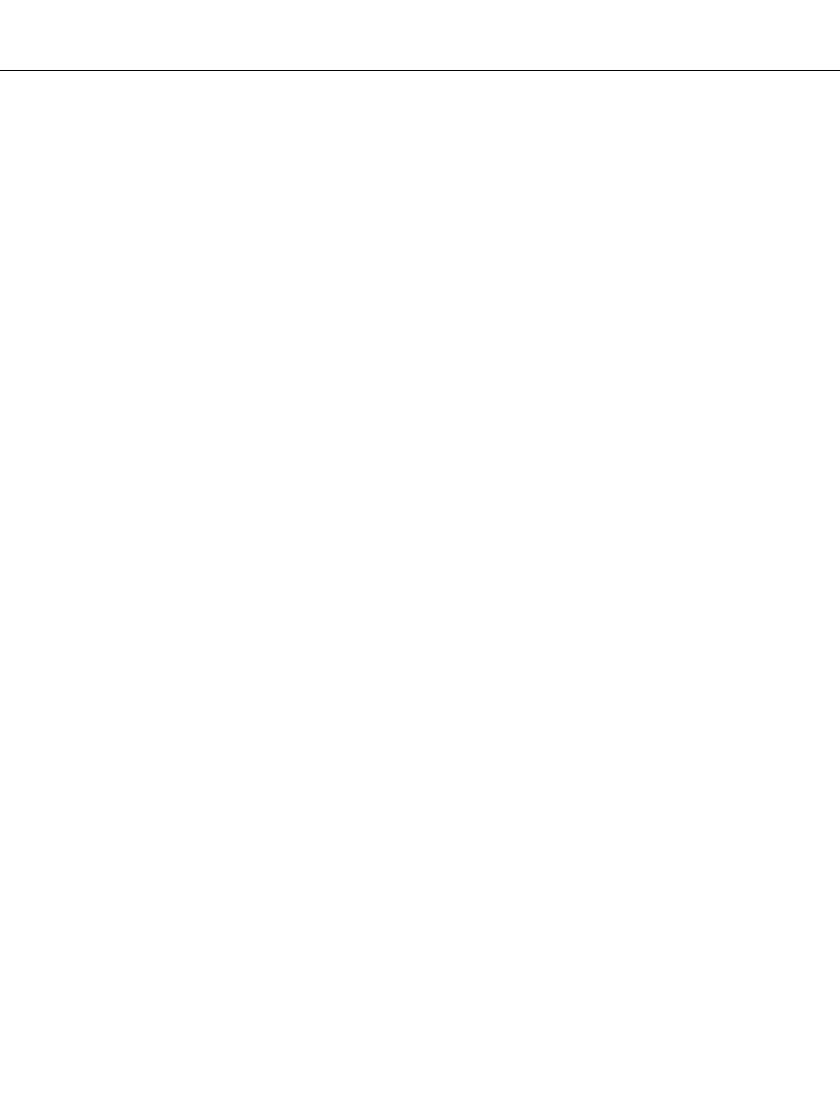
19.6 CHAPTER NINETEEN
19.4 PERFORMANCE CHARACTERISTICS
19.4.1 General
Energy and Power Density. Liquid-electrolyte reserve batteries are not normally rated in
terms of energy or power per unit weight or per unit volume. Because of the need to provide
double the volume for the electrolyte (one volume in an ampoule, the other in the cells
themselves), such batteries are not highly space efficient. Space is also consumed by the
ampoule-opening mechanism and the cell-sealing material. Furthermore, the cell area is
sometimes not exposed to the electrolyte because of the spin eccentricity of the projectile,
which houses the battery. Finally, such batteries are generally designed for short-lifetime
applications, such as the flight time of an artillery projectile (approximately 3 min).
Operating Temperature Limits. Like most other batteries, the performance of liquid-
electrolyte reserve batteries is affected by temperature. Military applications frequently de-
mand battery operations at all temperatures between
⫺40 and 60⬚C, with storage limits of
⫺55 to 70⬚C. These requirements are routinely met by the lead /fluoboric acid/lead dioxide
systems and, with some difficulty at the low-temperature end, by the lithium/ thionyl chloride
and zinc/potassium hydroxide/silver oxide systems. Provision is occasionally made to warm
the electrolyte prior to the activation of the two latter systems.
Voltage Regulation. Since the voltage sustained by a liquid-electrolyte reserve battery at
low temperatures and under heavy electric loading is much lower than that which it delivers
at high temperatures, a serious problem of voltage regulation frequently results. In some
situations, the ratio of high- to low-temperature voltage may be as much as 2:1. This problem
may be avoided by the use of thermal batteries (Chap. 21), which provide their own pyro-
technically induced operating temperature, irrespective of the ambient temperature. Until
recently, thermal batteries were extremely ineffective at high spin rates, but progress has
been made in this field and thermal batteries capable of withstanding spin rates of 300 rps
are now available.
Shelf Life. The shelf life of liquid-electrolyte reserve batteries is highly dependent on the
storage temperature, with high temperatures being the more deleterious. Zinc /silver oxide
cells are probably the most vulnerable of the generally used systems because of the reduction
of silver oxide and the passivation of zinc. Ten-year storage life is probably the best that
can be expected unless the battery is substantially overdesigned. Lead/fluorboric acid/ lead
dioxide batteries also degrade with time, in both the loss of capacity and the lengthening of
activation time. However, if objectionable organic materials are avoided in battery construc-
tion and the battery is designed with some safety factors, 20 to 25 years of shelf life may
be realized. Lithium/thionyl chloride reserve systems are still too new to have a documented
storage history; however, a long storage capability is projected for a properly (dry) built and
sealed battery.
Linear and Angular Acceleration Limits. Since spin-activated batteries are normally ex-
pected to be used in environments where guns are used, they must be built to withstand the
forces of gunfire. With the development of the ampoules and the construction methods de-
scribed, such batteries can withstand linear acceleration to the 20,000 to 30,000-g level and
spin rates as great as 30,000 rpm. The sizes intended for small-caliber (20 to 40-mm) pro-
jectiles will withstand linear g levels 2 to 5 times that high.
As an assist in withstanding these forces, the battery assembly is sometimes encapsulated
in a supporting plastic. A popular design involved a molded plastic cup to house the stack
and ampoule assembly, which was locked in place with an epoxy resin. More recently, the
stack and ampoule assembly has been encapsulated in situ in a RIM (reaction impingement
molding) process using a high-impact polyurethane foam, a process that allows demolding
in just minutes. These two types of support are shown in Fig. 19.5.