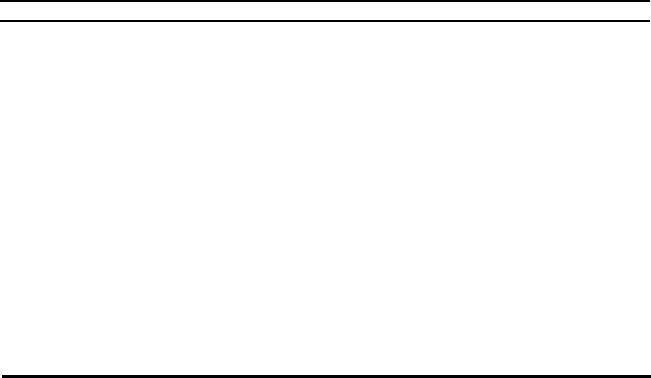
Petrochemical Catalysts 295
TABLE 7.8. Development of p-Xylene Oxidation Processes.
Process Catalyst Operating conditions
(a) p-xylene to p-toluic acid.
(b) p-toluic methyl ester to
monomethyl terephthalic
acid (Witton 1951)
Cobalt or manganese acetates
promoted by p-toluene sulfonic
acid.
140
o
–170
o
C, 4–8 atm
250
o
–280
o
C, 20–25 atm
(p-xylene selectivity 85%)
p-xylene in methanol solvent
to dimethyl terephthalate
Cobalt salts 100
o
–200
o
C, 5–20 atm
(p-xylene selectivity 90%)
p-xylene to pure terephthalic
acid (Amoco/Scientific De-
sign, 1958)
Reaction: cobalt and manganese
acetates in glacial acetic acid/
cocatalyst NH
4
BR plus tetra-
bromomethane
Purification: palladium supported
on carbon
Reaction: 190
o
–205
o
C, 15–
30 atm in stirred auto-
claves (95% conversion;
p-xylene selectivity 90%)
Purification: 225
o
–275
o
C to
hydrogenate 4-carboxy
benzaldehyde to p-toluic
acid in water solution.
p-xylene oxidized (with sub-
stance that provides hydrop-
eroxides, e.g., paraldehyde)
to pure terephthalic acid
Cobalt acetate in acetic acid
Catalysts used represent about
0.1% of the TPA produced
100
o
–140
o
C, 30 atm
(selectivity >97% but by-
product acetic acid forms)
mation of aromatic aldehydes.
76
These were converted to the acids via the per-
oxy intermediates. A further novelty of the process was the purification of prod-
uct by dissolving it at high pressure in water at 225°–275°C, and then hydrogen-
ating any 4-carboxybenzaldehyde by-product to p-toluic acid with a palladi-
um/carbon catalyst before allowing the terephthalic acid to crystallize. The same
process was used to oxidize toluene to benzoic acid in the Snia-Viscosa capro-
lactam process. The Amoco process has been widely licensed and now produces
the bulk of the terephthalic acid used in polyester manufacture. Terephthalic
acid is preferable to dimethylterephthalate in polyester production because the
reaction rate is faster and a better yield is obtained. The use of methanol is also
avoided.
The polyester polymer is produced in two steps to avoid side reactions. The
acid is esterified in an excess of ethylene glycol at 100°–150°C and 10–70 bar
using a cobalt or zinc acetate catalyst. The monomer then condenses at 150°–
270°C as a liquid melt under vacuum using an antimony oxide catalyst. Ethylene
oxide is removed by distillation as the polymerization proceeds. The use of an-
timony oxide catalyst always led to a slightly grey-colored product, as a result of
reduction of some of the antimony to the metallic state. Pure white polymer
could be obtained by the use of germanium dioxide catalyst, but the problem
was the very high cost of germanium relative to antimony. This problem was
solved in ICI by W Hewertson with the addition of phosphine oxide ligands to
the catalyst, which stabilized the antimony towards reduction. However, as is
often the case in production, the more stable catalyst could be operated at a