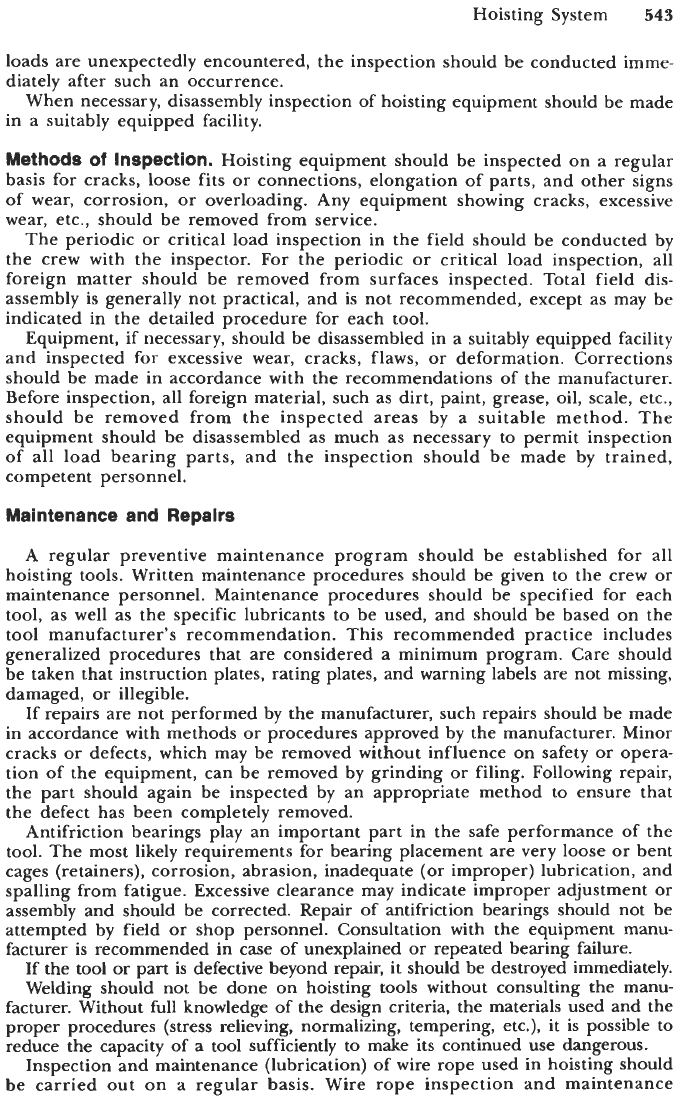
Hoisting System
543
loads are unexpectedly encountered, the inspection should be conducted imme-
diately after such an occurrence.
When necessary, disassembly inspection of hoisting equipment should be made
in a suitably equipped facility.
Methods
of
Inspection.
Hoisting equipment should be inspected on a regular
basis for cracks, loose fits or connections, elongation of parts, and other signs
of wear, corrosion, or overloading. Any equipment showing cracks, excessive
wear, etc., should be removed from service.
The periodic or critical load inspection in the field should be conducted by
the crew with the inspector. For the periodic or critical load inspection, all
foreign matter should be removed from surfaces inspected. Total field dis-
assembly is generally not practical, and is not recommended, except as may be
indicated in the detailed procedure for each tool.
Equipment, if necessary, should be disassembled in a suitably equipped facility
and inspected for excessive wear, cracks, flaws, or deformation. Corrections
should be made in accordance with the recommendations of the manufacturer.
Before inspection, all foreign material, such as dirt, paint, grease, oil, scale, etc.,
should be removed from the inspected areas by a suitable method. The
equipment should be disassembled as much as necessary to permit inspection
of all load bearing parts, and the inspection should be made by trained,
competent personnel.
Maintenance and Repairs
A
regular preventive maintenance program should be established for all
hoisting tools. Written maintenance procedures should be given to the crew
or
maintenance personnel. Maintenance procedures should be specified for each
tool, as well as the specific lubricants to be used, and should be based on the
tool manufacturer’s recommendation. This recommended practice includes
generalized procedures that are considered a minimum program. Care should
be taken that instruction plates, rating plates, and warning labels are not missing,
damaged, or illegible.
If
repairs are not performed by the manufacturer, such repairs should be made
in accordance with methods or procedures approved by the manufacturer. Minor
cracks or defects, which may be removed without influence on safety or opera-
tion
of
the equipment, can be removed by grinding or filing. Following repair,
the part should again be inspected by an appropriate method to ensure that
the defect has been completely removed.
Antifriction bearings play an important part in the safe performance of the
tool. The most likely requirements for bearing placement are very loose or bent
cages (retainers), corrosion, abrasion, inadequate (or improper) lubrication, and
spalling from fatigue. Excessive clearance may indicate improper adjustment or
assembly and should be corrected. Repair of antifriction bearings should not be
attempted by field or shop personnel. Consultation with the equipment manu-
facturer is recommended in case of unexplained or repeated bearing failure.
If the
tool
or part is defective beyond repair, it should
be
destroyed immediately.
Welding should not be done
on
hoisting tools without consulting the manu-
facturer. Without full knowledge of the design criteria, the materials used and the
proper procedures (stress relieving, normalizing, tempering, etc.), it is possible to
reduce the capacity
of
a
tool sufficiently to make its continued use dangerous.
Inspection and maintenance (lubrication) of wire rope used in hoisting should
be carried out on a regular basis. Wire rope inspection and maintenance