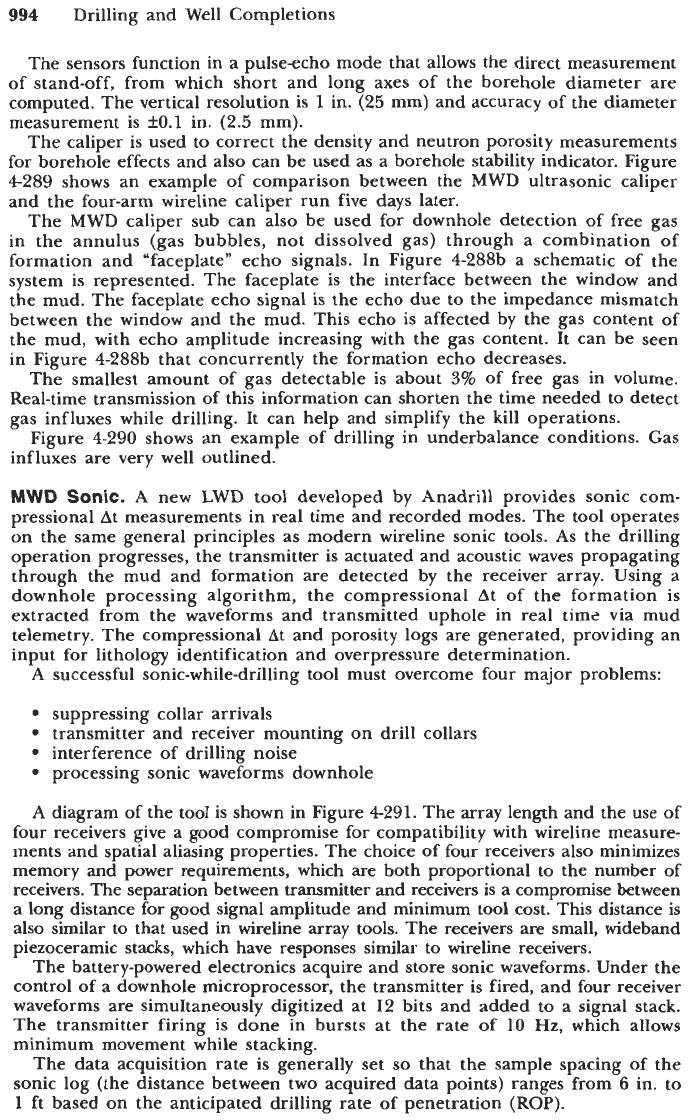
994
Drilling and Well Completions
The sensors function in a pulseecho mode that allows the direct measurement
of stand-off, from which short and long axes
of
the borehole diameter are
computed. The vertical resolution is
1
in.
(25
mm) and accuracy of the diameter
measurement is
fO.l
in.
(2.5
mm).
The caliper is used to correct the density and neutron porosity measurements
for borehole effects and also can be used as a borehole stability indicator. Figure
4-289 shows an example of comparison between the MWD ultrasonic caliper
and the four-arm wireline caliper run five days later.
The MWD caliper sub can also be used for downhole detection
of
free gas
in the annulus (gas bubbles, not dissolved gas) through a combination of
formation and “faceplate” echo signals. In Figure 4-288b a schematic of the
system is represented. The faceplate is the interface between the window and
the mud. The faceplate echo signal is the echo due to the impedance mismatch
between the window and the mud. This echo is affected by the gas content of
the mud, with echo amplitude increasing with the gas content. It can be seen
in Figure 4-288b that concurrently the formation echo decreases.
The smallest amount of gas detectable is about
3%
of free gas in volume.
Real-time transmission of this information can shorten the time needed to detect
gas influxes while drilling. It can help and simplify the kill operations.
Figure 4-290 shows an example of drilling in underbalance conditions. Gas
influxes are very well outlined.
MWD
Sonic.
A new LWD tool developed
by
Anadrill provides sonic com-
pressional At measurements in real time and recorded modes. The tool operates
on the same general principles as modern wireline sonic tools.
As
the drilling
operation progresses, the transmitter is actuated and acoustic waves propagating
through the mud and formation are detected by the receiver array. Using a
downhole processing algorithm, the compressional At of the formation is
extracted from the waveforms and transmitted uphole in real time via mud
telemetry. The compressional At and porosity logs are generated, providing an
input for lithology identification and overpressure determination.
A
successful sonic-while-drilling tool must overcome four major problems:
suppressing collar arrivals
transmitter and receiver mounting on drill collars
interference of drilling noise
processing sonic waveforms downhole
A
diagram of the tool is shown in Figure 4291. The array length and the use of
four receivers give a good compromise for compatibility with wireline measure-
ments and spatial aliasing properties. The choice of four receivers also minimizes
memory and power requirements, which are both proportional to the number of
receivers. The separation between trapmitter and receivers is a compromise between
a
long distance for good signal amplitude and minimum tool cost. This distance is
also similar to that used in wireline array tools. The receivers are small, wideband
piezoceramic stacks, which have responses similar to wireline receivers.
The battery-powered electronics acquire and store sonic waveforms. Under the
control of a downhole microprocessor, the transmitter is fired, and four receiver
waveforms are simultaneously digitized at
12
bits and added to a signal stack.
The transmitter firing is done in bursts at the rate of
10
Hz, which allows
minimum movement while stacking.
The data acquisition rate is generally set
so
that the sample spacing of the
sonic log (the distance between two acquired data points) ranges from
6
in. to
1
ft based on the anticipated drilling rate of penetration
(ROP).