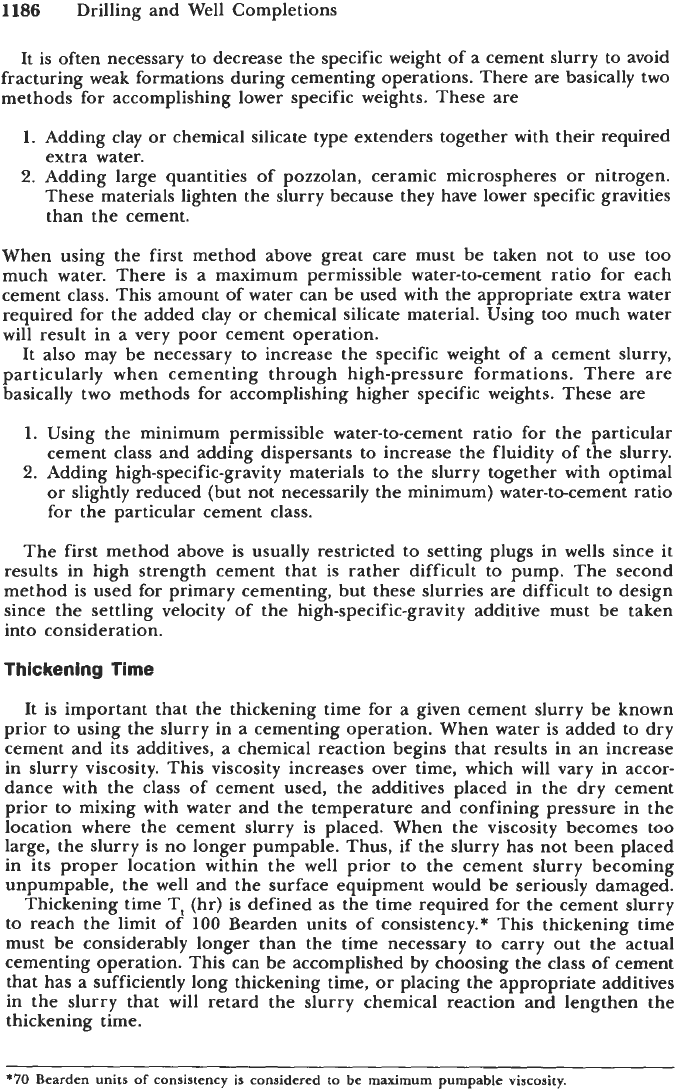
1186
Drilling and Well Completions
It is often necessary to decrease the specific weight of a cement slurry to avoid
fracturing weak formations during cementing operations. There are basically two
methods for accomplishing laver specific weights. These
are
1.
Adding clay
or
chemical silicate type extenders together with their required
extra water.
2.
Adding large quantities of pozzolan, ceramic microspheres
or
nitrogen.
These materials lighten the slurry because they have lower specific gravities
than the cement.
When using the first method above great care must be taken not to use too
much water. There is a maximum permissible water-to-cement ratio for each
cement class. This amount of water can be used with the appropriate extra water
required for the added clay
or
chemical silicate material. Using too much water
will result in
a
very poor cement operation.
It also may be necessary to increase the specific weight of a cement slurry,
particularly when cementing through high-pressure formations. There are
basically two methods for accomplishing higher specific weights. These are
1.
Using the minimum permissible water-to-cement ratio for the particular
cement class and adding dispersants to increase the fluidity of the slurry.
2.
Adding high-specific-gravity materials to the slurry together with optimal
or slightly reduced (but not necessarily the minimum) water-to-cement ratio
for the particular cement class.
The first method above
is
usually restricted to setting plugs in wells since it
results in high strength cement that is rather difficult
to
pump. The second
method is used for primary cementing, but these slurries are difficult to design
since the settling velocity of the high-specific-gravity additive must be taken
into consideration.
Thickening
Time
It is important that the thickening time for
a
given cement slurry be known
prior to using the slurry in a cementing operation. When water is added to dry
cement and its additives, a chemical reaction begins that resuIts in an increase
in slurry viscosity. This viscosity increases over time, which will vary in accor-
dance with the class
of
cement used, the additives placed in the dry cement
prior to mixing with water and the temperature and confining pressure in the
location where the cement slurry is placed. When the viscosity becomes too
large, the slurry is no longer pumpable. Thus, if the slurry has not been placed
in its proper location within the well prior to the cement slurry becoming
unpumpable, the well and the surface equipment would be seriously damaged.
Thickening time Tt (hr)
is
defined as the time required for
the
cement slurry
to reach the limit of
100
Bearden units of consistency.* This thickening time
must
be
considerably longer than the time necessary to carry out the actual
cementing operation. This can be accomplished
by
choosing the class of cement
that has
a
sufficiently long thickening time,
or
placing the appropriate additives
in the slurry that will retard the slurry chemical reaction and lengthen the
thickening time.
*70
Bearden units
of
consistency is considered
to
be
maximum
pumpable viscosity.